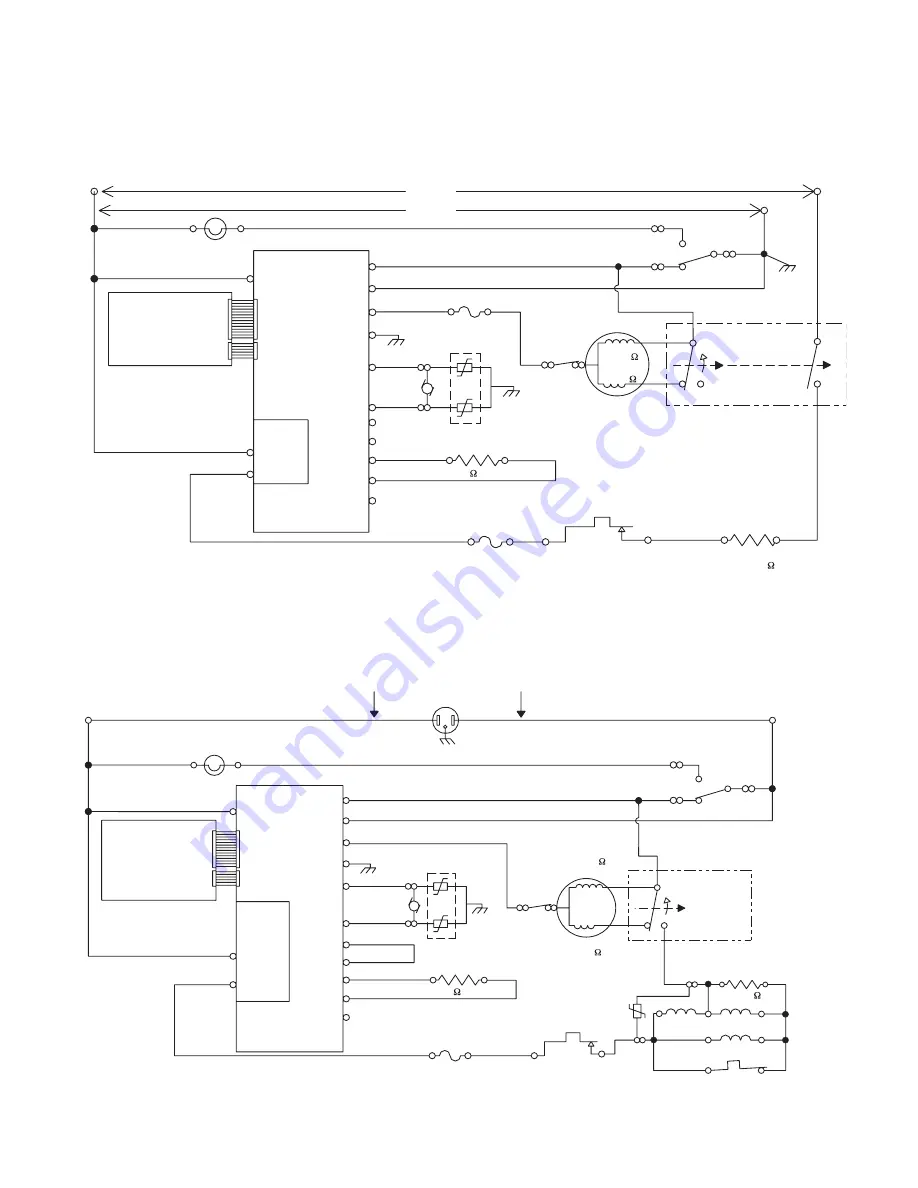
7-1
WIRING DIAGRAMS
ELECTRIC DRYER
GAS DRYER
120 VOLTS
240 VOLTS
L1 LINE BK
R
LINE L2
W
NEUTRAL
2M
1M
DOOR
SWITCH
R/W
NC
DRIVE MOTOR
1/3 H.P.
4M
MAIN
START
5M
6M
THERMISTOR
BK
DL
HEATER
R
BK
CONTROL
THERMAL CUT-OFF
(TCO) 352
°
F (178
°
C)
NEUTRAL
TERMINAL
LINKED TO
CABINET
CENTRIFUGAL SWITCH
THERMAL FUSE
196
°
F (91
°
C)
HIGH LIMIT
THERMOSTAT
295
°
F (146
°
C)
DOOR
DRUM LAMP
MOIST RTN
MOIST.
TEMP.
SENSOR
NC
3M
NO
COM
G
BU
BK
R
BR
LT BU
LT BU
BELT
SWITCH
W
MODEL RTN
L1
USER INTERFACE
(ACTIVE OVERLAY or
ALTERNATE TECHNOLOGY)
MOTOR
HEATER RTN
V
10k
± 3%
P3
P4
P1-3
P2-1
P2-2
P2-5
P2-4
P1-4
P1-5
HEATER
RELAY
NEUTRAL
P1-2 NEUTRAL
MODEL
P2-3
N.O.
(0.250 TERMINAL)
COM
(0.250 TERMINAL)
N.C.
TEMP RTN
P2-6
P2-7
G
SENSOR
MOVS
G/Y
P1-1
Y/R
BK
R/W
BK
W
7.8 - 11.8
BU
W
2.4 - 3.8
2.4 - 3.6
ELECTRONIC
FS2
FS1
VALVE NO. 1
IG
IGR
IGNITOR
50 - 500
HOLD
ASSIST
MAIN
22,000 BTU/HR
VALVE NO. 2
4
1
3
2
5
FLAME SENSOR
4M
5M
6M
DL
NC
3M
3V
1V
HS1
91
°
C (196
°
F)
96
°
C (205
°
F)
HS2
TF1
TF2
TEMP.
L1
HEATER RTN
V
10k
±3%
P3
P4
P1-3
P2-5
P2-4
P1-4
P1-5
HEATER
RELAY
P1-2
P2-3
N.O.
(0.250 TERMINAL)
COM
(0.250 TERMINAL)
N.C.
P2-6
P2-7
P2-1
P2-2
VALVE MOV
P1-1
BK
L1 LINE
BK
ELECTRONIC
CONTROL
DOOR
DRUM LAMP
MOIST.
NEUTRAL
MOTOR
PLUG
5 -15P
GND
USER INTERFACE
(ACTIVE OVERLAY OR
ALTERNATE TECHNOLOGY)
MODEL
MOIST. RTN
TEMP. RTN
MODEL RTN
120 VOLTS U.S.
LINE L2
R
W - NEUTRAL
DOOR SWITCH
START
THERMISTOR
CENTRIFUGAL
SWITCH
THERMAL FUSE
HIGH LIMIT THERMOSTAT
SENSOR
W
NEUTRAL
BELT SWITCH
W
SENSOR MOVS
GND
MAIN
DRIVE MOTOR - 1/3 H.P.
NC
NO
COM
2.4 - 3.6
2.4 - 3.8
BU
BU
W
LT BU
BR
BK
BK
G/Y
Y/R
BK
R/W
BK
BU
R
R
115 VOLTS CANADA
LT BU
Summary of Contents for Epic MED/GD9600S
Page 4: ... iv NOTES ...
Page 45: ...4 16 Squeeze Arms 8 Squeeze the locking arms and remove the socket from the drum light holder ...
Page 71: ...6 14 NOTES ...
Page 73: ...7 2 NOTES ...
Page 75: ......