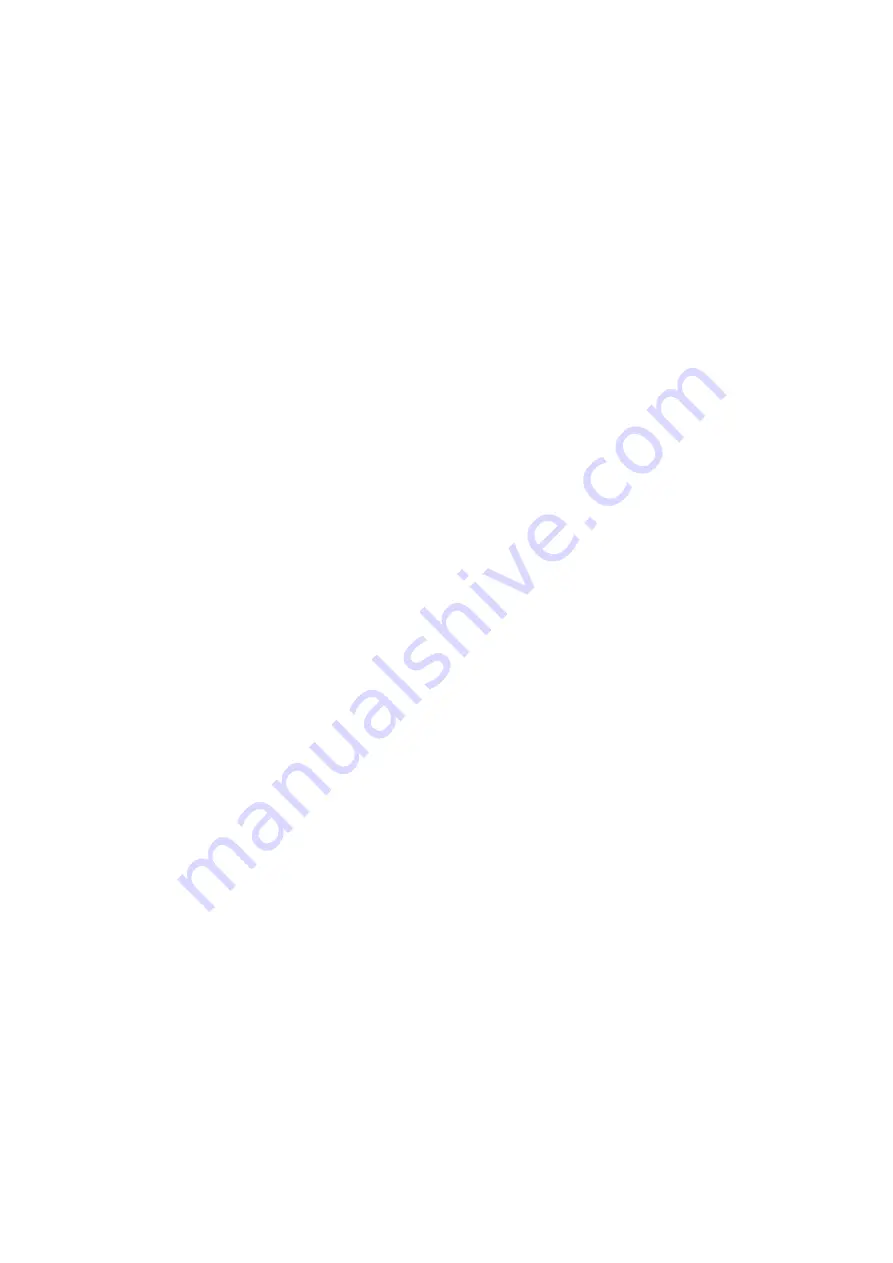
8
3.
General Description
The Split & Merge Station (SPM) is designed for the superimposition of two webs
under web tension. A web duplication is possible on one side of printed or
personalised webs at top speeds. The Split & Merge Station is modularly built and
can be integrated smoothly into the existing system (line). On entry to the Split &
Merge Station there is a "pneumatic pinch roller“, which turns the paper by means of
a switch on the guide roller. The guide roller itself is fitted with an override (free-
wheel) clutch, which prevents the paper web from drawing back into unwind.
The superimposition (longitudinal & transverse registering) is made manually over the
respective setting spindle. A 0-300mm overlap method materialises. Both forms of
production can be processed with the Split & Merge Station (Pin Less or Pin Feed).
The side registering of the slitter unit (LCUM) is set mechanically via a thumb wheel
and /- 5mm. Furthermore, a blade is integrated for the centre cut. Other
blades (LCUM) are available for e.g. edge trim as an option. The guide roller of the
Split & Merge Station is air-cushion supported, which is created by an integrated
compressor. The processing of the superimposed paper web e.g. with an
MBO
sheeter with „chip-out“, necessitates static fixing. This antistatic unit is
supplied as an option.
4.
Installation
In the assembly/disassembly of the Split & Merge Station the trained personnel
should ensure that the machine is arranged horizontally in machine and transverse
direction. Also, the Split & Merge Station must be in direct alignment to the existing
system, because, otherwise this will jeopardise a direct run of the paper web. In
addition, qualified personnel should ensure that sufficient room (e.g. the accessibility
of switch cabinets) is given for maintenance work. From the machine frame to the
ground approximately the same distance should be set over the set-up feet as for the
pre-machine (
MBO
unwind). The reason for this is that the entire system (line) is
aligned at the same height. To unwind there should be a distance of around
30-50cm and to the sheeter 80-110cm. After complete alignment of the Split &
Merge Station the counter nut of the set-up feet should be tightened.
Please follow the safety precautions when performing these operations! (see chapter
1 safety instructions).
The functioning of the Split & Merge Station is checked at the factory and it is packed
professionally. The packaging material shall be disposed, or reused, in accordance
with the applicable terms. You can remove the Split & Merge Station from the
packaging (pallet) with an appropriate lifting column (e.g. forklift truck). Here you
should ensure that no cable etc. is between the fork and frame. Furthermore, it is
mentioned that the centre of gravity of the split & merge station is on the driving side.
This instruction manual is an integral part of delivery. For detailed commissioning of
the antistatic unit we refer to the separate operating instructions.