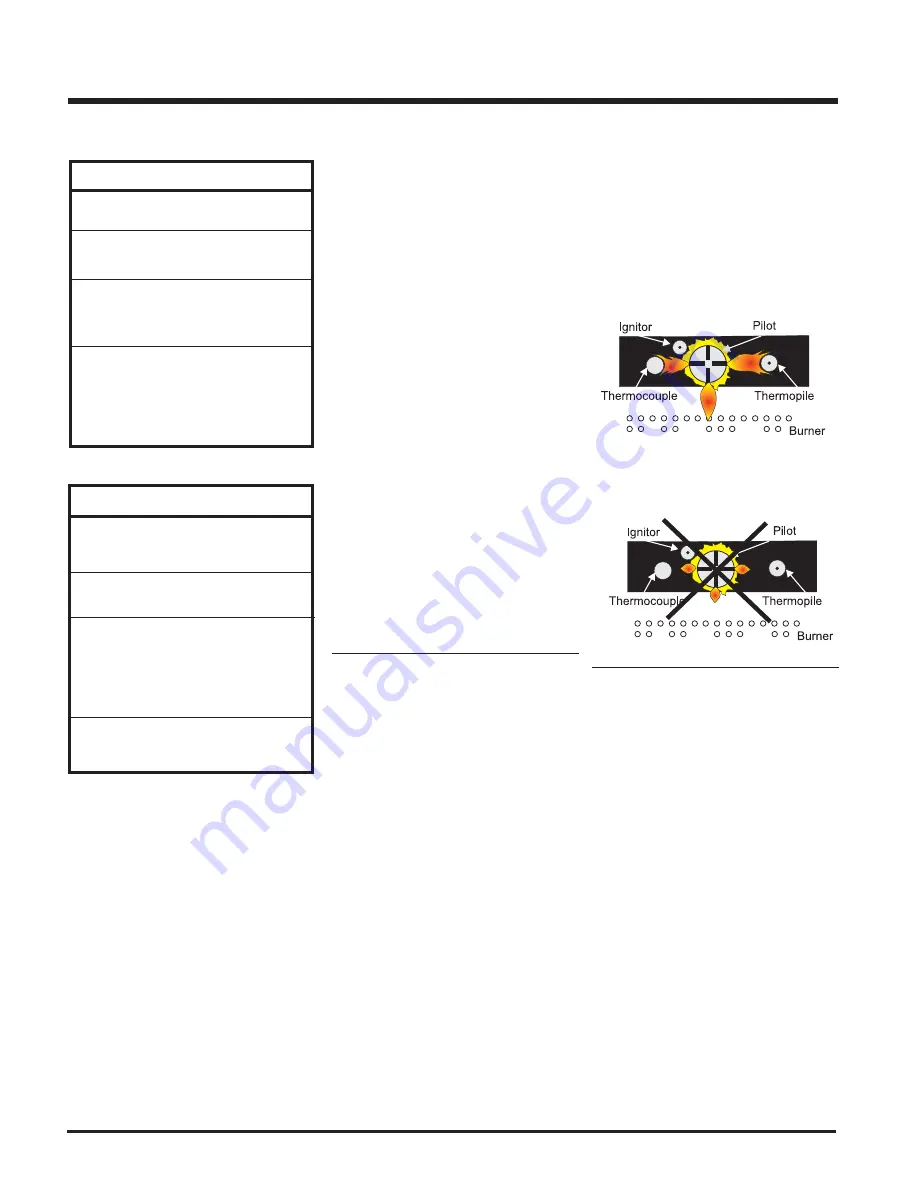
Masport P36-3 Gas Inbuilt
18
INSTALLATION
PRESSURE TESTING
The manifold pressure is controlled by a regu-
lator built into the gas control, and should be
checked at the pressure test point.
Note: To properly check gas pressure,
both inlet and manifold pressures
should be checked using the valve
pressure ports on the valve.
1) Make sure the valve is in the "OFF" position.
2) Loosen the "IN" and/or "OUT" pressure
tap(s), turning counterclockwise with a
1/8" wide flat screwdriver.
3) Attach manometer to "IN" and/or "OUT"
pressure tap(s) using a 5/16" ID hose.
4) Light the pilot and turn the valve to "ON"
position.
5) The pressure check should be carried out
with the unit burning and the setting should
be within the limits specified on the safety
label.
P36-NG3 System Data
For 0 to 4500 feet altitude
Burner Inlet Orifice Sizes: #37( 2.65mm)
Max. Input Rating 33 mj
Min. Input Rating
20 mj
Supply Pressure
min.1.25 kPa
Manifold Pressure
(High)
0.9 kPa
Electrical: 240 V A.C. System.
Circulation Fan: variable speed 130 CFM.
Log Set: Ceramic fibre, 7 per set.
Flue System:
Masport Direct Flue System (Flex)
P36-LPG3 System Data
For 0 to 2000 feet altitude
Burner Inlet Orifice Sizes: #52 (1.6 mm)
Max. Input Rating 31 mj
Min. Input Rating
18 mj
For 0 to 4500 feet Altitude:
Supply Pressure
min 2.75 kPa
Manifold Pressure
(High)
2.7 kPa
Electrical: 240 V A.C. System.
Circulation Fan: variable speed 130 CFM.
Log Set: Ceramic fibre, 7 per set.
PILOT ADJUSTMENT
Periodically check the pilot flames. Cor-
rect flame pattern has three strong blue
flames: 1 flowing around the thermopile,
1 around the thermocouple and 1 flowing
across the burner (it does not have to be
touching the burner).
Note: If you have an incorrect flame pat-
tern, contact your Masport dealer
for further instructions.
Incorrect flame pattern will have small,
probably yellow flames, not coming into
proper contact with the rear burner or
thermopile or thermocouple.
AERATION
ADJUSTMENT
The air shutter can be adjusted. Open the air
shutter for a blue flame or close for a yellower
flame. The burner aeration is factory set but may
need adjusting due to either the local gas supply
or altitude. This adjustment is performed by the
gas fitter.
Minimum Air Shutter Opening:
8 mm
NG
Full Open LPG
CAUTION: Carbon will be produced if air
shutter is closed too much.
Note: Any damage due to carboning re-
sulting from improperly setting the
aeration controls is NOT covered
under warranty.
Closed - Tall yellow
Open - Short Blue
GAS LINE
INSTALLATION
The gas line can be brought through either the
right or the left side of the appliance. The gas
valve is situated on the right hand side of the
unit and the gas inlet is on the right hand side
of the valve.
Note: If the gas line is being installed
from the left side, be sure to leave
room to accommodate servicing
of the fan.
The gas line connection may be made of rigid
pipe, copper pipe or an approved flex connec-
tor. (If you are using rigid pipe, ensure that the
valve can be removed for servicing.) Since
some municipalities have additional local codes
it is always best to consult with your local
authorities and the AG 601 or NZS 5261 instal-
lation code.
When using copper or flex connectors use
only approved fittings. Always provide a union
so that gas lines can be easily disconnected for
servicing. Flare nuts for copper lines and flex
connectors are usually considered to meet this
requirement.
Important: Always check for gas leaks
with a soap and water solution or gas
leak detector. Do not use open flame for
leak testing.
SYSTEM DATA