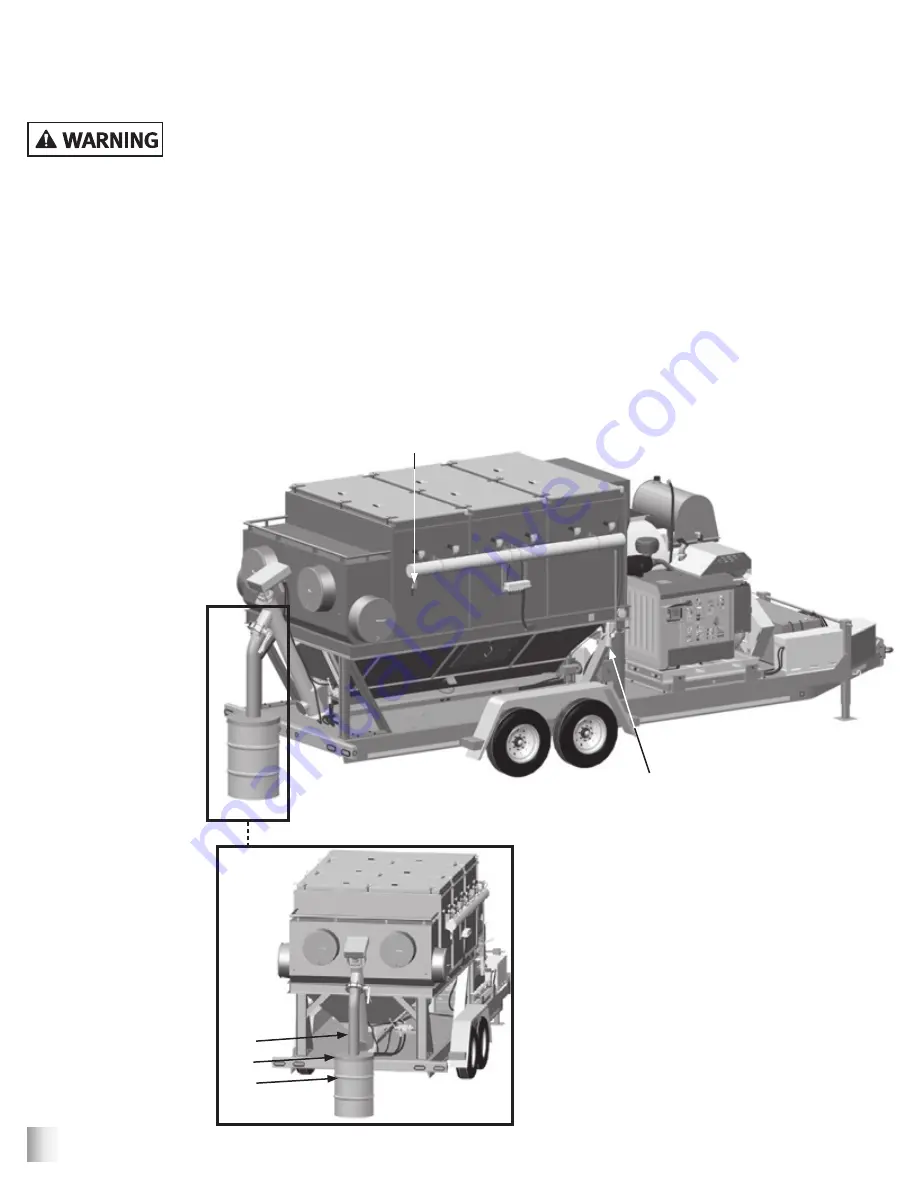
Dustmaster
®
28,000 CFM Tier 4 Diesel Dust Collectors
11
After use:
1) Decrease engine speed to idle (approximately 1000 RPM).
2) Disengage clutch with engine at idle.
3) Allow the pulser system to continue cleaning filters, with augers running. Operate at
least 60 minutes to allow filters to clean with the fan turned off.
4) Disconnect Discharge Hose (3) from optional Drum Cover (4), if equipped. Remove
Drum (5), if equipped.
5) Turn off compressed air supply.
6) Turn pulsers off by turning the two-position Selector Switch (2) "OFF" after header has
depressurized.
7) Turn the Auger Clean-out System “OFF” by returning the Hydraulic Control Valve
Lever (3) on the control valve to center position.
8) Shut engine down.
9) Open Pulser System Ball Valve (1).
10) Disconnect duct hose from Air Inlet(s).
11) Close Air Inlet(s).
OPERATING INSTRUCTIONS
Inspect all equipment for
wear or damage before
and after each use.
Failure to use Original
Equipment Manufacturer
repair parts and failure
to immediately replace
worn or damaged
components could void
warranties and cause
malfunctions. Failure to
comply with the above
warning could result in
death or serious injury.
W-505
1
4
5
2
3