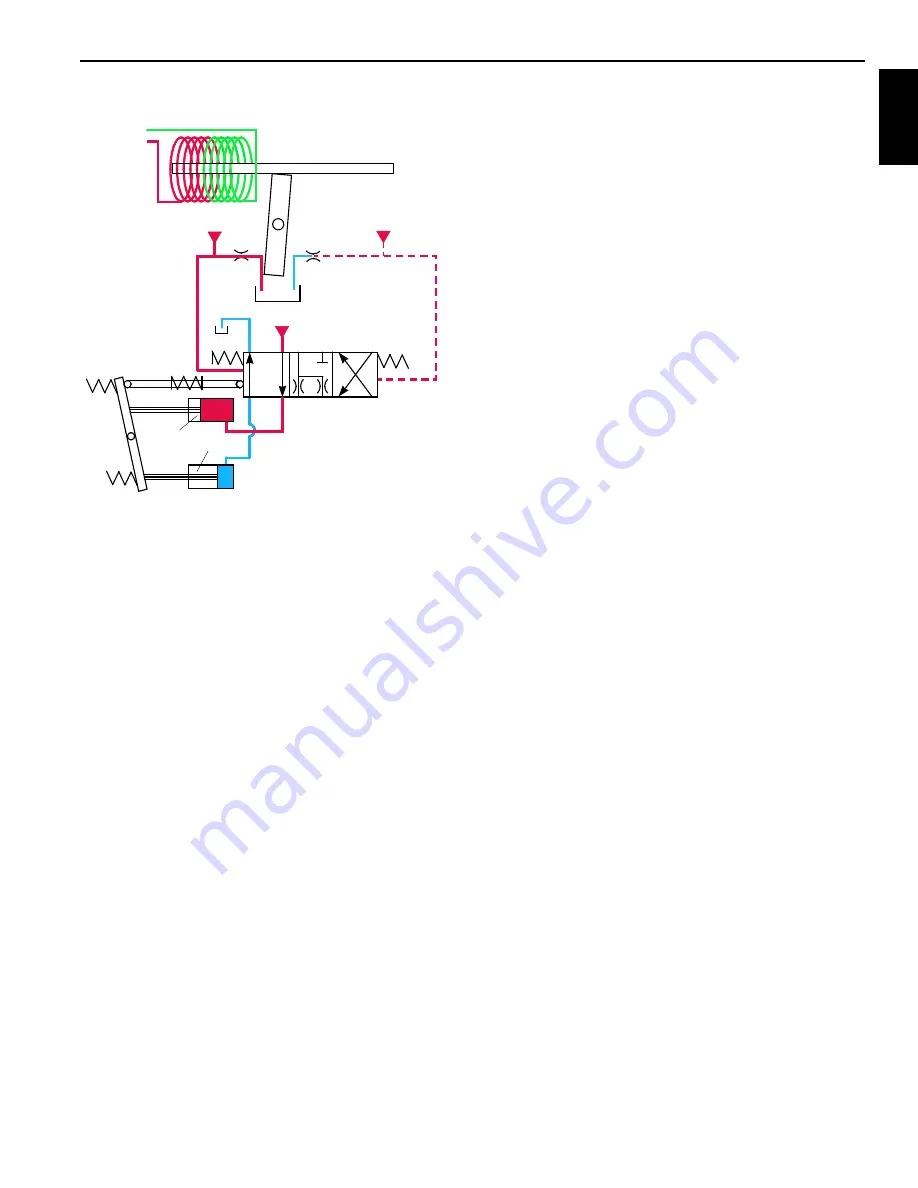
Reference
Only
Manitowoc
Published 05-16-17, Control # 233-03
1-7
999 SERVICE/MAINTENANCE MANUAL
INTRODUCTION
1
Exhaust hydraulic fluid from valve (17) flows through exhaust
port of displacement control valve (19). Exhaust port of
displacement control valve has a restricted orifice that
develops back-pressure for servo control cylinder (1) to
pressurize and de-stroke pump to limit system pressure.
When rapid loading produces pressure spikes, system relief
valve (16) shifts, allowing high pressure fluid to return to tank
through charge pump relief valve (3) or transfers fluid to low-
pressure side of closed-loop system through charge flow
make-up check valves (4).
In other system pumps, pressure limiting is controlled
through relief valve section of multifunction valves only. Flow
control orifice (20) is removed from pump EDC. Servo check
valves (18) are removed from pump and paths to servo
control cylinders are plugged. These changes permit pump
to react quicker to PC commands.
Also, pressure limiting valves (17) serve as pilot valves to
open system relief valves (16) when desired relief pressure
setting is reached. For example, if a pressure imbalance
occurs on both sides of flow restrictor (21), pressure limiting
valve opens and system relief valve relieves system
pressure. Hydraulic fluid is directed to tank through relief
valve (3) or the flow is transferred to low-pressure side of
system through make-up check valves (4).
NOTE:
Servo check valves (18) are only used in the travel
pump circuit. In other system pumps, these valves
are removed and the paths to the servo control
cylinders are plugged as shown with (X).
Pump displacement depends on engine driven pump speed
through pump drive and swashplate tilt angle. The engine
provides power for work, while the swashplate tilt angle
provides speed control. Engine speed is set and controlled
with hand or foot engine throttle.
Each variable displacement motor, except travel, begins
operation at maximum displacement (high torque, low
speed) and shifts to minimum displacement (low torque, high
speed) if torque requirement is low. The motor remains in
maximum displacement until servo PC valve (23) receives a
command from PCP valve (25) to direct system pressure
and flow from shuttle valve (22) to minimum displacement
side of servo cylinder (24) that shifts motor. As PCP valve
opens in proportion to the positive output signal received
from the PC, pilot line pressure is directed to shift servo PC
valve. After overcoming adjustable valve spring (26) and
valve spring (27), servo PC valve shifts and directs fluid to
stroke motor into minimum displacement output. If the load
at the motor shaft increases, force on adjustable valve spring
(26) increases. This shifts servo PC valve to de-stroke the
motor to maximum displacement for safe load handling.
The load drums and boom hoist motors also have a PCOR
(Pressure Compensating Over-Ride) valve (28) that is
enabled when system pressure of 4,930 psi (340 bar) is
reached (3770 psi [270 bar] for travel system). When system
pressure exceeds the PCOR setting, the valve shifts to direct
flow from shuttle valve (22) into maximum displacement side
of servo cylinder (24). The PCOR valve over-rides the
command from servo PC valve (23), increasing motor
displacement and output torque and reducing output speed.
When PCOR valve closes, control of the motor returns to
servo PC valve.
FIGURE 1-2
999CSM1-101
5
6
8
9
13
12
10
7
11
15
14
Control
Voltage
Pilot Pressure
Pilot Pressure
Pilot Pressure
Summary of Contents for 999
Page 1: ...R e f e r e n c e O n l y Service Maintenance Manual Manitowoc 999 ...
Page 2: ...R e f e r e n c e O n l y ...
Page 4: ...R e f e r e n c e O n l y THE ORIGINAL LANGUAGE OF THIS PUBLICATION IS ENGLISH ...
Page 297: ...R e f e r e n c e O n l y ...
Page 298: ...R e f e r e n c e O n l y ...