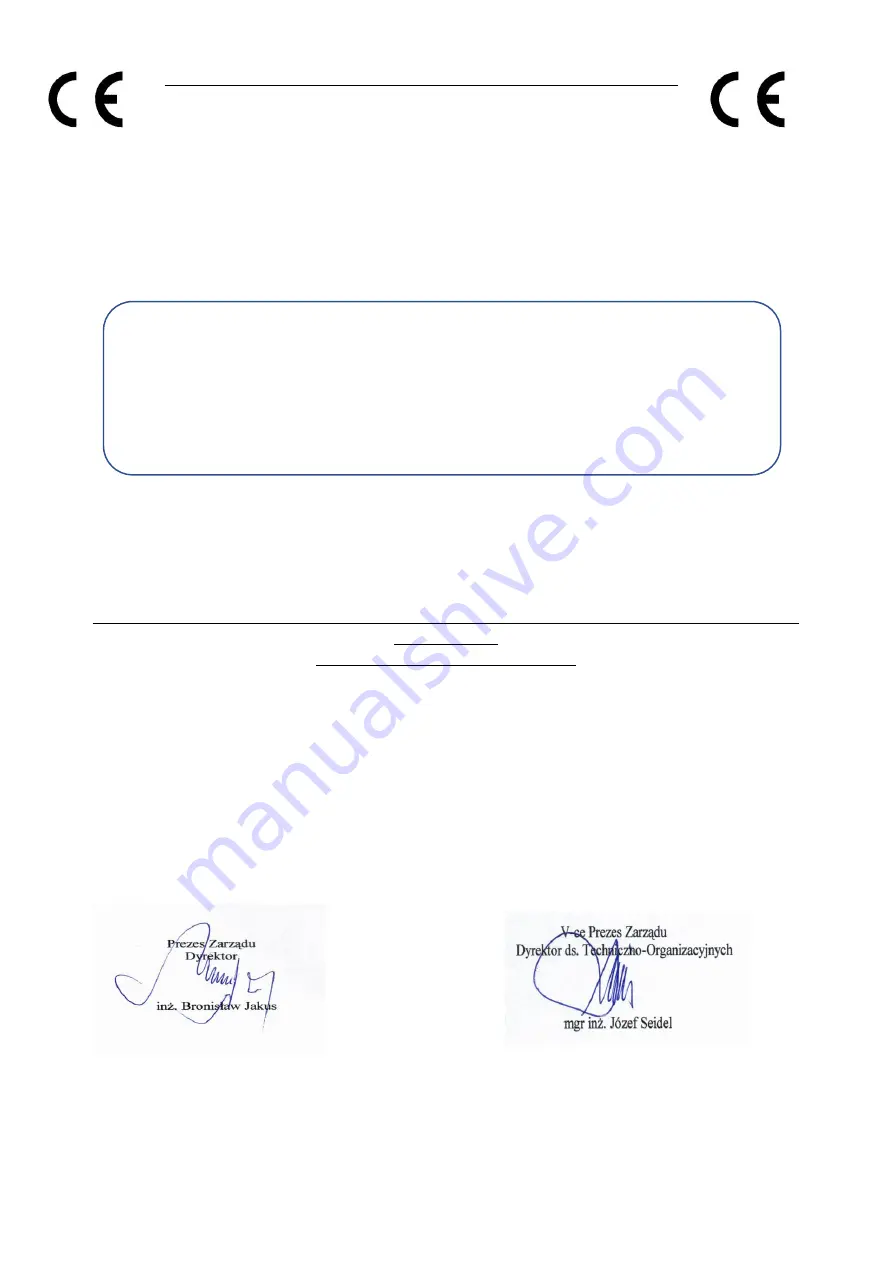
2
EC DECLARATION OF CONFORMITY
FOR THE MACHINE
Pursuant to the Ordinance of the Minister of Economy of 21 October 2008 (Journal of Laws No. 199, item 1228)
and the Directive of the European Union 2006/42/EC of 17 May 2006
MANDAM Sp. z o.o.
ul.
Toruńska 14
44 -100 Gliwice
declares with full responsibility that the machine:
under this declaration, complies with:
Ordinance
of the Ministry of Economy of October 21, 2008 on the essential
requirements for machines (Journal of Laws No. 199, item 1228)
and the Directive of the European Union 2006/42/EC of 17 May 2006
Persons responsible for the technical documentation of the machine: Jarosław Kudlek,
Łukasz Jakus
ul. Toruńska 14, 44
-100 Gliwice
The following standards were also used to assess compliance:
PN-EN ISO 13857:2010,
PN-EN ISO 4254-1:2016-02,
PN-EN ISO 12100-1:2005/A1:2012
PN-EN ISO 12100-2:2005/A1:2012
PN-EN 982+A1:2008
This EC Declaration of Conformity loses its validity, if the machine is modified or converted
without the manufacturer's consent.
Gliwice 27.06.2019
Place and date of issue
Surname, first name, position and
signature of the authorized person
SAL DISC HARROW
type/model
…………………………
.........................................
year of production:
...............................
Serial No.:
…………………
.