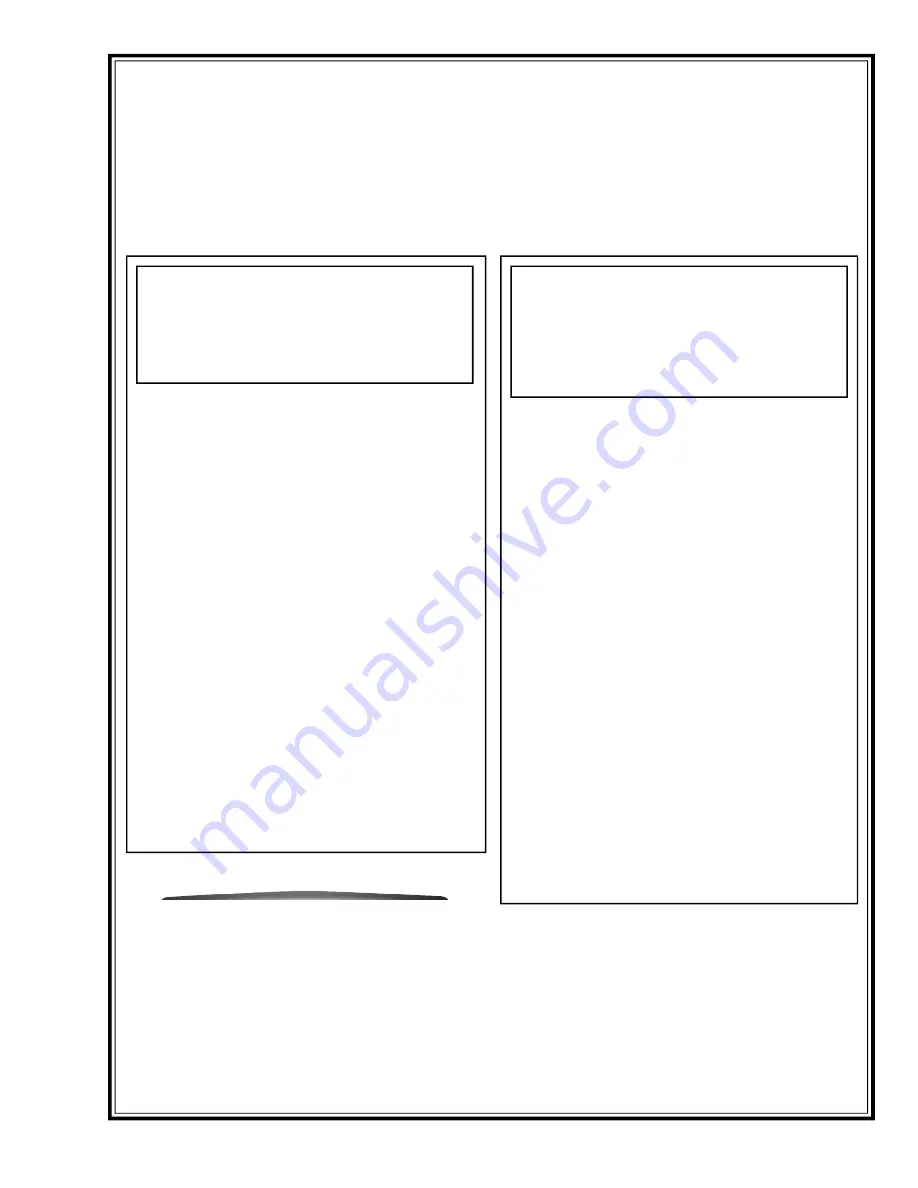
RETAIN THESE
INSTRUCTIONS IN A
SAFE PLACE FOR
FUTURE REFERENCE
MDG-120PHV / MDG-170PHV
Installation Manual
Phase 7 / Non-Coin / Dual Timer
with S.A.F.E. System
Part No. 113395-9
AVERTISSEMENT: Assurez-vous de bien
suivre les instructions données dans cette
notice pour réduire au minimum le risque
d’incendie ou d’explosion ou pour éviter
tout dommage matériel, toute blessure ou
la mort.
—Ne pas entreposer ni utiliser d’essence
ni d’autres vapeurs ou liquides
inflammables à proximité de cet
appareil ou de tout autre appareil.
—QUE FAIRE SI VOUS SENTEZ UNE
ODEUR DE GAZ:
●
Ne pas tenter d’allumer d’appareils.
●
Ne touchez à aucun interrupteur. Ne
pas vous servir des téléphones se
trouvant dans le bâtiment.
●
Évacuez la pièce, le bâtiment ou la
zone.
●
Appelez immédiatement votre
fournisseur de gaz depuis un voisin.
Suivez les instructions du fournisseur.
●
Si vous ne pouvez rejoindre le
fournisseur de gaz, appelez le service
des incendies.
—L’installation et l’entretien doivent être
assurés par un installateur ou un
service d’entretien qualifié ou par le
fournisseur de gaz.
WARNING: For your safety the information
in this manual must be followed to
minimize the risk of fire or explosion and
to prevent property damage, personal
injury or death.
— Do not store or use gasoline or other
flammable vapors and liquids in the
vicinity of this or any other appliance.
— WHAT TO DO IF YOU SMELL GAS:
●
Do not try to light any appliance.
●
Do not touch any electrical switch;
do not use any phone in your
building.
●
Clear the room, building or area of
all occupants.
●
Immediately call your gas supplier
from a neighbor’s phone. Follow
the gas supplier’s instructions.
●
If you cannot reach your gas
supplier, call the fire department.
— Installation and service must be
performed by a qualified installer, service
agency or the gas supplier.
Summary of Contents for MDG-120PHV
Page 46: ...Part No 113395 9 03 26 15 ...