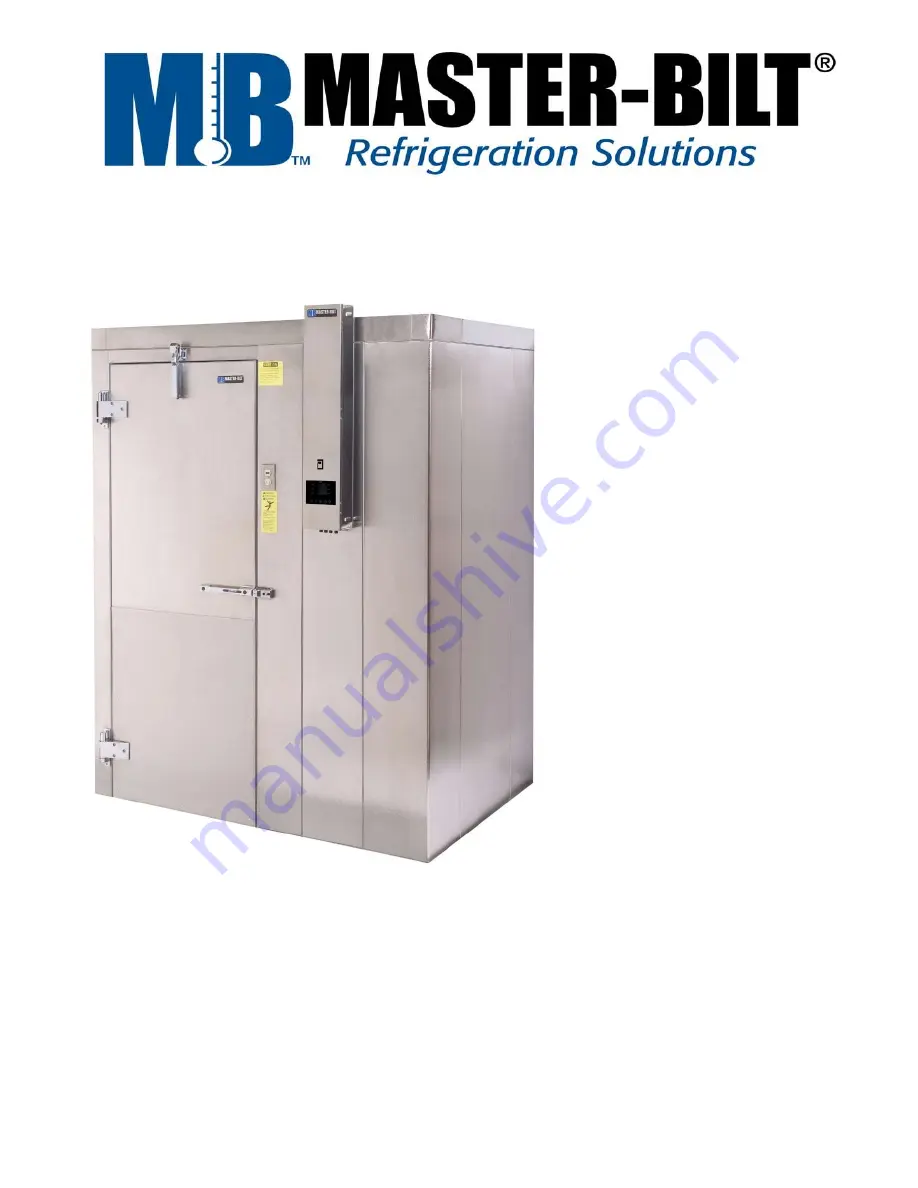
02/20 Rev. B 57-02064
Blast Chiller
Installation & Operation Instructions
MCR/MCF – 33101
MCR/MCF – 33102
MCR/MCF – 33101PT
MCR/MCF – 33102PT
Master-Bilt Products
908 Highway 15 North
New Albany, MS 38652
Phone: (800) 684-8988
©2014 Master-Bilt Products, an unincorporated division of Standex International Corporation. All rights reserved.
Printed in U.S.A.
Summary of Contents for Master-Chill MCR-33-101PT
Page 2: ...2 ...
Page 57: ...57 EVFTFT818 REMOVABLE PROBE ASSEMBLIES EVFTFT818 ...