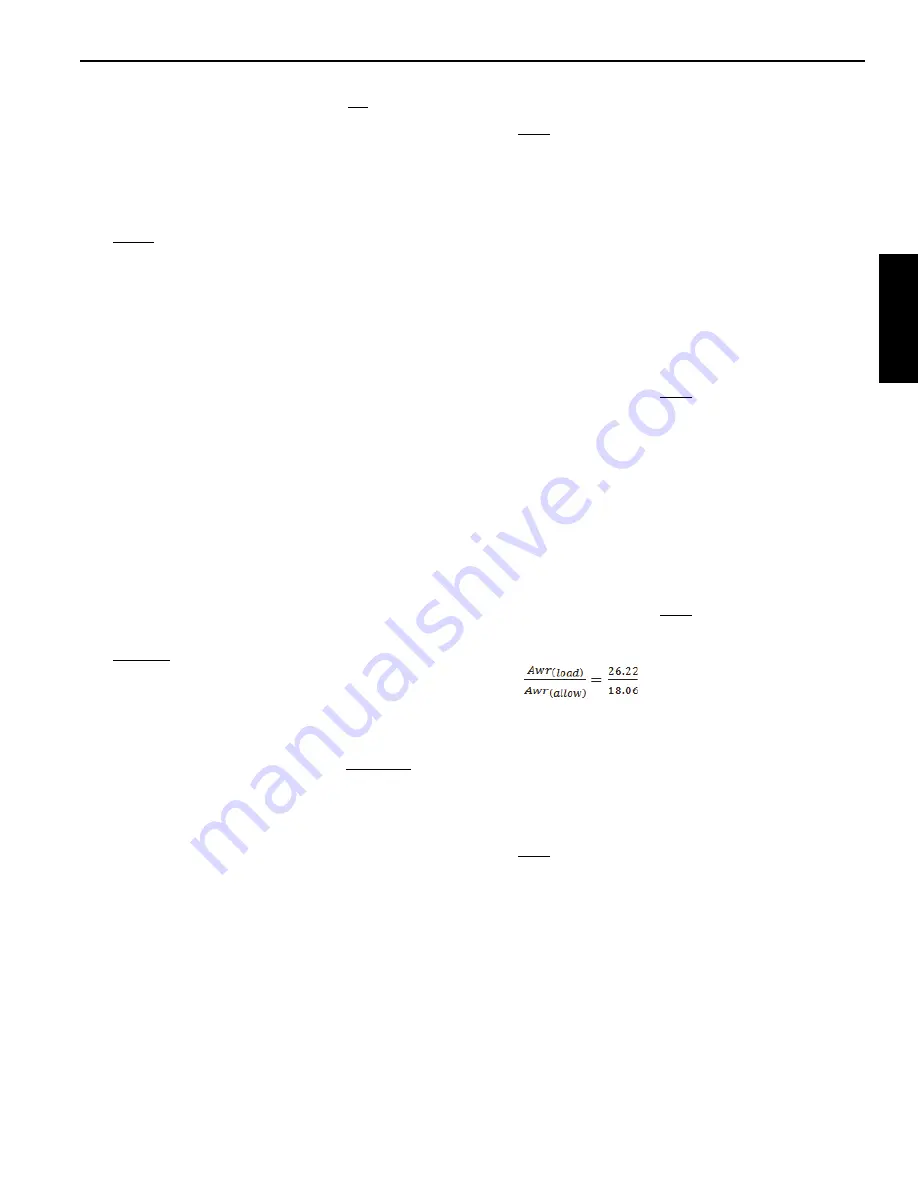
NATIONAL CRANE
Published 03-23-2018 Control # 243-14
2-15
NBT50 OPERATOR MANUAL
SAFETY PRECAUTIONS
2
At wind speeds greater than 13.4 m/s, it is not permissible to
lift a load greater than 12,040 kg, even if the wind resistance
area of the load is less than 14.45 m
2
.
Refer to the information from the above crane configuration,
examine several load conditions.
Load example 1.1:
With known Wind Drag Coefficient of the load
Cd
, and
•
load to be lifted of 11,200 kg,
•
Projected Wind Area
Ap
= 9.20 m
2
,
•
Wind Drag Coefficient
Cd
= 1.5
wind resistance area of load can be estimated as
Awr
(load)
=
Ap
x
Cd
= 9.2 x 1.5 = 13.8 m
2
Refer to the above
Lifting Limits at wind speed V(z)
> 13.4 m/s and
≤
to 20.1 m/s
. Comparing the load and wind
resistant area to the allowable:
•
Is the load to be lifted less than allowable load?
11,200 kg
≤
12,040 kg
YES
•
Is
Awr
(load)
less than
Awr
(allow)
?
13.8 m
2
≤
14.45 m
2
YES
Conclusion
: This load is permissible to lift in wind speed up
to 20.1 m/s.
Load example 1.2:
With unknown Wind Drag Coefficient of the load
Cd
,
•
Load to be lifted of 10,000 kg,
•
Projected Wind Area
Ap
=
5.45 m
2
,
•
Wind Drag Coefficient
Cd
= unknown
NOTE:
If exact Wind Drag Coefficient is not known, it shall
be assumed as 2.4.
•
the wind resistance area of load can be estimated as
Awr
(load)
=
Ap
x
Cd
=
5.45 x 2.4 = 13.08 m
2
Refer to the above
Lifting Limits at V(z) > 13.4
m/s
and
≤
20.1
m/s
. Comparing the load and wind resistant area
to the allowable:
•
Is the load to be lifted less than allowable load?
10,000 kg
≤
12,040 kg YES
•
Is
Awr
(load)
less than
Awr
(allow)
?
13.08
m
2
≤
14.45 m
2
YES
Conclusion
: This load is permissible to lift in wind speed up
to 20.1 m/s.
Load example 1.3a:
With large wind resistance area of the load
Awr
(load)
,
•
Load to be lifted of 14,000 kg,
•
Projected Wind Area
Ap
= 21.85 m
2
,
•
Wind Drag Coefficient
Cd
= 1.2
the wind resistance area of load can be estimated as:
Awr
(load)
=
Ap
X
Cd
=
21.85 x 1.2 = 26.22
m
2
R e f e r t o t h e a b o v e
L i f t i n g L i m i t s a t w i n d
speed V(z) > 13.4
m/s
and
≤
20.1
m/s
. Comparing the load
to the allowable:
•
Is the load to be lifted less than allowable load?
14,000 kg
≤
12,040 kg
NO
Conclusion
: This load is NOT permissible to lift in wind
speed up to 20.1 m/s.
R e f e r t o t h e a b o v e
L i f t i n g L i m i t s a t w i n d
speed V(z) < 3.4
m/s
. Comparing the load to the allowable:
•
Is the load to be lifted less than allowable load?
14,000 kg
≤
15,050 kg
YES
The maximum permissible wind speed for this load is
13.4 m/s, depending on the wind resistance area of the load.
•
Is
Awr
(load)
less than
Awr
(allow)
?
26.22 m
2
≤
18.06 m
2
NO
Conclusion
: This load is NOT permissible to lift in wind
speed at 13.4 m/s, but is permitted to lift at a reduced wind
speed calculated as follows:
Ratio
=
1.45
From Table 2-5, the maximum permissible wind speed at
ratio of 1.45 (rounded to next higher table value of 1.6) is
10.6 m/s.
Conclusion
: This load is permissible to lift in wind speed up
to 10.6 m/s only.
Load example 1.3b:
With large wind resistance area of the load
Awr
(load)
,
•
Load to be lifted of 8,000 kg,
•
Projected Wind Area
Ap
= 15.25 m
2
,
•
Wind Drag Coefficient
Cd
= 1.3
the wind resistance area of load can be estimated as
Awr
(load)
=
Ap
x
Cd
=
15.25 x 1.3 = 19.83 m
2
Refer to the above
Lifting Limits at wind speed V(z)
> 13.4
m/s
and
≤
20.1
m/s
. Comparing the load and wind
resistant area to the allowable:
Summary of Contents for National Crane NBT50 Series
Page 1: ...Operator Manual National Crane NBT50 Series ...
Page 2: ......
Page 10: ...TOC 6 TABLE OF CONTENTS OPERATOR MANUAL NBT50 THIS PAGE BLANK ...
Page 12: ...INTRODUCTION OPERATOR MANUAL NBT50 1 2 Published 03 23 2018 Control 243 14 FIGURE 1 1 7650 66 ...
Page 157: ......
Page 158: ......