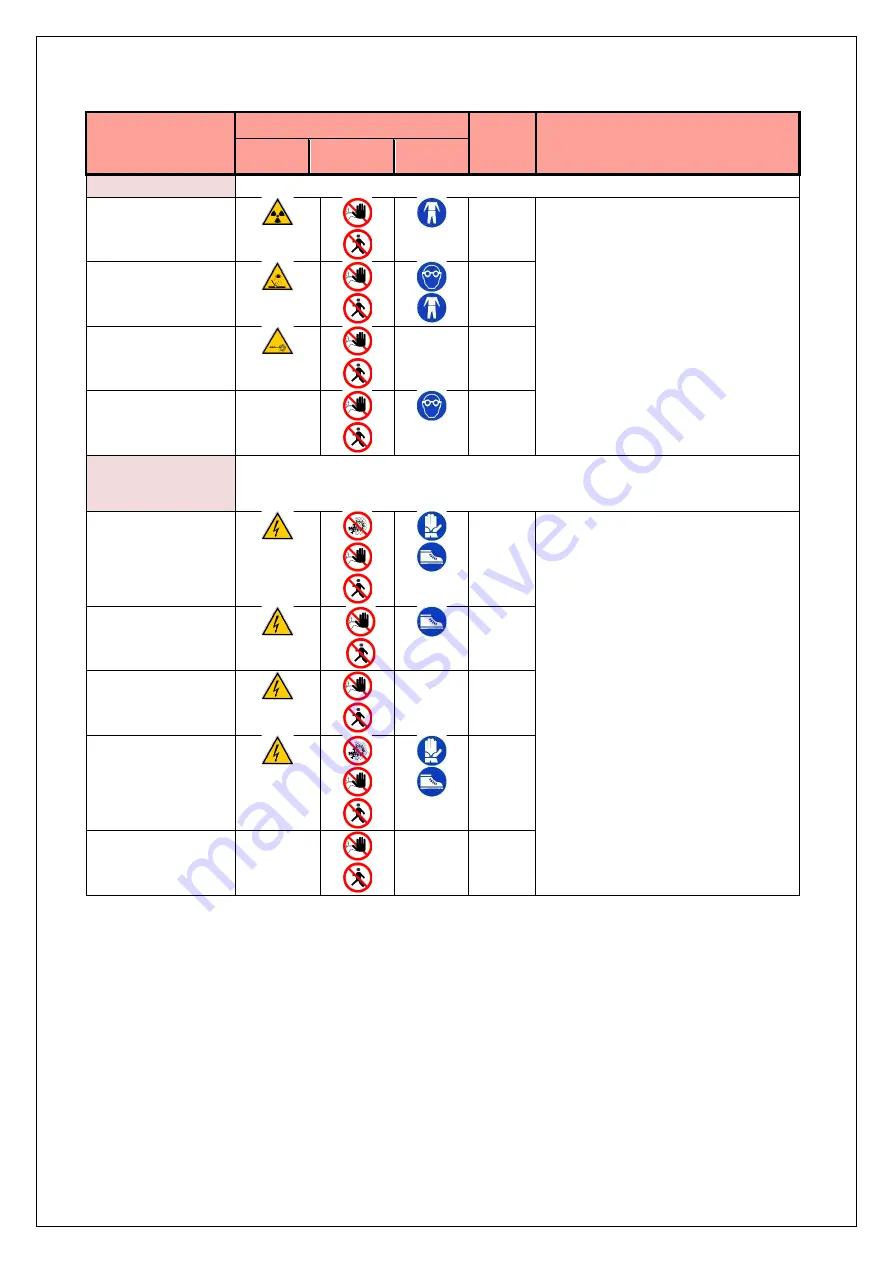
19
RISKS
Reference Signs
SI
Residual Risks
Danger
Prohibition
IPD
RADIATION
Ionizing radiation
Not applicable.
Non-ionizing
radiation, heat, light
Laser equipment
Exposure to
Infrared and
Ultraviolet Rays
DIRECT AND
INDIRECT
ELECTRICAL
Electrocution
caused by direct
and indirect
contacts
Not applicable.
Electrostatic
phenomena
Electric arcs
Injuries caused by
failures in power
supply and/or in the
control system
Exposure to
electromagnetic
fields