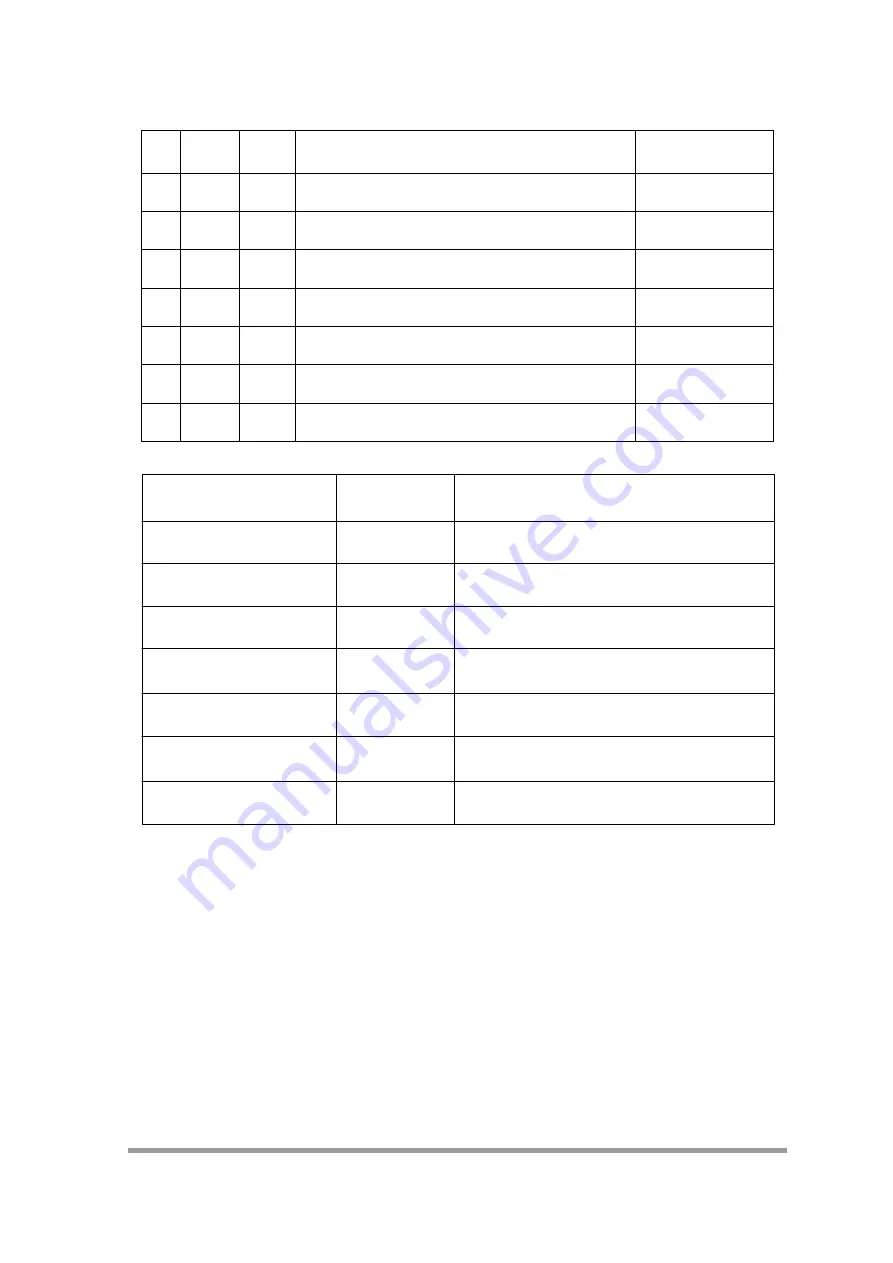
© Martin Engineering GmbH
33
M3504UK-10/15
Part numbers
Part number /
Teilenummer
Blade color /
Blattfarbe
Range of application /
Anwendungsbereich
35899-XXXXXXXX-XX+E
Orange
Used for 80% of all aplications /
Geeignet für 80% aller Anwendungen
35899-XXXXXXBR-XX+E
Brown / Braun
Used for chemical applications /
Anwendung mit Chemikalien
35899-XXXXXXCL-XX+E
Clear / Klar
Used for dry products /
Anwendung bei Trockenprodukten
35899-XXXXXXGR-XX+E
Green / Grün
Used for temperatures up to 150°C /
Anwendung bei Temperaturen bis zu 150°C
35899-XXXXXXNB-XX+E
Navy blue /
Marineblau
Used for sticky materials /
Anwendung bei klebrigen Produkten
35899-XXXXXXCR-XX+E
Yellow w/
Ceramic / Gelb
mit Keramik
Used for highly abrasive applications /
Hochabrasive Einsatzbedingungen
35899-XXXXXXYL-XX+E
Yellow / Gelb
Used for dry products /
Anwendung bei Trockenprodukten
ND
Item /
Pos.
Qty. /
Anz.
Description / Beschreibung
P/N / Teile-Nr.
1
1
XHD QC™ #1 blade / Abstreiferblatt
s.C. / s.T.
2
1
XHD QC™ #1 mainframe / Hauptachse
s.C. / s.T.
3
1
Slotted pin 20x80 mm / Spannstift
36046+E
4
1
Snap pin lock / Sicherungsklammer
36976
5
1
Tensioner / Spannvorrichtung
s.C. / s.T.
6
0,5 m
Cable Ø4mm / Kabel
40377
7
2
Cable clip / Kabelklemme
40378