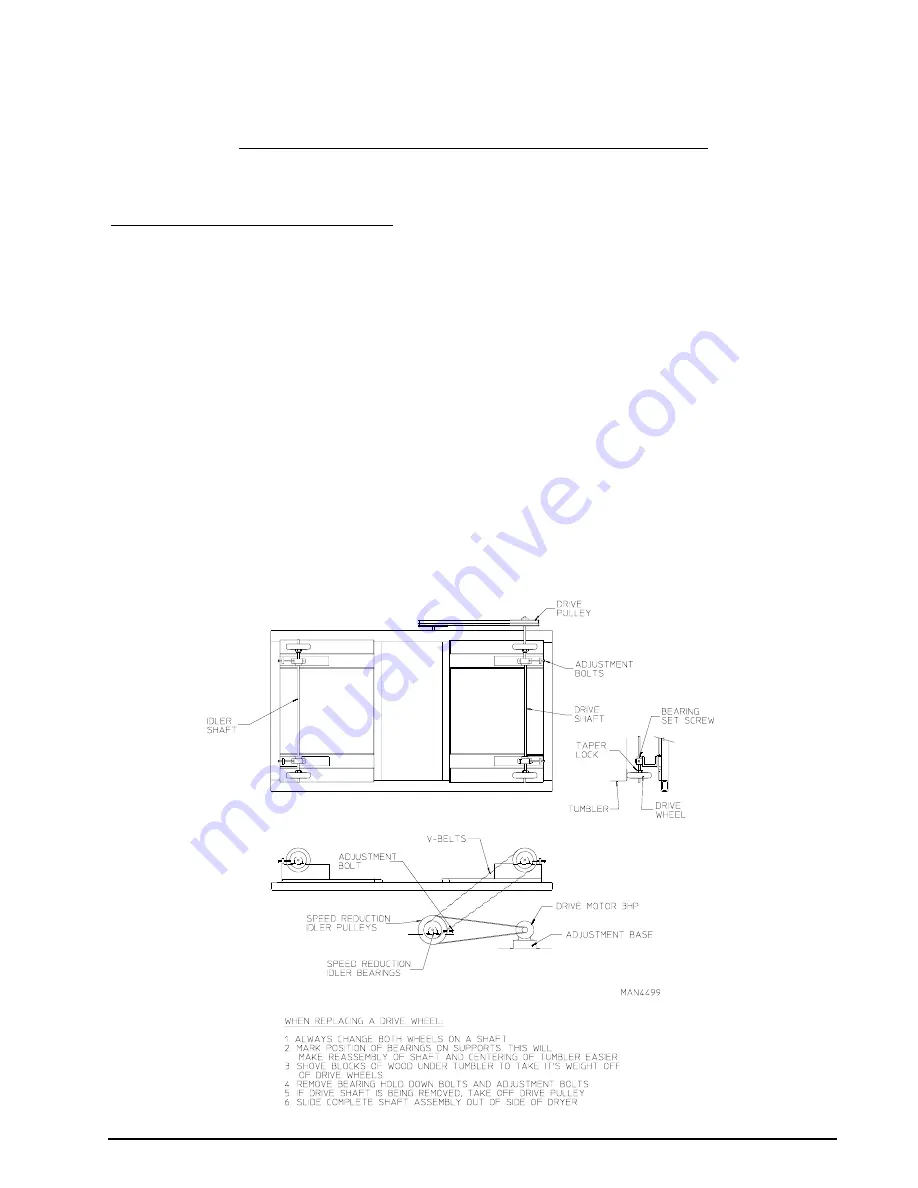
113274 - 1
47
SECTION VII
COMPONENT SYSTEM DESCRIPTIONS
A. TUMBLER DRIVE SYSTEM
The tumbler is supported and driven by four (4) 11-inch diameter drive wheels. Two (2) of these wheels are
attached to a 1-1/2” diameter idler shaft, while the other two (2) are attached to a 1-1/2” diameter drive shaft.
Each of the wheels is fastened to the shafts by a taper lock bushing. The taper lock is made up of three (3)
pieces: an inner collar, an outer sleeve, and a key. The inner and outer elements have matching opposing tapers.
As a result, when the bolts are tightened, the taper lock contracts onto the shaft and expands into the drive wheel
hub locking the wheel onto the shaft.
The idler shaft and drive shaft are each supported by two (2) 1-1/2” diameter pillow block bearings. These
bearings sit on slotted support channels and can be moved inward or outward by the adjustment bolts to raise or
lower the tumbler.
The drive system consists of a shaft mounted pulley, two (2) V-belts, and a 3 hp (2.24 kW) drive motor. Belt
tension can be adjusted by tightening or loosening the gear reducer turnbuckle.
TUMBLER DRIVE SYSTEM
Summary of Contents for MAXIMD200
Page 11: ...113274 1 7 B DIMENSIONS AND COMPONENT LOCATION NON TILT GAS MODEL...
Page 12: ...8 113274 1 NON TILT STEAM MODEL...
Page 14: ...10 113274 1 1 Reassembly Instructions For Gas Dryer Shipped In Two 2 Pieces...
Page 16: ...12 113274 1 2 Reassembly Instructions For Steam Dryer Shipped In Two 2 Pieces...
Page 22: ...18 113274 1...
Page 23: ...113274 1 19...
Page 24: ...20 113274 1...
Page 64: ...Part No 113274 1 05 17 11...