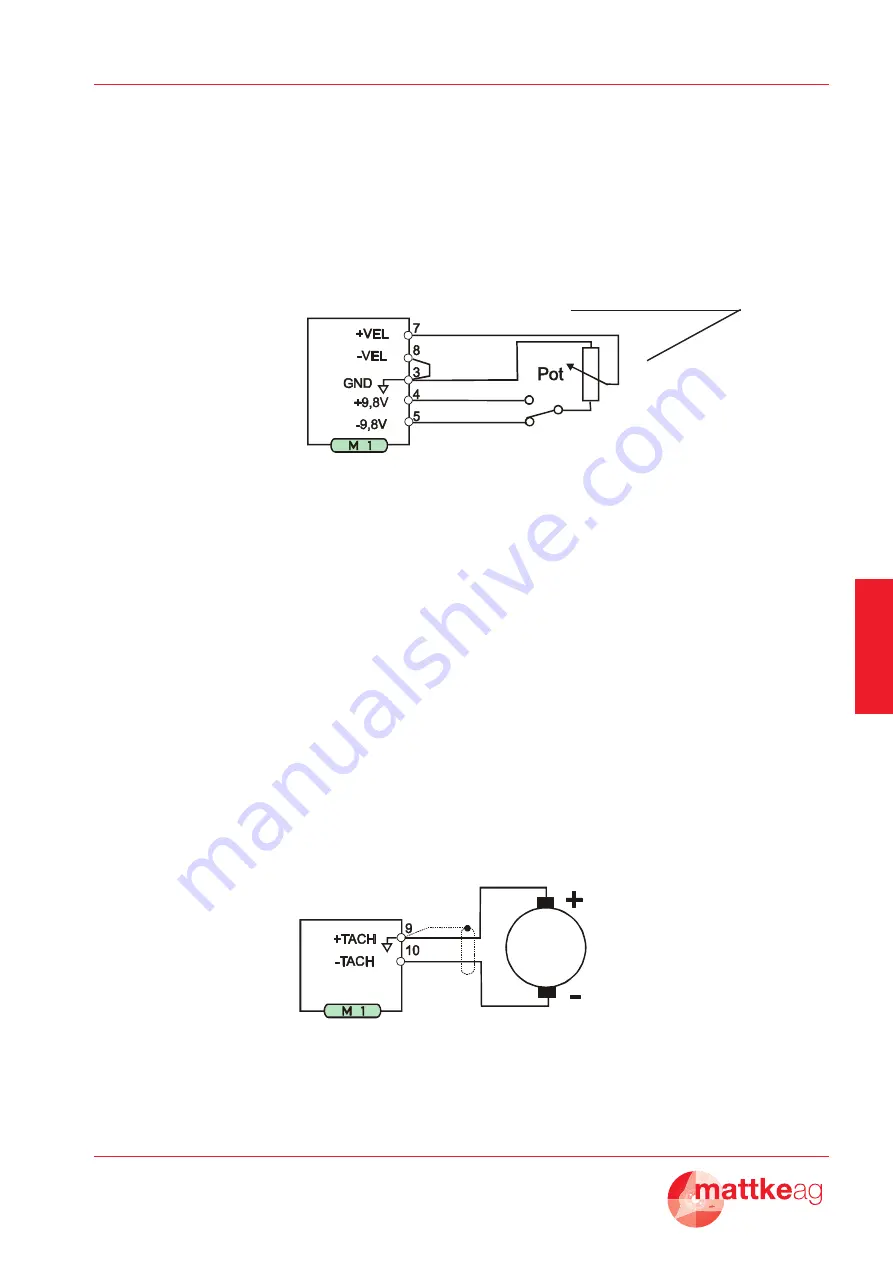
15
The following diagram shows an application utilizing a differential reference from a C.N.C
The +/-VEL in differential mode has a 40Kohm of impedance input.
Speed potentiometer
The following diagram shows an application using speed reference connections from C.N.C in the
Common Mode. This analog in common mode has a 20Kohm of impedance input.
The following figure shows an application with speed reference connections using an in/-9.8V
power supply.
The speed potentiometer must have an included value between >5 and <10Kohm.
Speed reference from external potentiometer
The following figure shows an application with speed reference connections using an internal
+/-9.8V power supply.
The speed potentiometer must have an included value between >5 and <10Kohm.
2.7 Tachogenerator input
Tachogenerator input (M1 signal terminal pin 9 and 10)
The following diagram shows the connection from tachogenerator and the drive DC ONE.
This function is enabled through the following settings on the solder point, and the insertion
of RDT resistance on the adjstustement zone. +TACH „pin 9“ corrisponds to power supply’s
negative GND input.
Connect the negative of tachometer to pin 10. Do not exceed voltage as input from tacho
value of 50V. Example: If you use a 10V/KRPM no more than 5000rpm.
If the motor rotates in an opposite direction to the expected one,switch off and reverse the
motor and tachogenerator connections.
View the connections and settings from tachogenerator in chapter 4.2
In the terminals 2 and 3 you can connect the inputs from an incremental encoder for the current
feedback in response to encoder. Signals can come from encoder powered from +5V to +24V).
Minimum high logic level >+2.8V/24Vmax,
Minimum low logic level <1.5V
Encoder can be connected either push-pull (wires A, B and GND) or line-driver encoder type (wires
+ A + B and GND). Remember to connect the zero encoder with the GND power converter.
View the connections and settings from encoder in chapter 4.1
On the terminal (+V) is available auxiliary power supply v5V (+12 V on request order). This
output can be used to power the encoder on the motor. The capacity of the output current is
130mA max.
The following diagram shows the connection from tachogenerator and the drive DC ONE.
This function is enabled through the following settings on the solder point, and the insertion of RDT
resistance on the adjstustement zone. +TACH "pin 9" corrisponds to power supply’s negative GND
input.
Connect the negative of tachometer to pin 10. Do not exceed voltage as input from tacho value of
50V. Example: If you use a 10V/KRPM no more than 5000rpm
If the motor rotates in an opposite direction to the expected one,switch off and reverse the motor
and tachogenerator connections.
View the connections and settings from tachogenerator in chapter 4.2
Summary of Contents for MDCA 100
Page 1: ...1 MDCA XXX XX Precision Servodrive for DC motors...
Page 2: ...2...
Page 4: ...4 MDCA XXX XX...
Page 36: ...36 V 1 0...