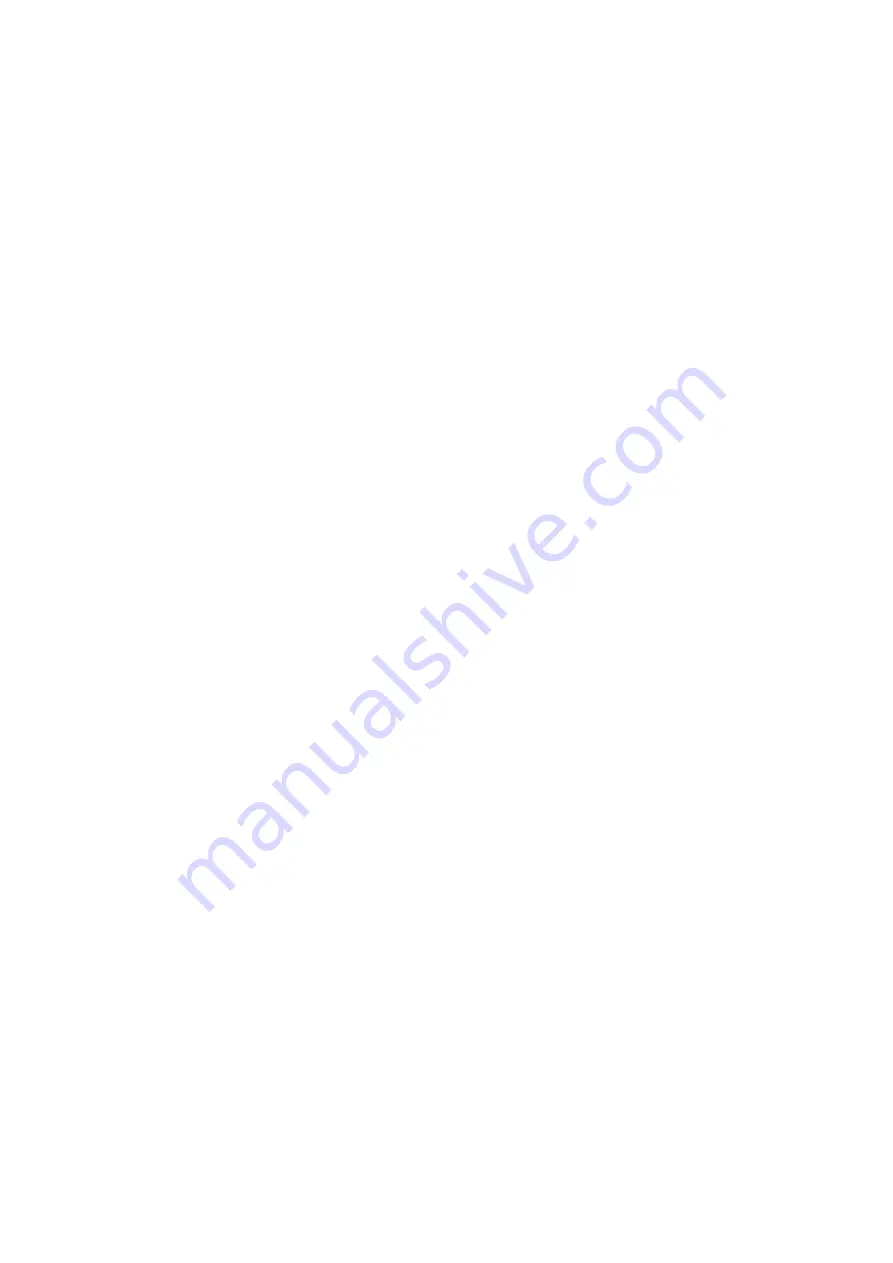
MAX POWER
FINAL FITTING OF THE RETRACT UNIT TO THE MOUNTING BASE
CAUTION: To ensure absolute cleanliness, hydraulic lines and ports must remain
plugged until final connection.
Final installation on the mounting base must be made after thoroughly cleaning and
then liberally coating both joint surfaces (case and base) with good quality marine
grease. This is so that the « O » ring seal is compressed flat, evenly, smoothly and
squarely when the bolts are tightened.
CAUTION: Under no circumstances should the RETRACT be glued or bedded down
with a marine type mastic/glue such as Sikaflex or other similar product.
The flange bolt should be tightened sequentially and in successive passes until the
two surfaces touch. If desired, a torque wrench can be used and the bolts can be
tightened to a torque of 5,0 kg/M. The flange bolts should be metric size 12 mm of
stainless steel, and should have a large stainless steel washer placed above a nylon
washer. The nylon washers avoid stainless steel contact with the aluminium case.
The nuts should be NYLOCK self-locking type.
The 4 lifting lugs provided by MAX POWER, should be put in a small plastic bag,
along with the hydraulic pipe plugs, for storage and future use by the ships crew .
FINAL ADJUSTING OF THE CLOSING PLATE
(See drawings N°4 & N°3)
Once the thruster is permanently bolted onto the mounting base, reinstall the plate
and check it’s adjustment.
The turbine is naturally
closed
at rest because of the gas spring used in the lifting
mechanism .It is the force of this spring that
most of the time
holds the plate closed
Adjust the closing plate so that it fits evenly and squarely in its hull recess
.
When testing the cover plate fit, use the manual lower mechanism.
Two rubber blocks have been placed on the top of the turbine to help adjust the
closing plate in the correct position.
Tighten its fixation bolts (A) then remove the rubber blocks. (Drawing n°3 fig 2)
Be sure that it is the gas spring holding it in place, and that the thruster
is not fully
folded with the plate shut
(see drawing n°3 Fig 1)
The closing plate could however
open at sea
because of aqua dynamic forces or
because of down ward momentum.
The thruster is therefore fitted with a mechanical locking device.
(See drawing N°2)
Although the RETRACT R450 is delivered completely tested and folded in the folded
UP position, the locking slide bar cannot be definitively adjusted at the factory.
Adjustment has been set at the factory in the medium position
- 7 INSTALLATION MANUAL RETRACT R 450