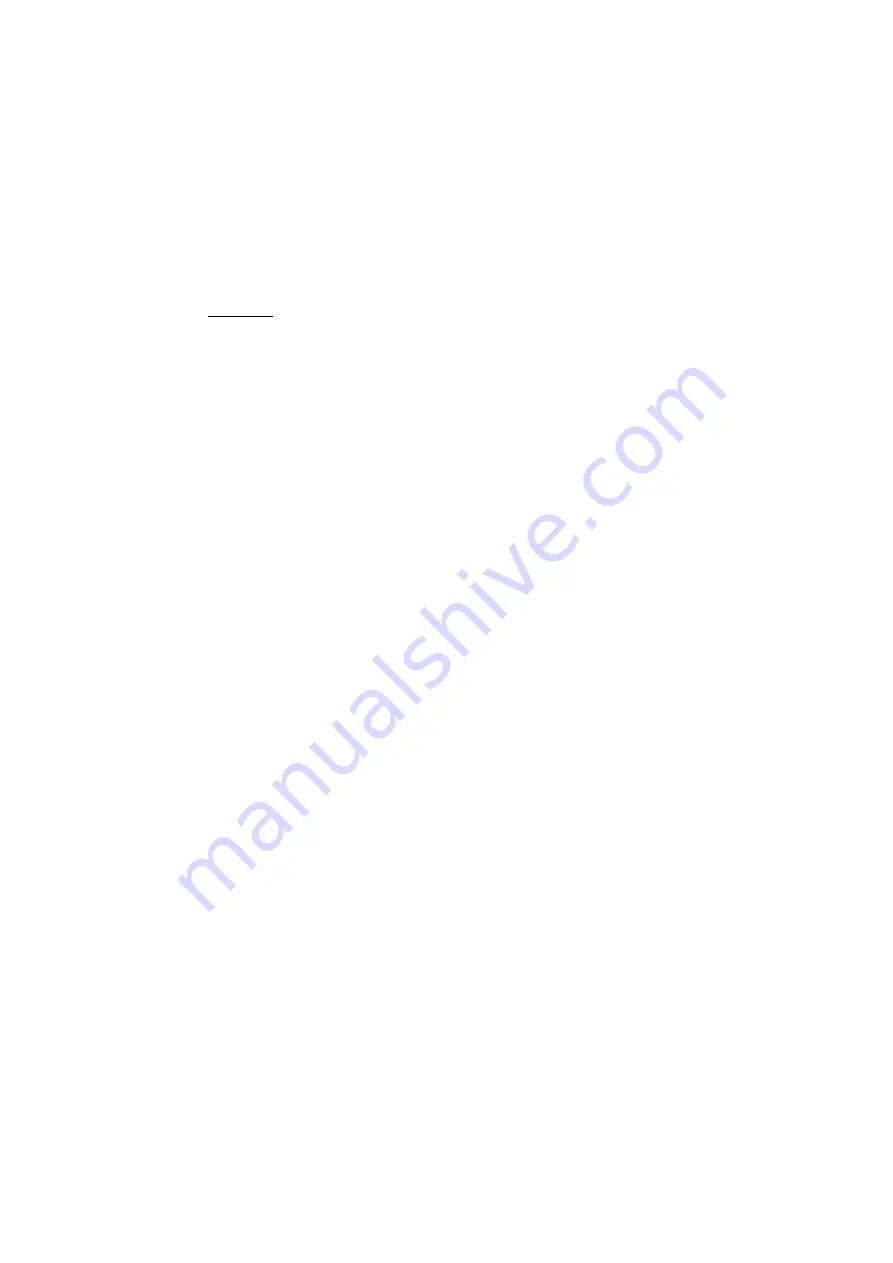
803 B – 04/11 D – pag. 22/24
PFS “B” Frame 4 - Technical specifications
To supply and install, where specified in the project n ..... unit(s) water cooled chiller with cooling capacity of .....
kW, to cool ..... l/sec. of water from ..... °C to ....., condenser entering water temperature ….°C, condenser leaving
water temperature ….°C. The unit should work with electricity at ..... V, 3ph, 50Hz. The electrical power absorbed
should not exceed ..... kW. The units COP will be at least ..... at the working conditions of the project. Part load
COP will be at least ..... at the working conditions of the project. For the units with 1 or 2 compressors the chillers
will have only one refrigerant circuit, and the electronic microprocessor will allow the starting of the compressors.
Each chiller will be factory assembled on a robust baseframe. The unit will be tested at full load in the factory at
the nominal working conditions and water temperatures. Before shipment a full test will be held to avoid any
losses, and the units will be filled with oil and refrigerant.
Refrigerant -
only HFC 134a will be accepted.
Noise level and vibrations
– Sound pressure level at 1 meter distance in free field shall not exceed ………dBA
Vibration level should not exceed 2 mm/s.
Units will have the following components:
Compressors
- The compressor should be single screw type with one main screw rotor that meshes with two
diametrically opposed gaterotors. The two exactly opposed gaterotors create two exactly opposed compression
cycles which results in balanced forces acting on the compressor. The gaterotors should be constructed of a
carbon impregnated engineered composite material. The gaterotor supports will be constructed of cast iron. The
semi-hermetic compressor should be gas-cooled.
Oil injection shall be used for this compressor in order to get high COP at high condensing pressure. The unit
should be provided with an oil separator and it will be the high efficiency, augmented gas impingement type to
maximise oil extraction.
Evaporator
- The units will be supplied with shell-and-tube flooded type evaporator (refrigerant flow in the shell
and water flow in tubes). Replaceable tubes will be fabricated from integral finned copper and mechanically
bonded to steel tube sheet. Refrigerant side will be ISPESL designed, constructed, inspected and stamped. Water
side working pressure should be designed for 10,5 bar. Vessels will include spring loaded pressure relief valves.
Shell and non-connection water heads will be insulated with 3/4 ” thick closed cell insulation.
Condenser –
Condenser will be shell-and-tube type operating with refrigerant in shell and water in tubes.
Replaceable water tubes should be fabricated from integral finned copper and mechanically bonded to steel tube
sheets. Condenser will be designed to conform ISPESL. Water side working pressure should be designed for 10.5
bar.
Servo controlled modulating liquid level regulators -
The refrigerant circuit will be equipped with a modulating
servo-controlled main expansion valve type controlled by a pilot float valve type to perfectly modulate refrigerant
flow to the evaporator, proportionally to the required capacity. This will ensure a stable regulation and economic
operation, because pressure and temperature variations will be strongly reduced.
Modulating condenser water flow valve –
It is factory mounted on condenser outlet water connection, in order to
allow fast and safe unit starting. It is not supplied for condensers with water side pressures higher than 10 bar.
Control panel
- Field power connection, control interlock terminals, and unit control system should be centrally
located in an electric panel (IP 43). Power and starting controls should be separate from safety and operating
controls in different compartments of the same panel. Starting will be star/delta type. Power and starting controls
should include fuses and contactors for each compressor winding. Operating and safety controls should include
energy saving control; emergency stop switch; overload protection for compressor motor; high and low pressure
cut-out switch; compressor lead-lag switch (on 2 compressor units only); cut-out switch for each compressor.
All of the information regarding the unit will be reported on a display and with the internal built-in calender and
clock that will switch the unit ON/OFF during day time all year long.
Regulation of cooling capacity
- Each unit will have a microprocessor for the control and operation of the unit
that should have a infinitely variable capacity control down to 12,5% (two compressors) or to 25% (one
compressor) of the cooling capacity.
Refrigerant piping
- Refrigerant circuit should include a factory insulated suction line, manual liquid line shut-off
valve with charging connection, refrigerant filter drier with replaceable core, sensor indicator, servo controlled
liquid regulator and relief valve.