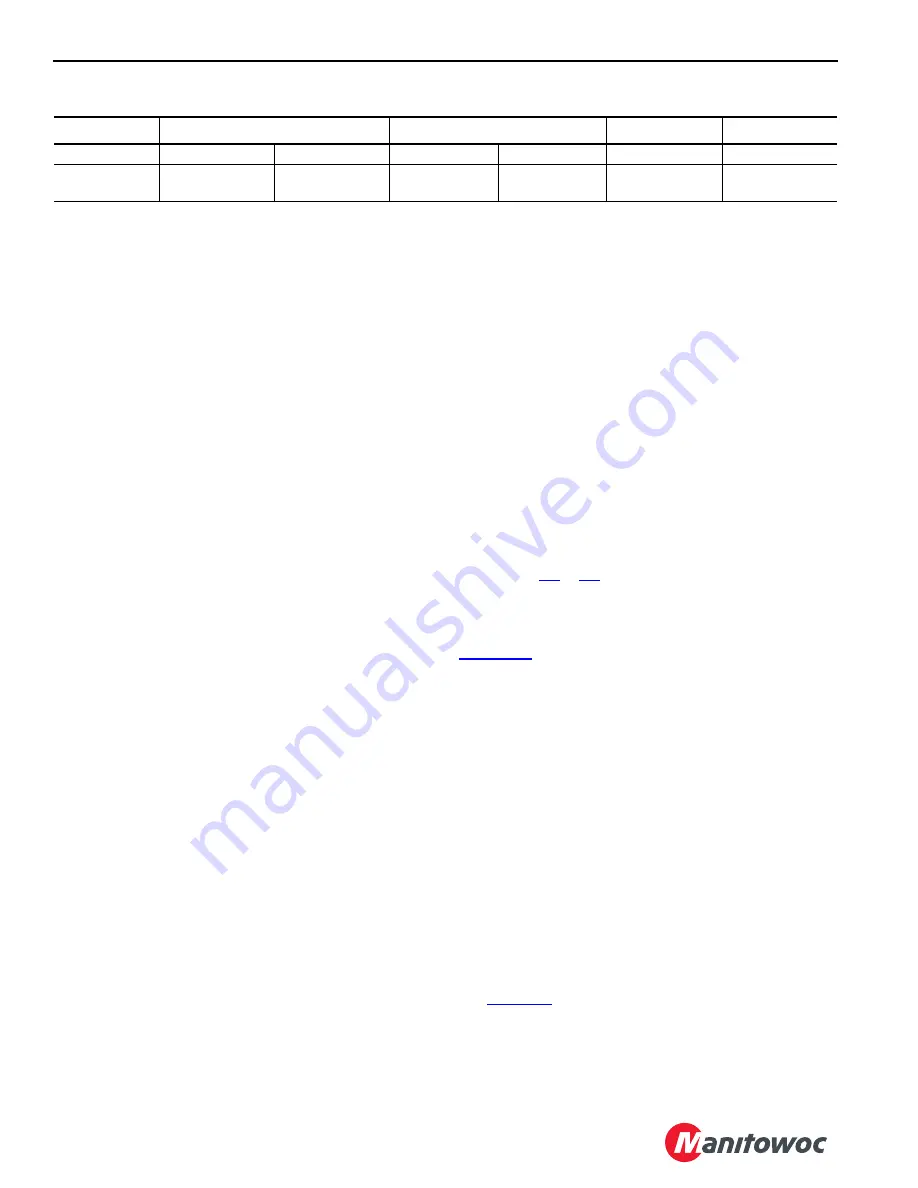
Reference
Only
INTRODUCTION
999 SERVICE/MAINTENANCE MANUAL
1-6
Published 05-16-17, Control # 233-03
Table 1-1 System Pressure Settings
Charge Pressure
Diagnostic screens contain system charge pressure
information. When a drum, swing or track system control
handle is in neutral, the system diagnostic screen provides
charge pressure information.
Charge pressure in each closed-loop system is preset at 350
psi (24 bar) with a relief valve in charge pump. Charge
pressure must be at preset value as lower pressures can
cause a slowing or stopping of operation.
If charge pressure drops in any system the brakes begin to
spring-apply. Brakes are fully spring-applied at 200 psi (14
bar) or more, depending on system. System pump does not
de-stroke when minimum charge pressure is reached,
except the accessory system (rear drum) pump. The
accessory pump de-strokes if the suction side pressure
drops below 160 psi (11 bar).
Hydraulic Motors
Variable displacement low torque/high speed, bent axis
piston motors are used in hydrostatic transmissions of the
travel, boom hoist, and load drum systems. Swing system
motor is a hydrostatic transmission, fixed displacement, low
torque/high speed, axial piston motor. Each variable
displacement motor contains a cylinder block, pistons,
output shaft, and external flushing valve. Boom hoist drum
and load drums have a PCP (Pressure Control Pilot) valve
that controls output speed/torque of the motor.
Motor cylinder block axis is tilted at an angle to output shaft
with pistons fitted axially around its axis. The internal end of
output shaft has a large flange face similar to pump
swashplate. Motor piston ends are retained to output flange
face and do not ride around the axis of rotating flange face
like the pump pistons.
Hydraulic fluid entering motor puts a force against pistons.
The retained piston ends put a thrust against output flange
with a rotational torque that turns output shaft. This also
rotates the cylinder block on bent axis, while tilt angle to
flange face reciprocates the pistons as they rotate. Hydraulic
fluid displaced by the pistons, returns to system pump
through non-pressure side of closed-loop system.
Main Pressure Monitoring
Diagnostics monitor each closed-loop system pressure.
Drum, swing, or track diagnostics screen displays the
monitored pressure information. System pressure value is
maintained at or greater than preset value, depending on
engine RPM. System pressure can also be checked at
pressure sender diagnostic gauge coupler with a 10,000 psi
(689 bar) high pressure gauge, when pump is stroked.
Accessory System Pressure
Diagnostics monitor the accessory system pressure. The
rear drum pump is the source of pressure for the accessory
system items. When an accessory valve is enabled, the PC
enables the rear drum pump to pressurize the low-pressure
side of rear drum system. Each solenoid valve of the
accessory system are open circuit type (return fluid is not
ported back to high-pressure side of pump). The PC
monitors the high-pressure side of the closed-loop. When
pressure on the high-pressure side of the closed-loop drops
off, the PC reduces the pump flow so the charge pumps can
keep up. To increase flow, a check valve is piped from the
charge pressure port on front drum pump to the high-
pressure side of rear drum closed-loop.
Basic Operation
See Figures
When a control handle is moved from neutral, the PC sends
a positive or negative output signal to system pump external
EDC. This current signal magnetizes armature (5,
) and starts to block orifice port (6) or (7),
depending on current polarity. Blockage of flow at exhaust
side of orifice port (6) in this example causes a pressure
difference across spool (8). This pressure difference
overcomes the resistance of spring (9) and moves the spool
proportionally to pressurize servo control cylinder (10).
The other servo control cylinder (11) fluid is routed to tank.
This tilts the swashplate (12), stroking the pump. As
swashplate tilts, chamber spring (13) is pulled in the opposite
direction of spool with linkage (14). This centers and
maintains spool in a neutral position until the 16 psi (1 bar)
chamber spring pressure is reached.
In travel pumps, the pressure relief and pressure-limiting
sections of multifunction valve responds when relief
pressure is reached. The pressure limiting function of travel
pumps is set not to exceed 6090 psi (420 bar). If travel pump
pressure exceeds preset pressure limit, pumps de-stroke to
prevent overheating of system fluid. Hydraulic fluid pressure
overcomes spring resistance in pressure limiting relief valve
(17,
), shifting spool to open a path for fluid. Servo
check valves (18) are spring loaded with an opening
pressure of 750 psi (52 bar).
SYSTEM
LOAD DRUMS
BOOM HOIST
SWING
TRAVEL
FUNCTION
Hoist (Port A)
Lower (Port B)
Up
Down
Left/Right
Fwd./Rev.
PRESSURE
psi (bar)
6,090
(420)
3,770
(260)
6,090
(420)
3,770
(260)
6,090
(420)
6,090
(420)
Summary of Contents for 999
Page 1: ...R e f e r e n c e O n l y Service Maintenance Manual Manitowoc 999 ...
Page 2: ...R e f e r e n c e O n l y ...
Page 4: ...R e f e r e n c e O n l y THE ORIGINAL LANGUAGE OF THIS PUBLICATION IS ENGLISH ...
Page 297: ...R e f e r e n c e O n l y ...
Page 298: ...R e f e r e n c e O n l y ...