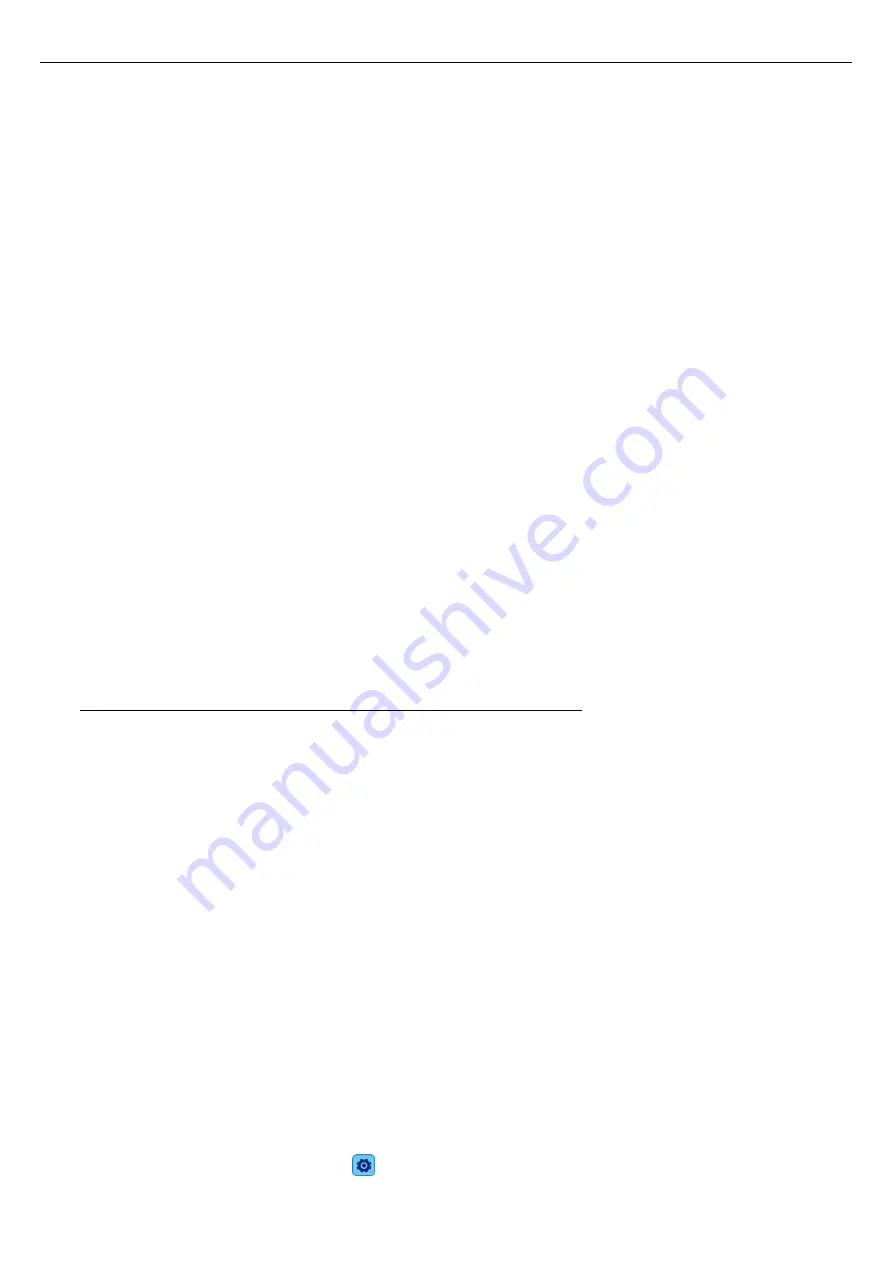
Hi-T2
Centralised controller
20
intervention of the chillers change, by rotating the decalibration of the set point of the chillers, in order to balance the load on the
various machines. If a chiller is in alarm, it is excluded from the regulation. By default
Par 8/65=0
.
4.2
CHILLER/HEAT PUMPS MANAGMENT
Up to 7 chillers (I-32V5) can be controlled by the Hi-T2 remote control. The main functions that can be adjusted are:
•
ON/OFF command;
•
Change of season (summer, winter, summer with DHW mode, winter with DHW mode, DHW mode);
•
Set-point setup;
•
Display of current alarms;
•
Alarm history residing in the keyboard with the date and the time of the event;
•
Access to the parameters of the chiller (password protected);
•
Display of the main statuses of the chiller;
•
Weekly programming in summer, winter, DHW mode and of the legionella disinfection cycle.
4.2.1
ENABLING INDIVIDUAL CHILLERS FOR DHW PRODUCTION
Among the chillers (in the network) that are enabled to produce domestic hot water, you can choose using the appropriate sub-
menu in “
Status setup
”, which of these may participate in DHW production (see Paragraph 4.6.2). Only those selected will be
enabled for the production of DHW, all the others are used exclusively for the plant.
4.3
MANAGEMENT OF FAN COIL UNITS
With the Hi-T2 remote control panel, we can manage up to 80 fan coils of our production equipped with an RFC module, divided
into a maximum of 9 zones. Note that the fan coil settings can be done for individual zones (not for individual units). The main
functions that can be adjusted are:
-
ON/OFF (of the system and/or of the zone with relative scheduler);
-
Season (of the system);
-
Fan speed (fan coil of the zone);
-
Dehumidification control.
The set-point will be sent also to the fan coils of the zone they belong to. Note that a correction can be made locally by means of the
fan coil’s knob.
4.4
INITIAL CONFIGURATION PROCEDURE OF Hi-T2 REMOTE CONTROL PANEL
Note: For easier installation and interfacing of the keyboard with the hydronic terminals, it is recommended to separately power on
the terminal units; each terminal unit must be cut off by its own disconnector.
4.4.1
ADDRESSING
During the first startup step, it is necessary to power on each hydronic terminal separately. The addressing process takes place
respecting the following steps:
1.
a unique address should be assigned to each water terminal unit on the network, to do this, you can use the dip switches
situated on the RFC module (first valid address is the value 10). See the relative manual (MCO01137I0300 FAN COIL
REGULATOR).
In the case of addressing beyond the value 32, it is necessary to set an address lower than 32 using the dip-switches and acting on
the parameter 23 of the concerned fan coil. Once the parameter has been configured, set the dip switches in a definitive way and
restart the water terminal unit. See the relative manual (MCO01137I0300 FAN COIL REGULATOR).
2.
Each fan coil must have a unique address. It is important to assign consecutive addresses to the fan coils of the same zone
(e.g. if there are 3 fan coils inside the same hall and you want to associate them to a single thermal zone called for example
HALL, you need to assign the fan coils with a series of addresses from 10 to 12, etc.);
3.
once all the fan coils have been configured, they should be powered on;
4.4.2
NETWORK SCANNING
Once the addressing has been done for each fan coil, it is necessary to perform a network scanning to check if all the fan coils are
correctly recognised. To do this:
1.
power on all the fan coils;
From the system main page, go to “
Configuration
“
;