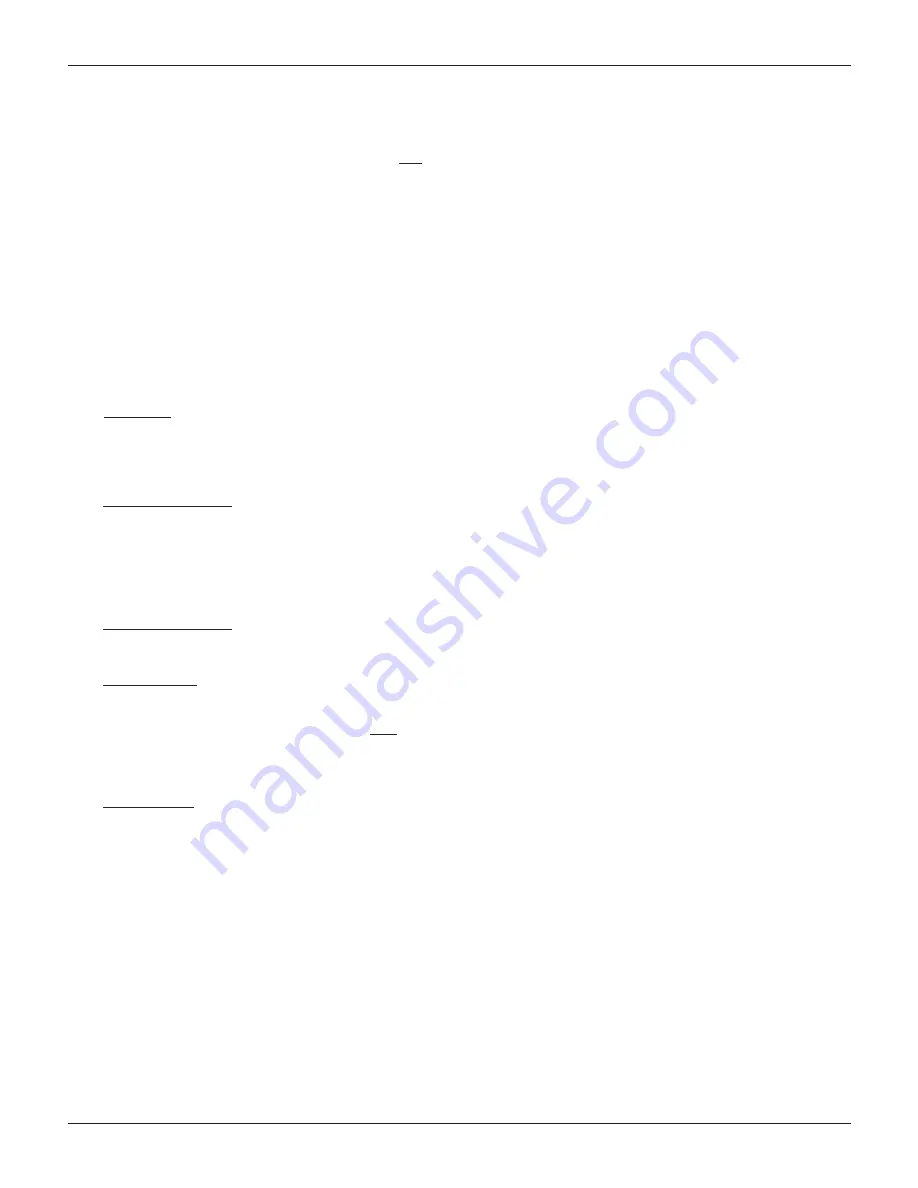
www.DaikinApplied.com 21
IOM 1210-1 • MAGNITUDE
®
MODEL WMC CHILLERS
o
peraTIon
Enabling
To enable the chiller and its compressors when the “Control
Source” is “Switches” or “BAS,” all four rocker switches and
the Remote Switch, if included, need to be closed (in the ON
position).
If the “Control Source” is set to “Local” and a Remote Switch is
being used, the position of the Remote Switch will be ignored.
In that case, only the four rocker switches need to be closed.
Once these four rocker switches are closed, press the AUTO
button on the OITS to enable the chiller in “Local” mode.
Disabling
Each of the four switches located on the unit have a different
functionality in terms of disabling. The descriptions below apply
if the “Control Source” on the OITS MODES Setpoint Screen is
set to “Switches” or “BAS.”
1. Unit Switch- When placed in the OFF position while
the chiller is running, the Unit Switch will shutdown the
chiller in a normal controlled sequence and will stop each
compressor that is running. This switch will leave the
entire chiller disabled until it is set in the ON position.
2. Compressor 1 Switch - When placed in the OFF position,
this switch prevents Compressor 1 from being used
in the normal auto-sequencing of the compressors. If
Compressor 1 is running when this switch is placed in
the OFF position, the compressor will perform a “rapid
stop” different from the stop caused from placing the Unit
Switch in the OFF position.
3. Compressor 2 Switch - This switch functions in the same
manner as the Compressor 1 Switch but it controls
Compressor 2 instead.
4. External Switch - If placed in the OFF position, this
switch will cause both compressors to do a “rapid
stop” together. In other words, putting this switch in the
OFF position has the same effect as placing both the
Compressor 1 Switch and the Compressor 2 Switch in
the OFF position. The External Switch will leave the unit
disabled until it is placed in the ON position.
5. Remote Switch - This switch will disable the chiller in a
similar manner as the Unit Switch.
If the “Control Source” on the OITS MODES Setpoint Screen
is set to “Local,” press the STOP button on the OITS to disable
the chiller. This method of disabling will cause the chiller to act
in a similar manner as when it is disabled using the Unit Switch
in the “Switches” or “BAS” mode.
Operator Interface Touch
Screen (OITS)
The following sections outline the operation of the OITS panel.
OITS On/Off
The OITS is turned on/off with a switch located at the lower
front of the display panel. Screen control buttons are located
to either side of it and elicit on-screen prompts when pressed.
The OITS is equipped with a screen saver (a blank, black
screen) that can be enabled if desired. If the screen is black,
touch it first to be sure it is on before using the ON/OFF button.
Chiller Operation Without the OITS
The Operator Interface Touch Screen (OITS) communicates
with the controller, displaying data and transmitting touch
screen inputs to the controllers. It does no actual controlling
and the chiller can operate without it. Should the touch
screen become inoperable, no commands are necessary for
continuing unit operation. All normal inputs and outputs will
remain functional. The unit controller can be used to view
operational data, to clear alarms, and to change setpoints, if
necessary. See
"The Controller"
section starting on
page 48
for more information.
Navigation Summary
The Home View Screen, see
Figure 16 on page 22
, is
usually left on. This screen contains the AUTO and STOP
buttons used to start and stop the unit when in “Local” control
mode. Other groups of screens can be accessed from the
Home View Screen by pressing one of three buttons on the
bottom of the screen: HISTORY, VIEW, or SET.
• HISTORY: See the
"HISTORY Screens"
section starting
on
page 41
for more information.
• VIEW: See the
"VIEW Screens"
section starting on
page
22
for more information.
• SET: See the
"SET Screens"
section starting on
page
26
for more information.
Figure 15 on page 22
illustrates the arrangement of the
various screens available on the OITS. A few minutes practice
on an actual OITS should provide an acceptable level of
confidence in navigating through the screens.