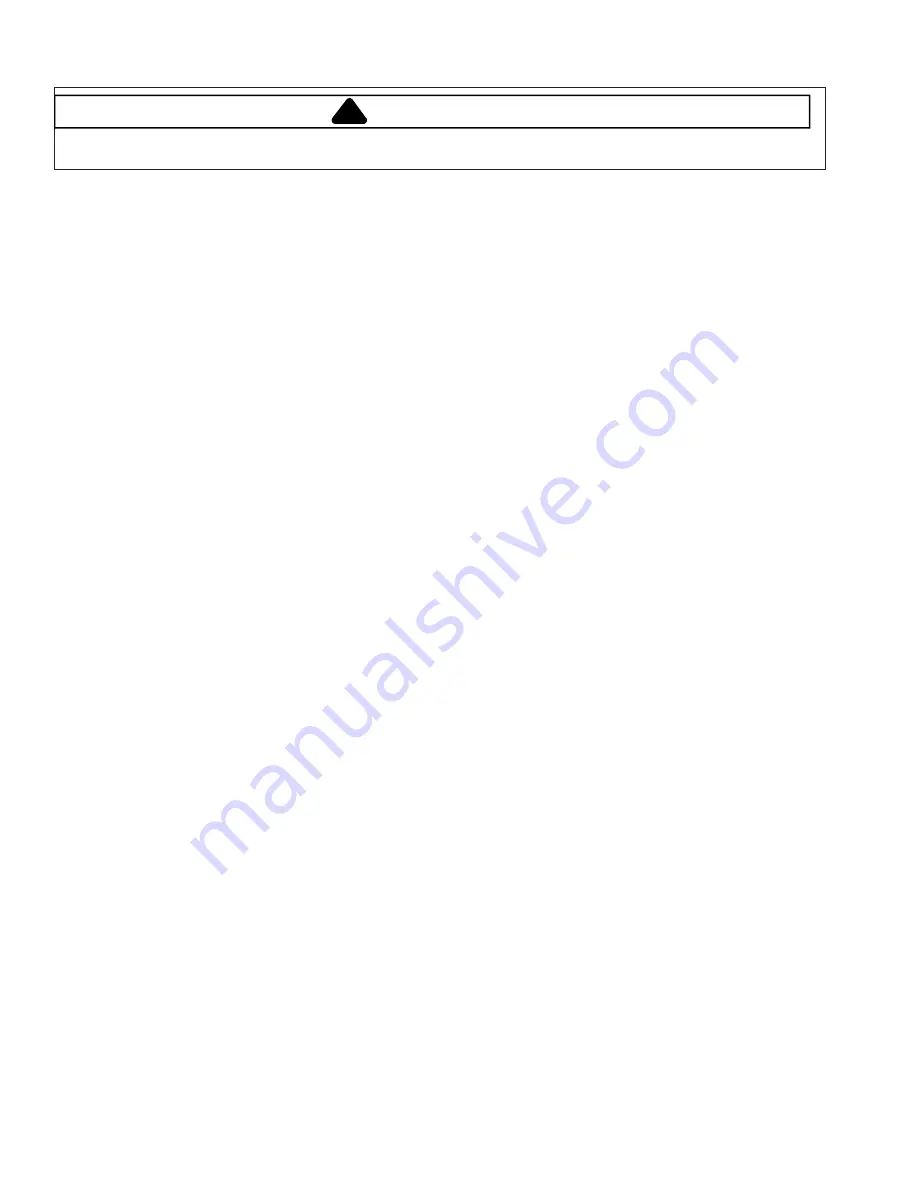
16027402 4
August 2006
©2006 Maytag Services
Leaking
•
Make sure supply hose connections are not
leaking. Check for rubber gasket damage
due to overtightening.
•
Make sure end of drain hose is correctly
inserted and secured to drain facility.
•
Avoid overloading which can push the door
partially open.
•
Check internal hose connections
•
Check tub cover. Remove, reposition and
reinstall the tub cover seal. Seal seam must
be at the top of the tub cover.
Display Lights Up When Door Opened
• This is normal behavior.
No Tumble
•
Washer does not tumble for the first 30
seconds after the door has been opened for
safety purposes.
•
Fabric cycles such as
delicates
and
hand
wash
only tumble for a few seconds every 30
seconds.
•
Check for loose connections at machine
control board, motor control board and
motor.
•
Perform
Motor and Motor Control Test
.
•
Washer does not tumble during some drains
and rinse fills.
No Water Fill
•
Check to make sure water supply turned on
fully.
•
Normal water level is only 2.5 to 5 inches inside
the spinner.
•
Check for kinks in inlet hoses.
•
Check for clogged inlet screens.
•
Visually check hot and cold separately at
dispenser for proper flows.
•
Go to
No Fill Test
page 11.
Noisy
•
Clothes washer should be leveled properly
as outlined in installation instructions.
•
Weak floors can cause vibration and walking.
•
Check for loose lower front bracket.
•
Be sure rubber feet are installed on leveling
legs.
•
Check that the leveling leg lock nuts are
tightened.
•
If complaint is a high-pitched noise during fill
then disconnect supply hoses and clean
screens.
•
Check for proper spring placement of outer
tub support springs.
•
Check strut operation.
Tub is completely full of suds
•
Run the clothes washer through another
complete cycle using cold water and no more
detergent.
•
Reduce detergent amount for that specific load
size and soil level. Towel loads have a minimal
amount of soil present and typically create more
suds.
•
Use high efficiency or low sudsing detergent
specially formulated for front load washers.
•
Check for restricted drain system.
•
Check for loose wire connections at control
board and pump.
•
Check to see if belt fell off motor and pulley.
•
Perform
Motor and Motor Control Test
.
Troubleshooting Procedures
!
WARNING
To avoid risk of electrical shock, personal injury or death; disconnect power to washer before servicing, unless
testing requires power.