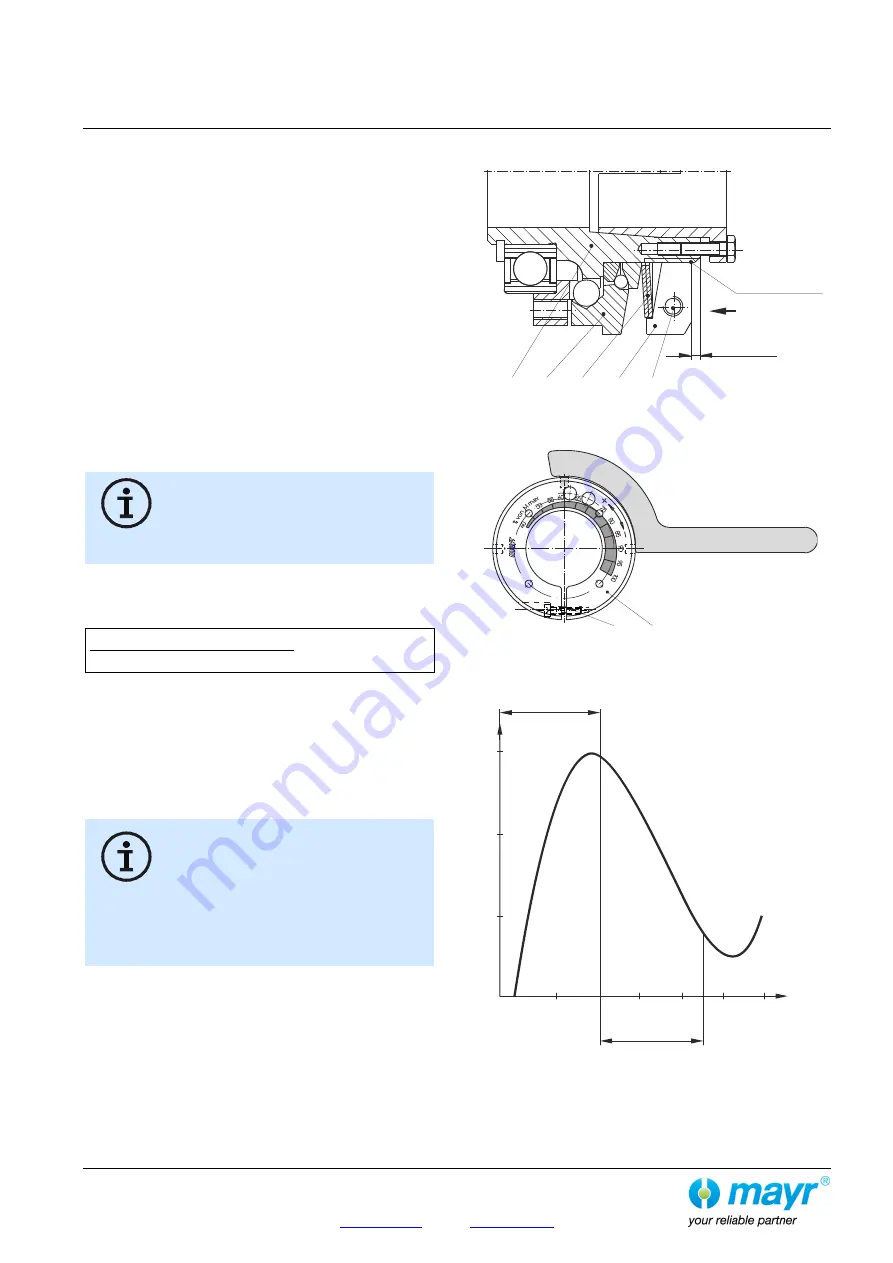
Installation and Operational Instructions for
EAS
®
-Compact
®
overload clutch Type 49_._ _4._
Sizes 01 to 3
(B.4.14.1.EN)
13/11/2017 GC/NU/GH/SU
Chr. Mayr GmbH + Co. KG
Eichenstraße 1, D-87665 Mauerstetten, Germany
Tel.: +49 8341 804-0, Fax: +49 8341 804-421
Page 14 of 19
Torque Adjustment
In order to guarantee low-wear clutch operation, it is essential
that the clutch torque is set to a sufficiently high service factor
(overload torque to operating torque).
Our experience has shown that an
adjustment factor of
1.5 to 3
gives good results.
On very high load alternations, high accelerations and irregular
operation, please set the adjustment factor higher.
Torque adjustment is carried out by turning the adjusting nut (4).
The installed cup springs (9) are operated in the negative range
of the characteristic curve (see Fig. 12); this means that a
stronger pre-tensioning of the cup spring results in a decrease of
the spring force.
The torque is set manufacturer-side according to the customer's
request.
If no particular torque adjustment is requested customer-side,
the clutch will always be
pre-set
and
marked
(calibrated)
manufacturer-side to approx. 70 % of the maximum torque.
It is possible to check the
"Spring operation in the operating
range"
(Fig. 12) using the dimension "a" (distance from the
adjusting nut (4) facing side to the hub (1) facing side, as shown
in Fig. 10).
Please see Table 3 for the respective values.
Turning the adjusting nut (4) clockwise causes
a reduction in torque.
Turning it anti-clockwise causes an increase in
torque.
You should be facing the adjusting nut (4) as
shown in Fig. 10 and Fig. 11.
Changing the Torque
a) Please convert the required torque using the formula below
into percent of the maximum adjustment value (see Table 3).
Required torque adjustment
x 100 = Adjustment in %
max. adjustment value
b) Loosen the locking screw (5) in the adjusting nut (4).
c) Turn the adjusting nut (4) using the engraved adjustment
scale (Fig. 11) clockwise or anti-clockwise using a hook or a
face wrench until the required torque is reached.
d) The required torque results from the marking overlap on the
hub (1) and the percent value on the adjusting nut (Item 4 /
Figs. 10 and 11).
e) Re-tighten the locking screw (5)
(please observe the tightening torque acc. Table 5).
Adjusting the adjusting nut (4) or distorting the
cup spring (9) outside of the cup spring
characteristic curve (see Fig. 12) stops the clutch
functioning.
The inspection dimension “a” (see Table 3) can
show deviations due to construction tolerances or to clutch
wear. After de-installing the clutch
(e.g. due to cup spring replacement or changes to the cup
spring layering), the clutch must be re-adjusted and calibrated
using dimension "a" (see Table 3 and Fig. 9).
Fig. 10
Fig. 11
Fig. 12
5
9
3
1
4
5
4
Marking
Facing direction
Dim. “a”
Hook wrench
Move to
operating range
Graph of spring
characteristic
curve
Operating
range
Spring path S
F
orc
e F