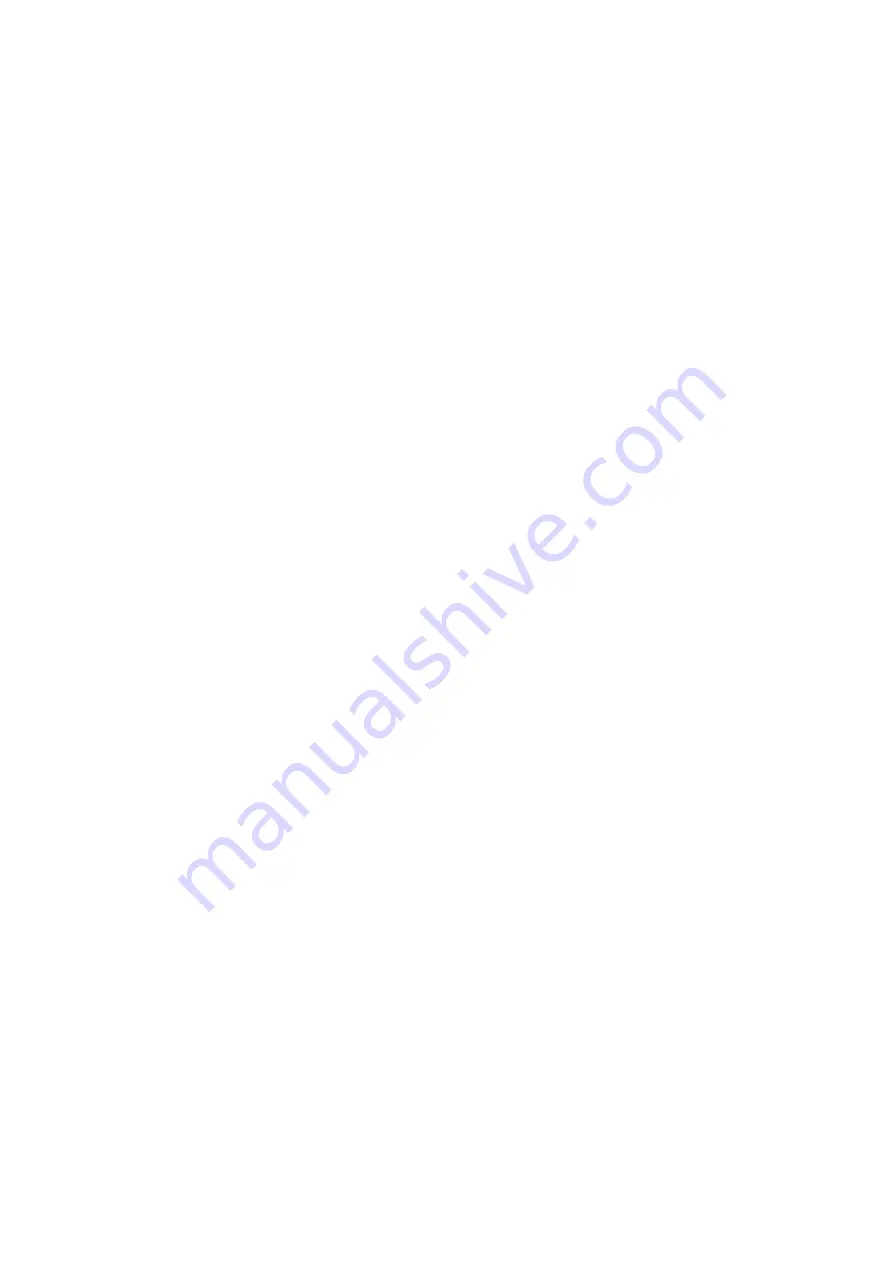
Sheet no. RP 840/5.1.211.1.2 issue 11.08.2021
MANKENBERG GmbH | Spenglerstr
aße 99 | D-23556 Lübeck
www
.mankenber
g.de T
el. +49 (0) 451 -8 79 75 0
Installation
The pilot-operated pressure reducing valves are supplied completely piped with the throttle valves D1 and D2 as well as with a dirt trap in the sense line.
The supply limits can be seen in the drawing.
Thoroughly flush the piping prior to installation of the valve in order to avoid that dirt particles get into the valves. If foreign matter and dirt particles cannot be
prevented during operation, the system must be protected with a dirt trap. The factory-supplied dirt trap at the inlet side of the sense line only protects the internal
control system and is not sufficient for permanently contaminated fluid. Remove packing material incl. the plastic plugs and mount the valve without strain. The
arrows on the valve bodies must point to the flow direction. In principle, the valves are to be mounted with the spring caps facing downward. The installation site
should be a horizontal section of pipe without any flow disruptions. Elbows, shut-off devices or other throttle points close to the valve, either upstream or down-
stream, have to be avoided.
The following connections must necessarily be provided by the customer:
A1:
Connection of the main valve inlet to the inert gas supply
A2-A5:
Sense line from the inert gas supply to the dirt trap of the sense line
A3-A4:
Sense line from the inert gas supply to the upper sense line connection at the main valve
A6-A9:
Sense line from the sense line connection of the pilot valve to the vessel / tank
A7-A8:
Connection from the pilot valve outlet to the vessel / tank
Do not use flexible connections for the sense lines.
Safety Instructions
Pressure control valves are no shut-off elements ensuring a tight closing of the valve. In accordance with DIN EN 60534-4 and/or ANSI FCI
70-2 they may feature a leakage rate in closed position in compliance with leakage classes II – V. Therefore, according to the German
Accident Prevention Act VGB 17, a safety device must be provided that prevents the admissible pressure within the system from being
exceeded. Unless indicated otherwise, the pressure control valve itself must be protected in such a way that the max. set pressure will not
be exceeded by more than 1.5 times.
Commissioning
The function and tightness of the differential pressure control valve that forms part of the pressure reducing valve RP840 as well as of the
pilot valve have been tested in the factory. The valves have been supplied with released spring. In this delivery condition, the main valve
(differential pressure control valve) is fully closed and opens immediately at minimum differential pressure. The pilot valve (pressure reducing
valve) is open and closes immediately at minimum outlet pressure.
For commissioning, open the valve at the inlet side slowly while making sure that the fluid is discharged on the outlet side. Pressure surges
have to be avoided. Then adjust the system at continuous flow as follows:
1. Main valve: Adjust it to the required inlet pressure towards the inert system by tightening the adjusting screw.
Turning the adjusting screw in clockwise direction (when looking onto the adjusting screw) increases the inlet pressure towards the
inert system.
2. Throttle D1 (influences the response behaviour of the entire control unit). Basic setting: open by 1 to 2 turns. In the delivery state, the
throttle D1 is open by 1.5 turns. By tightening the throttle, the control unit reacts more slowly. In so doing, possible vibrations can be
dampened.
Unscrewing the throttle makes the control unit react faster. The risk of vibrations will then be growing.
3. Throttle D2 (influences the response behaviour of the main valve). Basic setting:
open by approx. 3 turns. In the delivery state, the throttle D2 is open by 3 turns.
By tightening the throttle, the main valve reacts more slowly. In so doing, possible vibrations can be dampened.
Unscrewing the throttle makes the main valve react faster. The risk of vibrations will then be growing.
4. Pilot valve:
Setting to the required outlet pressure of the vessel / tank by tightening the adjusting screw.
Turning the adjusting screw in clockwise direction (when looking onto the adjusting screw) increases the pressure within the vessel.
5. Fine adjustment of the system with the help of the throttles D1 and D2.
Summary of Contents for M XTRA RP 840
Page 16: ...2020 MANKENBERG GmbH...
Page 37: ...2020 MANKENBERG GmbH...