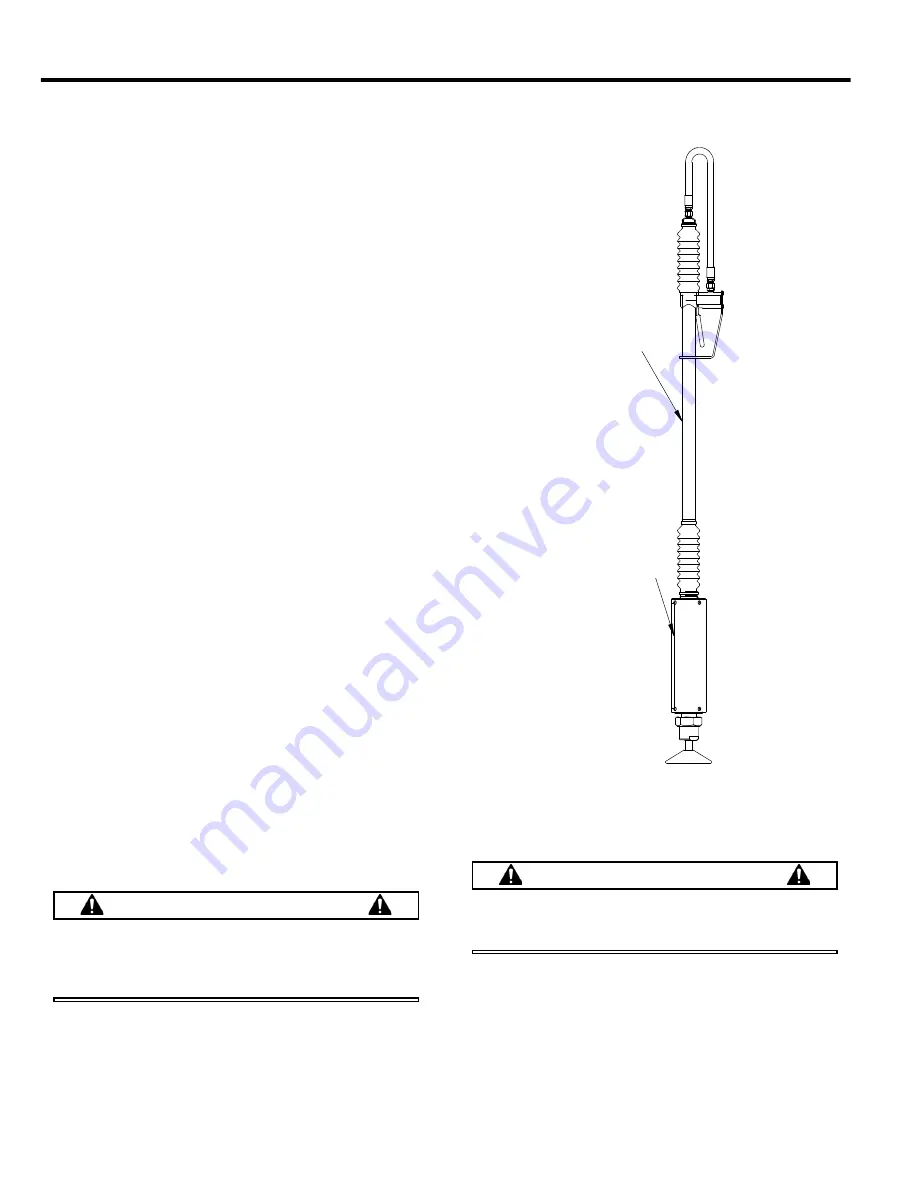
- 4 -
OPERATION
Introduction
MBW equipment is intended for use in very severe
applications. The Ergo-Tamp’s versatility makes it ideal for
small compaction areas while providing MBW’s known
reliability and compaction abilities.
This parts manual contains only standard parts. Variations
of these parts as well as other special parts are not included.
Contact your local MBW distributor for assistance in
identifying parts not included in this manual.
Installation
1.
Remove all pressure from air supply.
2.
Connect air supply to Ergo-Tamp.
3.
Slowly deliver pressure from air supply to Ergo-Tamp.
• Depending on air supply method, adapter(s) may be
needed to make connections.
• To ensure connections do not leak, MBW recommends
using a pipe sealant on the threads of the Ergo-Tamp.
Before Starting & Operating
• REMEMBER! It is the owner’s responsibility to
communicate information on the safe use and proper
operation of this unit to the operators.
• Review ALL of the Safety Precautions listed on page 1 of
this manual.
• Familiarize yourself with the operation of the machine
and confirm that all controls function properly.
• Know how to STOP the machine in case of an
emergency.
• Make sure hands, feet, and clothing are at a safe
distance from any moving parts.
• Verify that all joints are tight.
CAUTION
The MBW Ergo-Tamp should only be run with
clean and dry compressed air. The use of an oil
mist lubrication system is required and will
improve the life of both the tamper and handle.
Operating Ergo-Tamp
WARNING
Follow all recommended operating procedures of
pole tamper manufacturer. Failure to do so could
result in serious bodily injury or death.
1.
Connect air supply hose to Handle Assembly.
2.
Grasp Tamper assembly on the main body of the
Handle Assembly (anywhere between the two
bellows).
+$1'/(
7$03(5
Summary of Contents for ERGO-TAMP
Page 13: ...10 Handle Assembly...
Page 15: ...12 Tamper Assembly...