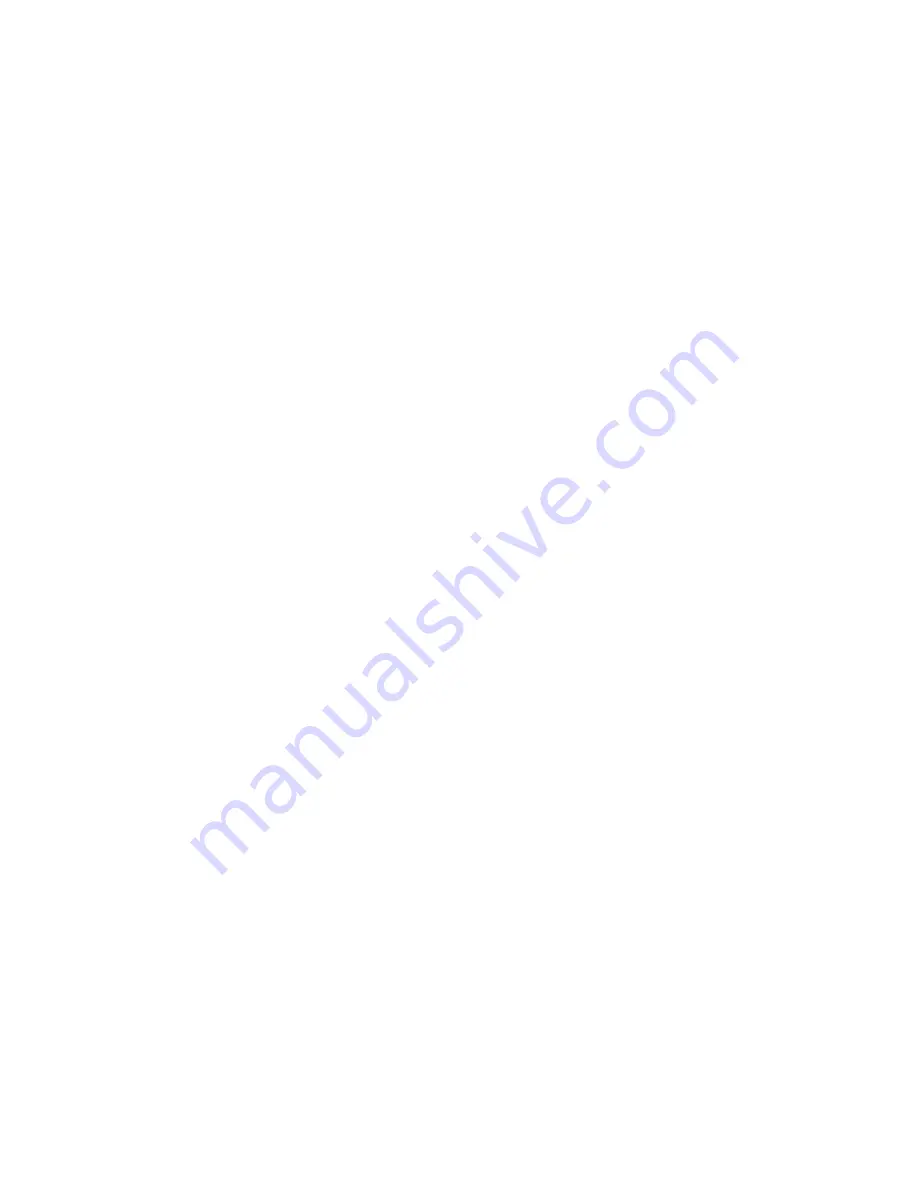
a high pressure drop. Remember, these tanks
can weigh up to 30 pounds when full of water; a
firm, level area is required.
3. R.O. Manifold Assembly
–
The manifold
can be installed on either the right or left side
of the under–sink area or a cabinet. The right
side is recommended because the tubing will
be to the back of the cabinet and out of the
way. Installation in the basement is also an
option, one location is near the laundry/utility
sink where cold potable water and drain
access is handy. The mounting location should
allow adequate clearance and accessibility for
cartridge changes.
4. Feed Water Connection
–
The Feed Water
Saddle Valve should be located as close to the
manifold assembly as possible. USE A
POTABLE COLD WATER SUPPLY ONLY.
Softened water is preferred as it will extend the
life of the R.O. Membrane.
5. Drain Connection
–
The waste water must
go to drain through an anti–siphon air gap. The
air gap is provided for in the base of the faucet.
If discharging into a utility sink or standpipe, an
air gap of greater than 1" above the flood rim
must be provided.
Do NOT connect the system drain line to the
dishwasher drain or near the garbage disposal.
Backpressure from these units may cause the
air gap to overflow.
SECTION IV.
INSTALLATION STEPS
All plumbing should be done in accordance with state
and local plumbing codes.
NOTE:
Some codes may require installation by a
licensed plumber; check with the local plumbing
authority prior to installation.
In restricted under–sink areas, it may be easier to
install the faucet first. Allow adequate tubing lengths for
any final component position.
A. Faucet Installation–
The faucet contains an
anti–siphon air gap. While the system is producing
water, the drain water flows from the R.O., through
the air gap and then to the household drain. The
purpose of the air gap is to prevent water in the
drain from backing up into the R.O. Drinking Water
System.
NOTE:
For proper installation the Air Gap Faucet
has a critical level line “CL” marked on its body
and should be mounted so that the “CL” line is at
least one (1) inch (26mm) above the flood rim of
the sink.
The easiest installation is to use an existing spray
attachment hole. If the spray faucet hole is not
available, then the sink top must be drilled.
Choose a convenient location as described in
Sec. III, C.1, page 4.
1. Mark the location of the center of the faucet
base.
2a. Drilling a stainless steel sink:
•Center punch the hole to provide a starting
point for the drill.
•Start with a smaller drill as a pilot, and then
drill a " diameter hole to accept the bolt of a
1 " Greenlee Hole Punch (1 " chassis
punch).
•Clean away any chips.
•Install the punch and tighten the nut to cut the
hole.
•Deburr any sharp edges.
2b. Drilling a porcelain sink:
It is best to use a special 1 " diameter cutter
designed for porcelain. A carbide tipped
masonry bit is a second choice.
•Place a piece of tape over the area to be
drilled to help prevent chipping.
•Drill a pilot hole for the porcelain cutter. Use
the pilot drill supplied with the kit or a carbide
tipped drill.
•When drilling the 1 " hole, drill slowly and
carefully; the porcelain chips easily.
•After drilling, clean the area well. Iron filings, if
left in place, can cause rust stains.
2c. Drilling a counter top:
NOTE:
The counter top must be less than 1 "
thick. (See Sec. IV, A.2b, page 5.) Treat
ceramic tile as porcelain until the tile is pene-
trated, then use the carbide tipped metal cut-
ter.
Formica counter tops may be drilled with a
good 1 " wood bit, drilling a 3/32" pilot hole will
help keep the bit going straight.