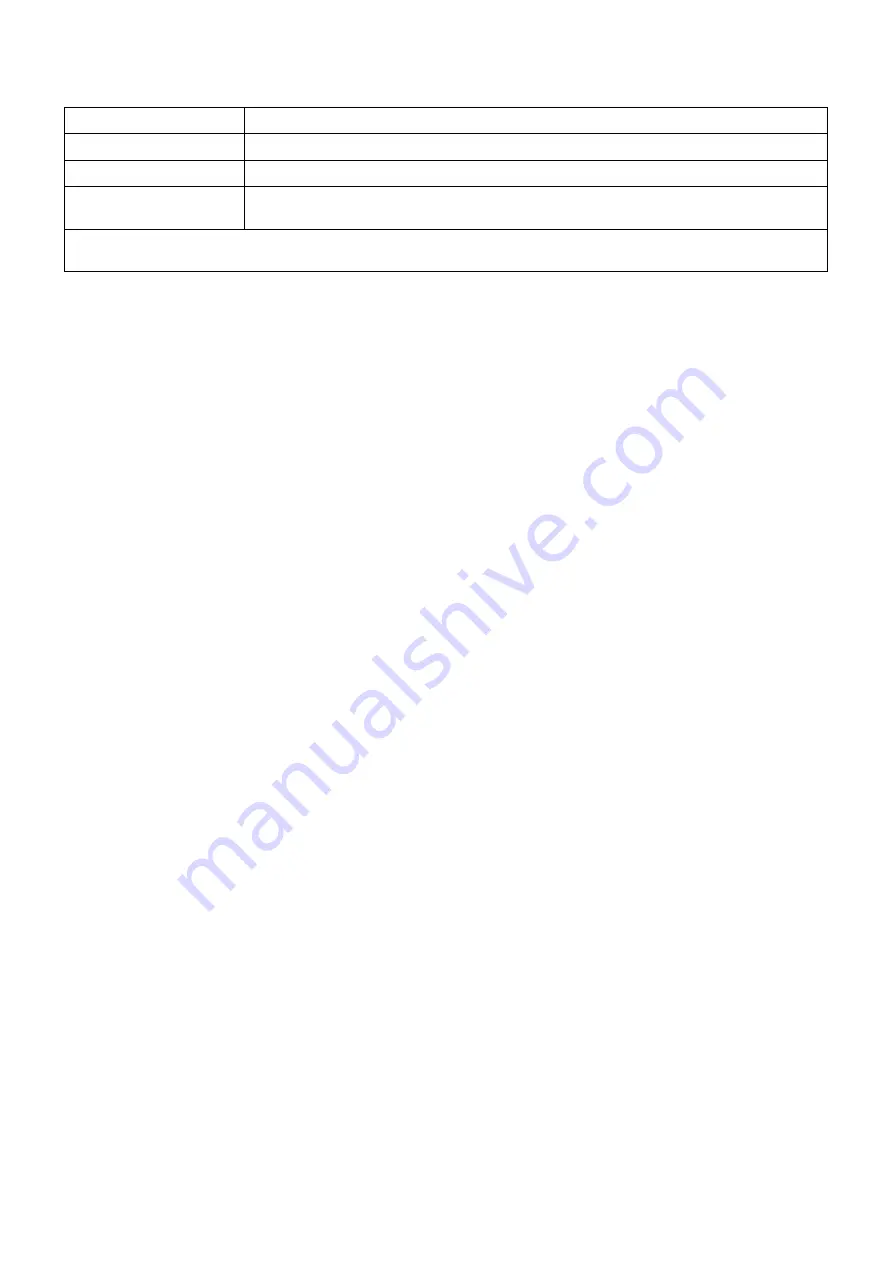
59
࣭
Key operation
Key
Function
1
Increase the number of station by one
4 or 7
Reduce the number of station by one
MODE
࣭
CHECK
RESET
࣭
START
Return to the CHECK mode of the main functions.
Can
’
t Adjustment of the paper feed photo luminescence intensity
12. CHANGING THE SYSTEM PARAMETER
System parameters are aimed at allowing users to adjust the values required for operating the collator
by themselves. While, taking advantage of them, users may optimize the machine operation
according to the environment in which it is used, erroneous setting will cause the machine to
malfunction.
Closest care should be taken when system parameter are changed.
.
12.1 Facts about system parameter
(1) In order to move to system parameter setting mode,
1) Start based on the normal mode
2) Keep pressing [0] key for three seconds
Then, the counter displays [P113] (x represents the current set value)
3)
Press the MODE key to move to next item.
Press the RESET key to move back to the previous item
Press the CHECK key to make a tentative setting
(The set value will return to the initial value when the power supply is cut off).
Press the START key to memorize the set value
(The altered value will be stored even if the power supply is cut off).
Summary of Contents for FC 10 PLUS
Page 1: ... 0 SERVICE MANUAL MBM TABLETOP COLLATOR MODEL FC 10 PLUS R e v 1 0 㻌 㻌 㻌 㻌 Sep 09 2016 ...
Page 7: ...6 䐟㻌 䐠㻌 䐡 䐢 䐣 䐤 䐥 䐦 䐧 䐨 䐩 䐪 䐫 䐯 䐰 䞣 䞢 䞡 䐲 䐱 䞧 䞦 䞥 䞤 䞨 䐬 䐭 䐮 䞪 䞩 䞫 1 2 Operation Panel ...
Page 20: ...19 ...
Page 21: ...20 6 MAIN PRINTED CIRCUIT BOARD ...
Page 22: ...21 7 Wiring Diagram ...
Page 33: ...32 Dismount the clutch holder Dismount the paper feed clutch ...
Page 35: ...34 Lift up the flat idler pulley and slip off the timing belt ...