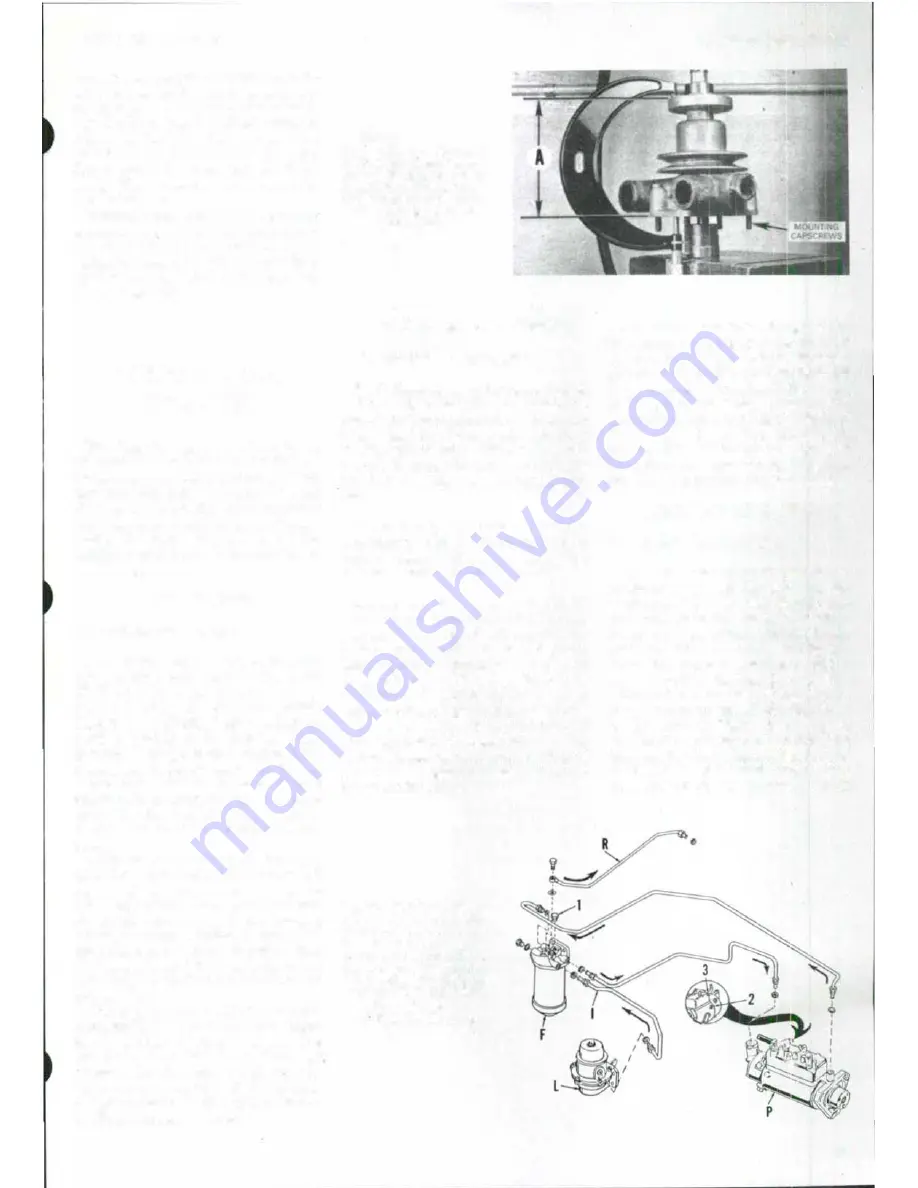
SERVICE MANUAL
mm
(0.010-0.020
inch). Support rear end
of shaft (not the impeller), place pump
mounting cap screws into holes in hous
ing, then press pulley hub onto shaft as
shown in Fig.
84.
Distance
(A)
from
gasket surface to fan surface of pulley
flange should
be
140.5
mm
(5.530
in·
ches). Make certain shaft assembly
rotates smoothly.
Reinstall water pump by reversing the
removal procedure. Adjust fan belt ten
sion to provide
13-19
mm
(1/2
to 3/4
inch)
deflection with
66
N
(15
pounds) force
applied midway between longest span
between pulleys.
DI ESEL FUEL
SYSTEM
The diesel fuel system consists of three
basic units; the fuel tank and filters, in·
jeetion pump and if\iector nozzles. When
servicing any unit associated with the
diesel fuel system, the maintenance of
absolute cleanliness is of utmost impor·
tance.
Of
equal importance is the
avoidance of nicks or burrs on any of the
working parts.
FUEL FILTERS
All Models So Equipped
85.
Models MF230, MF235 and
MF245
are equipped with a single fuel filter
{F-Fig. 85). 1\vo fuel filters, a primary
and secondary, are used on Models
MF240
and
MF250.
A
glass sediment
bowl is located at the bottom of the
primary or single filter element. Bowl
should be inspected and any dirt or
water accumulation drained daily. If
substantial amount of water or other
contamination is evident, source of con·
tamination should
be
found and cor·
rected.
Manufacturer recommends renewing
fuel filter element(s) after every
500
hours of operations or annually,
whichever comes first. Filter elements
should also be renewed if loss of engine
power or uneven running is noticeable
regardless of hours of operation. Note
that cleanliness of fuel supply has more
effect
on the life offuel filters than hours
of operation.
Thoroughly clean fuel filter and sur·
rounding area prior to removal. Close
fuel tank shut-off valve. Remove center
cap screw from fuel filter head and
remove filter element. Install new ele·
ment using new gaskets. Open fuel shut·
off valve and bleed air from system as
outlined in paragraph
86.
Fig. 84-DisllJnce
(A)
should
be 140.5
mm
(5.530
Inches).
Be
1ure
to
support end of
shaft (not the
Impeller) and In
s tell mounting cep
screw•
before
pressing pulley hub
onto
shaft.
BLEEDING FUEL SYSTEM
All Models So Equipped
86.
'lb
bleed air from fuel system, first
make sw-e fuel shut-off valve is open and
move injection pump shut-ofT control to
"Run" position. Loosen air vent plug
(1-Fig.
85)
in
top of filter head, then
operate
lift
pump priming lever until air·
free fuel flows from vent. Tighten vent
plug.
NOTE:
It may be necessary to rotate
crankshaft to
change
position of camshaft
lobe In relation
to
lift pump actuating arm
to allow operation of priming lever.
Loosen vent plug on secondary filter
(if
so
equipped) and repeat bleeding pro
cedure. Open vent plugs
(2
and
3)
on in·
jection pump and operate lift pump
priming lever. Tighten lower plug then
upper plug as air-free fuel flows from
each vent. Note that air in governor
housing relieved by bleed screw
(3)
will
not prevent engine from starting and
running properly; however, condensation
in the trapped air can cause rusting of
governor components and eventual
pump malfunction.
Fig.
85-Schematlc
view of
typlcel dleul fuel system
showing
direction
of fuel
flow
In fuel
1/nes,
filter
(F}, lift
pump
(L) and Infection
pump
(P).
Line
(R) retums exceas
fuel
to tank.
Two
flltera ,,.
used on
MF240 end MF250.
I.
Filt.er bleed plut
2
Pump bleed plug
S. Governor
hou.ling
bleed
plug
Paragraphs
85·87
Loosen Thermostart fuel supply line
(tractors
so
equipped) at intake manifold
and operate lift pump priming lever un
til fuel flows from the line. Retighten fuel
line connection. If engine fails to start
at this point, loosen high pressure fuel
line connections at injectors. With hand
throltle in full speed position, crank
engine with starter motor until fuel
flows from the connections. Retighten
fuel line connections and start engine.
THERMOSTART SYSTEM
All Models So Equipped
87.
The Thermostart system is
available as an aid for
cold
weather
starting on late production
MF250
trac·
tors. The system consi.std of an electrical
ly actuated heater located in the int..ake
manifold. The unit heats and ignites
diesel fuel vapor in intake manifold to
warm the air going into the cylinders.
The system is actuated by turning the
starter switch to "Heat" position for
15
to
20
seconds, then turn key to
"Heat/Start" position and crank engine.
After engine struts, key can be returned
to "Heat" position until engine runs
smoothly or for a maximum
of
15
37