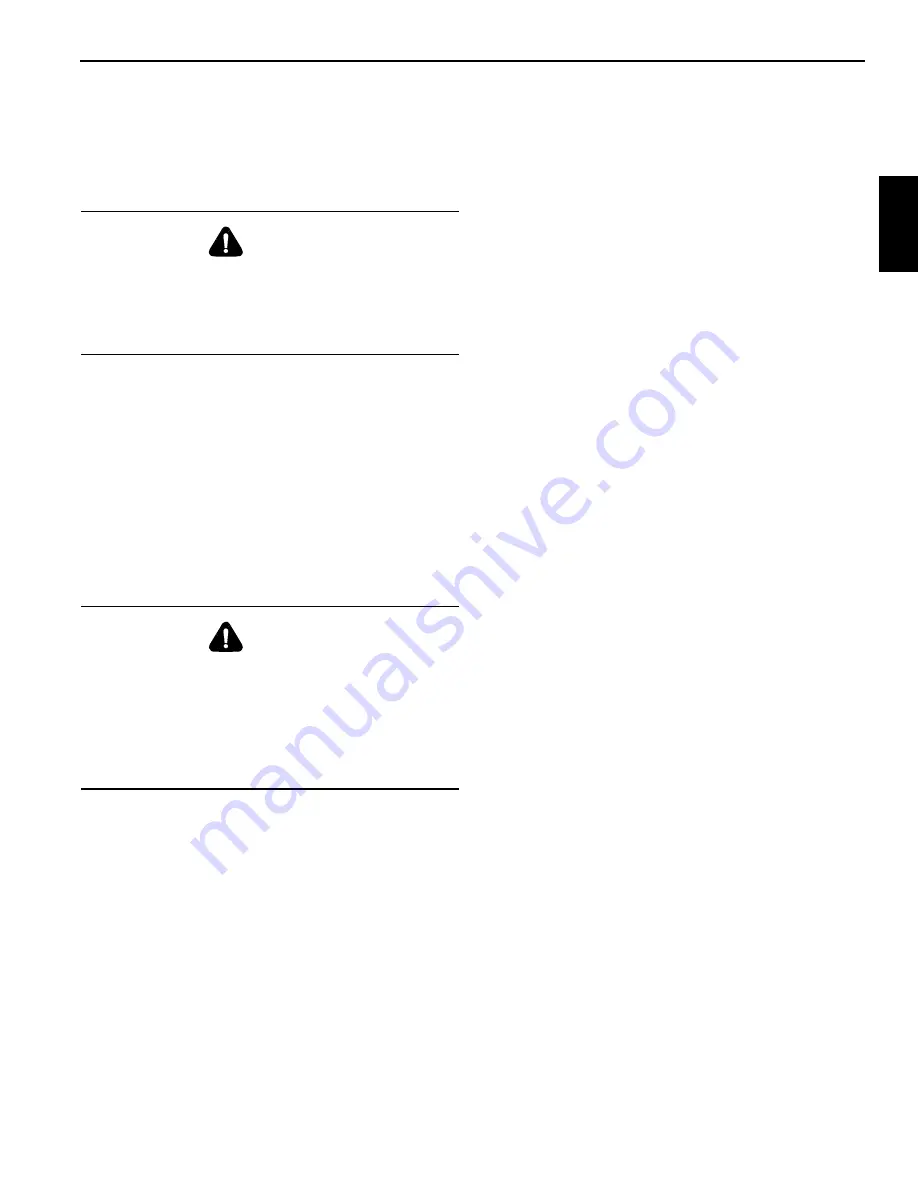
2-7
GROVE
RT770E
HYDRAULIC SYSTEM
2
Published 11/26/2014, Control # 447-05
Operate all hydraulic circuits several times in both
directions.
•
This action should return any entrapped air to the
reservoir where it can be removed from the hydraulic oil
by the baffles.
•
To remove entrapped air from telescope cylinders, lower
the boom to below horizontal and fully telescope the
boom in and out several times.
•
If the air is not readily removed, lower the boom to below
horizontal, extend the telescope cylinders as far as
practicable, and allow the boom to remain in this position
overnight. This should allow entrapped air to find its way
to the holding valve so that telescoping the boom IN the
next morning should force the air back to the reservoir.
Ensure the boom is first telescoped IN (not OUT) in the
morning. Telescoping OUT may cause air to be forced
back into the cylinder.
•
Entrapped air may be removed from cylinders having
wet rods by cycling. On certain cylinders, a plugged port
is provided on the rod end to bleed off entrapped air.
•
In the event that air entrapment should persist, bleeding
of air by loosening various clamp and screw type fittings
may become necessary.
•
If the above procedures fail to eliminate air entrapment,
contact your authorized Grove distributor.
Parts Replacement
Parts found damaged or out of tolerance when maintenance
is being performed should be replaced. Refer to the Grove
Parts Catalog for proper replacement parts.
Directional Control Valves
The control valves that control the crane functions are
installed on the right side of the turntable.
Inspection
Inspect the control valves for visible damage, binding spools,
and evidence of leakage. If excessive internal leakage is
suspected during operation with a spool in its center position,
it is possible that the area between the spool and working
section bore of the valve body is worn beyond serviceable
limits. If this condition exists, the spool and body must be
replaced as an assembly.
Valve Leakage
Dripping hydraulic oil indicates some type of external
leakage. The machine should be removed from service for
immediate repairs. External leaks sometimes develop at
fittings and seals. Spool seals are susceptible since they are
subject to wear. Seals may be damaged by temperatures
that are too high, or by dirt or paint accumulation on the
spool. Damaged or torn seals must be replaced.
A component functioning at reduced efficiency may indicate
that the control valve for that component is leaking internally.
If preliminary check-out reveals that adequate volume is
being supplied to the affected valve bank, relief valves are
properly adjusted, and the component is not at fault, check
the valve for scored or worn parts. Scoring is a sign of the
number one problem in hydraulics - contamination (external
contamination by dust or internal contamination by debris
from deteriorating components or oxidized hydraulic oil).
Scored or severely worn valve components must be
replaced.
Check valves in the control valves are designed to permit a
flow of hydraulic oil in one direction only. If a piece of dirt or
rust has worked its way into the check valve and lodges
between the poppet and seat, it will keep the valve open and
allow a return flow of hydraulic oil. The remedy is to clean the
valve, but it is also a good idea to follow through and ensure
the hydraulic system filter is still serviceable.
Binding Spools
Some of the most common causes for stiff spool movement
or jammed spool action are system overheating, excessive
pressure, contaminated or deteriorated hydraulic oil, or
warped mountings. When scorched, deteriorated hydraulic
oil or contamination is the cause, flushing the system and
replenishing with clean hydraulic oil may solve the problem.
If the spool bores are badly scored or galled, the valve must
be removed for servicing.
Warping occurs when mounting plates are not level or they
become distorted from machine damage. As mentioned
previously, the valve can be shimmed level.
CAUTION
Always locate the machine on a firm supporting surface,
extend the outriggers and level the machine and position
the boom over the front to extend the boom at low angles.
Injury or damage to the machine may result if this caution
is not followed.
CAUTION
Do not attempt to loosen fittings in pressurized lines or
while the hydraulic pumps are in operation.
Extreme care must be used when removing any plugs or
restrictions from a hydraulic system suspected to have
entrapped air that may be pressurized. Moderate to minor
injury mar result from pressurized air in a hydraulic
system.
Summary of Contents for Grove RT770E
Page 3: ...Service Maintenance Manual Grove RT770E ...
Page 4: ......
Page 40: ...INTRODUCTION RT770E SERVICE MANUAL 1 26 Published 11 26 2014 Control 447 05 THIS PAGE BLANK ...
Page 124: ...HYDRAULIC SYSTEM RT770E 2 84 Published 11 26 2014 Control 447 05 THIS PAGE BLANK ...
Page 149: ...4 5 Published 11 26 2014 Control 447 05 RT770E SERVICE MANUAL BOOM 4 GROVE FIGURE 4 2 ...
Page 150: ...BOOM RT770E SERVICE MANUAL 4 6 Published 11 26 2014 Control 447 05 FIGURE 4 2 continued ...
Page 152: ...BOOM RT770E SERVICE MANUAL 4 8 Published 11 26 2014 Control 447 05 FIGURE 4 2 continued ...
Page 154: ...BOOM RT770E SERVICE MANUAL 4 10 Published 11 26 2014 Control 447 05 FIGURE 4 2 continued ...
Page 224: ...5 24 Published 11 26 2014 Control 447 05 HOIST AND COUNTERWEIGHT RT770E This Page Blank ...
Page 276: ...POWER TRAIN RT770E 7 30 Published 11 26 2014 Control 447 05 THIS PAGE BLANK ...
Page 300: ...UNDERCARRIAGE RT770E 8 24 Published 11 26 2014 Control 447 05 FIGURE 8 28 ...
Page 348: ...LUBRICATION RT770E 9 36 Published 11 26 2014 Control 447 05 FIGURE 9 14 102 8130 2 ...
Page 356: ......
Page 357: ......