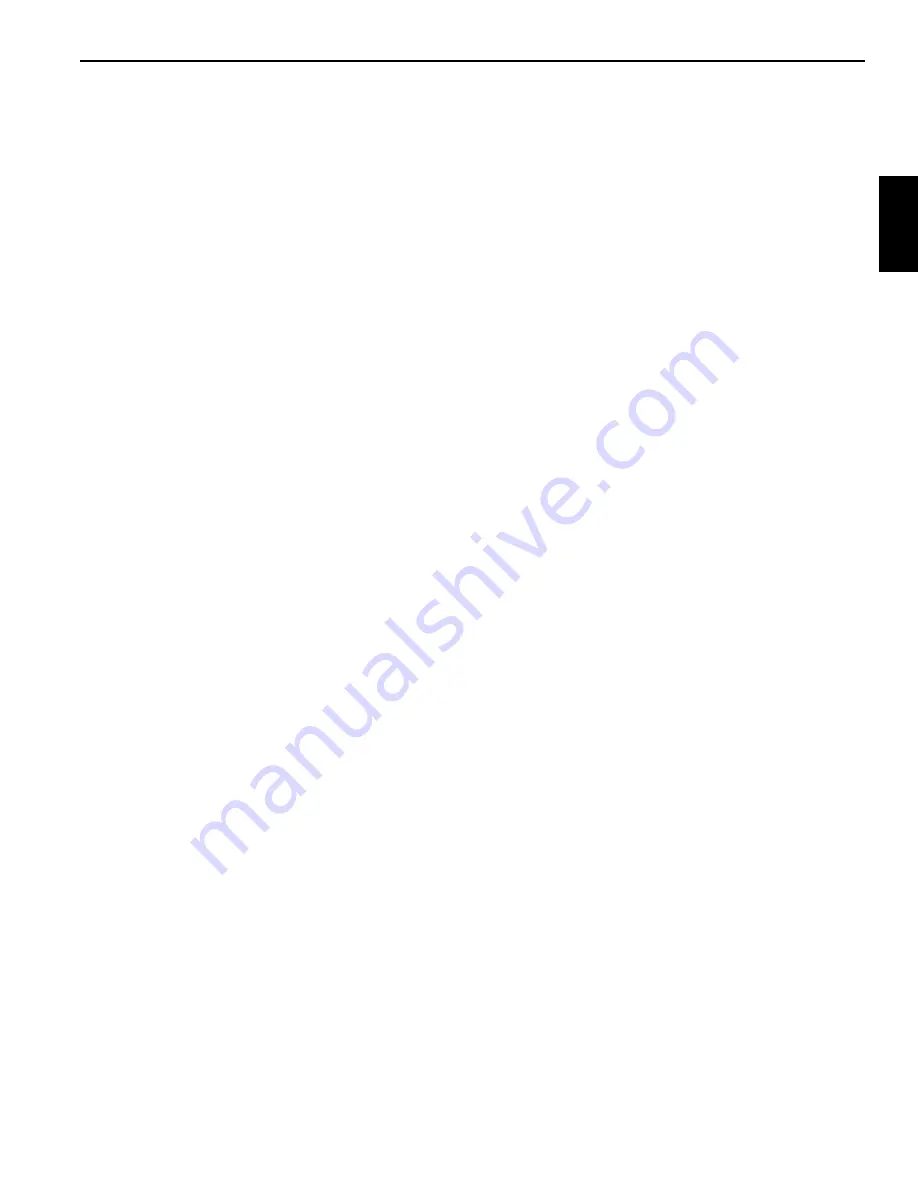
2-33
GROVE
RT770E
HYDRAULIC SYSTEM
2
Published 11/26/2014, Control # 447-05
DIRECTIONAL CONTROL VALVES
Description
The directional control valves direct and control hydraulic oil
flow from the pumps to function to be operated; lift and
telescope cylinder, each hoist, the swing motor, and the front
steering orbital motor.
Lift/Telescope/Hoist Directional Valve
The lift, telescope, and hoist(s) directional valves
Figure 2-18 located on the superstructure side plate are
three position normally closed valves. Hydraulic oil pressure
applied by the remote control valves through the pilot circuits
shift the directional control valves so they can drive their
respective cylinders and motors. RCL lockout valve(s) for
hoist up, lift down, and telescope out functions are located in
each directional control valve. These valves are in series in
the pilot lines between the remote control valve and the
directional control valve. When energized, they allow
operation of that function.
A load sense relief valve in the hoist/lift/telescope directional
control valve controls the main system pressure at 276 bar
(4000 psi). The unloading valve maintains a 20.7 bar
(300 psi) standby pressure and a constant 20.7 bar (300 psi)
pressure differential between the inlet and work port.
Swing/Steer Directional Valve
The swing/steer directional valve Figure 2-19 located on the
superstructure side plate is a three position normally open
valve. Hydraulic oil pressure applied by the remote control
valves through the pilot circuits shift the directional control
valves so they can drive their respective cylinders and
motors.
Counterweight Removal Directional Valve (Optional)
The counterweight removal directional valve Figure 2-20 is
installed on the rear of the turntable between the
accumulators.
The valve contains two five-way, three position closed center
directional valves. The inlet contains a load sense relief
valve set at 120.66 bar (1750 psi) which protects all four
working sections.
Maintenance
Swing/Steer Directional Valve Removal
1.
Tag and disconnect the hydraulic lines from the valves.
Cap or plug the lines and ports.
2.
Remove the capscrews, flatwashers and lockwashers
and bushings securing the valve. Remove the valve.
Swing/Steer Directional Valve Installation
1.
Install the valve on the turntable upright and secure with
the capscrews, flatwashers, lockwashers and bushings.
Torque capscrews; refer to
, page 1-16 for proper torque value.
2.
Connect the hydraulic lines to the valves as tagged
during removal.
Hoist/Lift/Telescope Directional Valve Removal
1.
Tag and disconnect the hydraulic lines from the valve.
Cap or plug the lines and ports.
2.
Tag and disconnect electrical connectors from the valve.
3.
Remove the capscrews, flatwashers, and lockwashers
securing the valve. Remove the valve.
Hoist/Lift/Telescope Directional Valve Installation
1.
Install the valve on the turntable upright and secure with
the capscrews, flatwashers, and lockwashers. Torque
capscrews; refer to
1-16 for proper torque value.
2.
Connect the electrical connectors to the valve as tagged
during removal.
3.
Connect the hydraulic lines to the valves as tagged
during removal.
Counterweight Removal Directional Valve Removal
1.
Tag and disconnect the hydraulic lines from the valve.
Cap or plug the lines and ports.
2.
Tag and disconnect electrical connectors from the valve.
3.
Remove the capscrews and nuts securing the valve.
Remove the valve.
Counterweight Removal Directional Valve Installation
1.
Install the valve to the turntable and secure with the
capscrews and nuts. Torque capscrews; refer to
, page 1-16 for proper
torque value.
2.
Connect the electrical connectors to the valve as tagged
during removal.
3.
Connect the hydraulic lines to the valves as tagged
during removal.
Functional Check (All Directional Valves)
1.
Start the engine and run it at normal speed.
2.
Operate the control levers of the valve bank(s). Check
for smooth operation of cylinders and motors.
3.
Check the valve bank(s) and lines for leakage. Make
repairs as needed.
Summary of Contents for Grove RT770E
Page 3: ...Service Maintenance Manual Grove RT770E ...
Page 4: ......
Page 40: ...INTRODUCTION RT770E SERVICE MANUAL 1 26 Published 11 26 2014 Control 447 05 THIS PAGE BLANK ...
Page 124: ...HYDRAULIC SYSTEM RT770E 2 84 Published 11 26 2014 Control 447 05 THIS PAGE BLANK ...
Page 149: ...4 5 Published 11 26 2014 Control 447 05 RT770E SERVICE MANUAL BOOM 4 GROVE FIGURE 4 2 ...
Page 150: ...BOOM RT770E SERVICE MANUAL 4 6 Published 11 26 2014 Control 447 05 FIGURE 4 2 continued ...
Page 152: ...BOOM RT770E SERVICE MANUAL 4 8 Published 11 26 2014 Control 447 05 FIGURE 4 2 continued ...
Page 154: ...BOOM RT770E SERVICE MANUAL 4 10 Published 11 26 2014 Control 447 05 FIGURE 4 2 continued ...
Page 224: ...5 24 Published 11 26 2014 Control 447 05 HOIST AND COUNTERWEIGHT RT770E This Page Blank ...
Page 276: ...POWER TRAIN RT770E 7 30 Published 11 26 2014 Control 447 05 THIS PAGE BLANK ...
Page 300: ...UNDERCARRIAGE RT770E 8 24 Published 11 26 2014 Control 447 05 FIGURE 8 28 ...
Page 348: ...LUBRICATION RT770E 9 36 Published 11 26 2014 Control 447 05 FIGURE 9 14 102 8130 2 ...
Page 356: ......
Page 357: ......