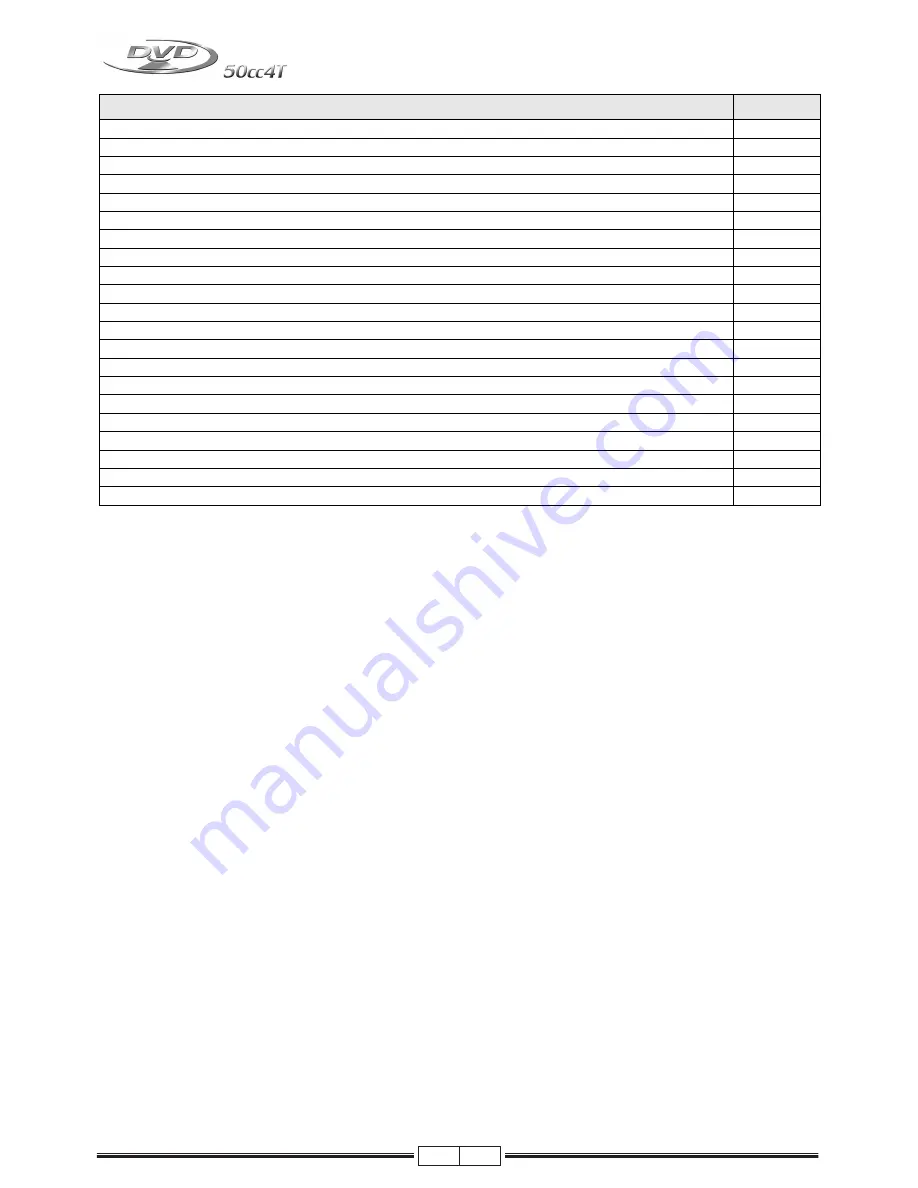
03/10
III
REPLACING CENTRIFUGAL ROLLERS
61
DISMANTLING THE CLUTCH ASSY
61
ASSEMBLING THE CLUTCH ASSY
62
DISMANTLING THE CARBURETTOR
62
DISMANTLING THE STARTER
62
DISMANTLING THE VALVE
63
DISMANTLING THE FLOAT, NEEDLE AND JET
64
REMOVE THE IDLE SCREW AND IDLING ADJUSTING SCREW
65
CYCLE TIGHTENING TORQUES
66
ENGINE TIGHTENING TORQUE
67
TIGHTENING TORQUE (GENERIC TABLE)
68
FRAME DIMENSION CHECKS
68
ELECTRICAL PART LOCATION
69
SWITCH CHECKS
71
CHECK FUEL LEVEL GAUGE
71
CHECK FUEL LEVEL SENSOR
72
IGNITION
72
HT COIL
72
SPARK PLUG CAP
72
STATOR (POWER 70W)
72
WIRING DIAGRAM
73
DESCRIPTION
PAGE