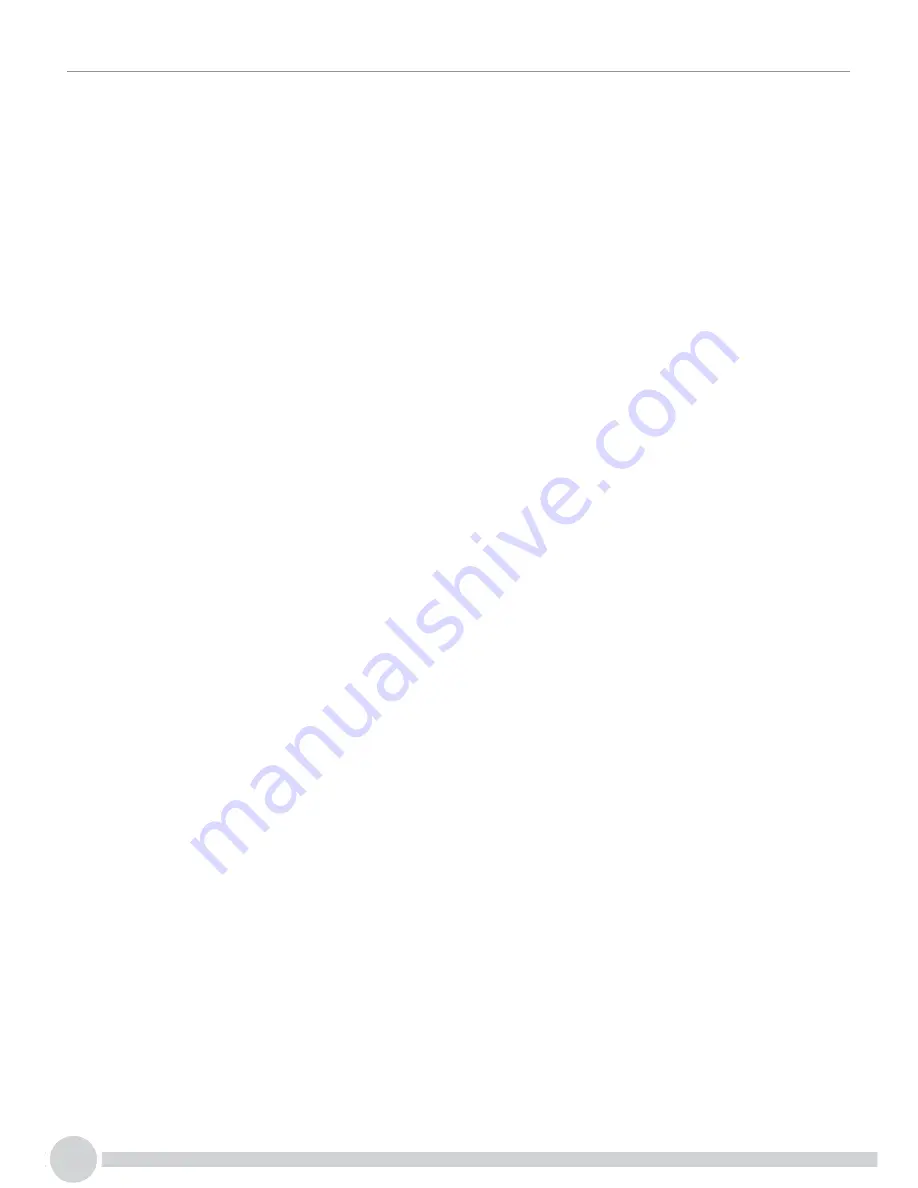
10
4.3 MAINTENANCE
Maintenance procedures (described below) are required for optimum equipment operation.
4.3.1 DAILY MAINTENANCE
1. Water faucet. Clean the faucet nozzle and remove any residue using warm water; do not use solvents or abrasive
detergents. If required, remove all the limestone with a food descaling solution.
2. Drip tray. Clean the tray and remove any residue using warm water.
3. CO2 pressure. Review pressure CO2 gauges for proper settings.
4. Power cord. Check condition of the power cord. Replace if necessary.
4.3.2 LIMESCALE
Descaling of the machine should ideally be carried out by qualified service personnel.
4.3.3 CHECK FOR CO2 PRESSURE:
Review pressure CO2 gauges for proper settings.
50 - 65 psi (350 - 450 Kpi) (3-4.5 bar)
Replacing a carbon dioxide (CO2) cylinder.
the cyclinder must be replaced when the needle of the reducer high pressure gauge is in the red segment.
1.Record the pressure values set on the pressure reducer, then fully close the bottle with the valve.
2.Remove the pressure reducer or disconnect the high pressure hose from the bottle if fitted. Check the condition of the
gaskets between the reducer and the bottle, replace them if necessary.
3.Replace the CO2 cylinder by slowly opening the valve to the fully open position and check that the pressure values are as
originally set.
4.3.4 CLEANING THE CHILLER CONDENSER:
Check the chiller condenser at monthly intervals and in accordance to the environmental conditions (humidity and dust). If
dust or dirt occurs between the condenser blades: remove screws, plastic clips and the removable upper panel then clean the
condenser fins using a soft brush, a vacuum cleaner or a low-pressure compressed air. Remove any dust from the cooling
and electrical components.
•
Accumulation of dust and grease over the condenser may cause overheating which could damage the compressor
beyond repair. The condenser must always be cleaned when necessary.
•
Do not use wire brushes or compressed air jets as they can damage the condenser.