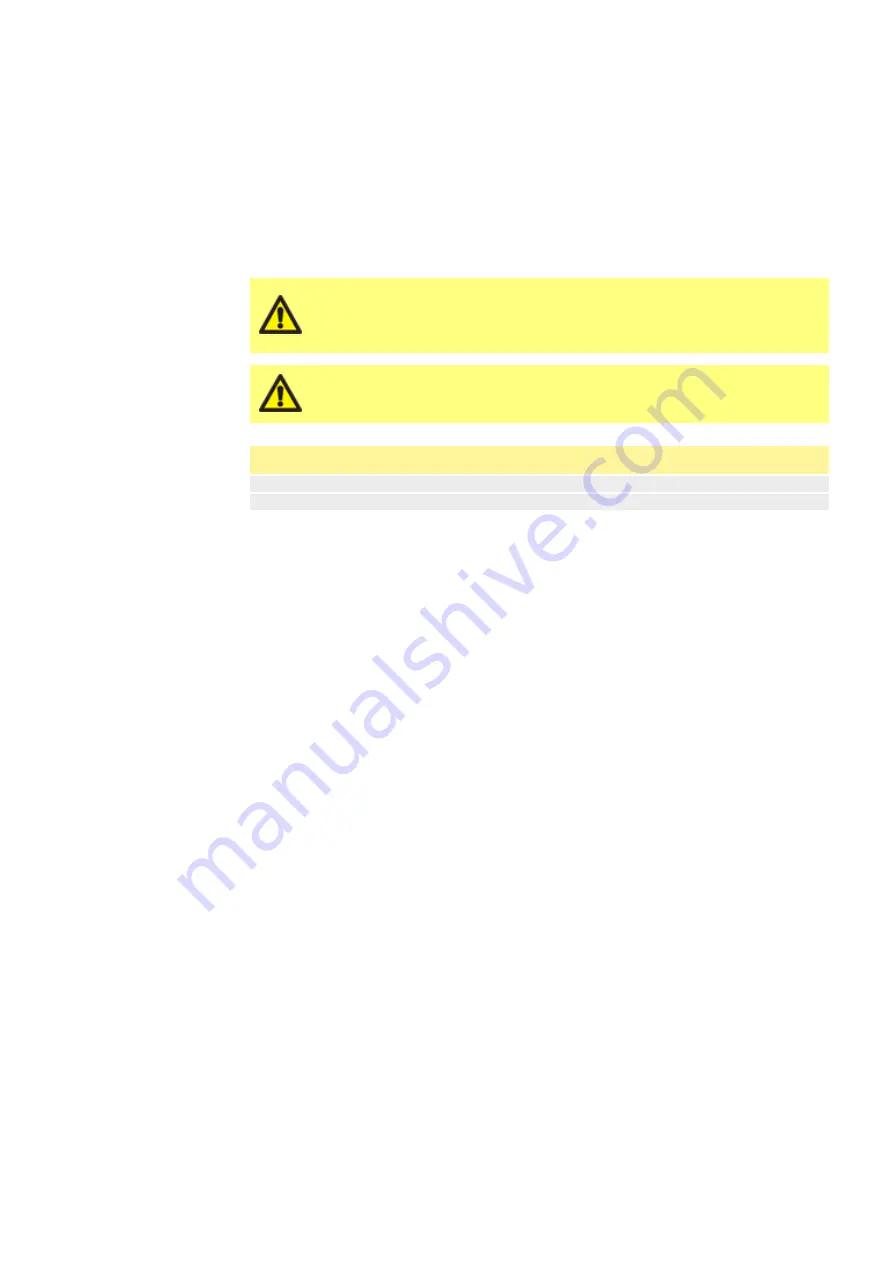
Steam-in place (SIP) for MasoSine products
Steam sterilisation kills micro-organisms through the application of moist heat (saturated steam) under
pressure, without disassembling the pump.
The heat from steam- in- place (SIP) cleaning processes damages a living cell's essential structures,
including the cytoplasmic membrane, rendering the cell no longer viable.
l
The pressure should be high enough to ensure that the steam reaches all parts of the pump through
the existing clearances.
l
The pump needs to be at standstill during SIP sterilisation. In exceptional cases the pump can run at
very low speed.
Avoid thermal shocks!
Thermal shocks have to be avoided as they might lead to an uneven thermal
expansion of the pump components. Uneven expansion caused by a sudden
temperature change can lead to pick up marks of the pump components.
After SIP sterilisation, ensure that a suitable acclimatisation period is maintained
before the pump is put back into operation
Class II SIP and CIP
procedure
Recommended temperature
Recommended pressure
differential
CIP
80-90C / 176-194F
2 bar (29 psi)
SIP
120C / 248F
—
Key CIP and SIP safety information
l
A distance of one metre around the pump should be kept clear during SIP to minimise danger in case
of leakage.
l
CIP and SIP processes should be monitored continuously.
l
If a leak occurs during CIP or SIP, the pumphead should not be touched until system pressure has
been relieved and the pumphead has been allowed to cool down.
Manual cleaning
For some products which are not soluble in water, or that contain fibres, a sufficient cleaning cannot
always be ensured by CIP. In this case a manual cleaning procedure is recommended.
Determine the pump cleaning schedule on-site for materials being processed and plant maintenance
schedule. Principally, MasoSine Certa series pumps do not require manual cleaning if CIP (clean-in-place)
is performed after operation.
To disassemble the pump head, see See Disassembling the pump on page 27. Inspect and replace worn
parts as necessary.
Note:
We recommend that you replace the front housing seal and locking screw seal when reassembling
the pump. If the area behind these seals becomes soiled, contact Watson- Marlow GmbH MasoSine
Division for a specific cleaning and sanitizing procedure validated to remove bacteria. If a chlorine
solution (150 ppm available chlorine) is used, it should leave no residual deposits which would remain in
the pump.
Also, acid cleaners have a much higher metal corrosion rate and pump parts should remain in acid
cleaning solutions no longer than necessary. Any strong inorganic mineral-based acids that are harmful
to your hands would be harmful to pump parts.
In applications where material can harden in the pump during shutdown, a CIP cleaning, flush or
disassembly of the pump head and manual cleaning is strongly recommended.
Aseptic processing system
If the equipment is installed in an aseptic processing system that is sterilized by heat and operated at a
temperature of 121C (250F) or higher, 3-A Standard 02-11 requires that the system monitors internal
pressure and shuts the system down automatically if the product pressure in the system drops below
atmospheric pressure. The system shall only be able to be restarted after it has been re-sterilized.
m-certa-en-08
23