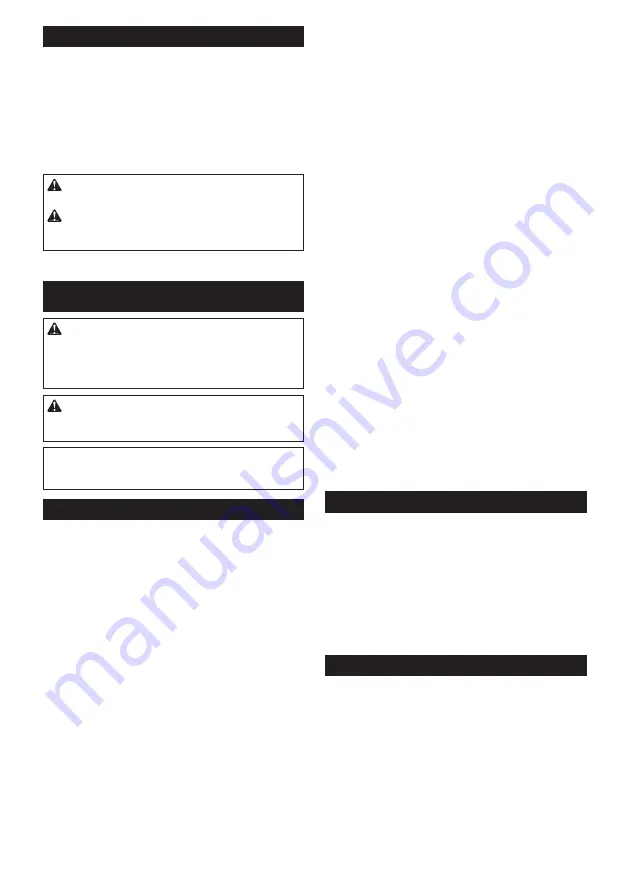
15 ENGLISH
Carrying tool
►
Fig.37:
1.
Stopper pin
Make sure that the tool is unplugged. Secure the blade
at 0° bevel angle and the turn base at left miter angle
fully. Lower the handle fully and lock it in the lowered
position by pushing in the stopper pin.
Carry the tool by carrying grip as shown in the figure. If
you remove the holders, dust bag, etc., you can carry
the tool more easily.
►
Fig.38
CAUTION:
Always secure all moving portions
before carrying the tool.
CAUTION:
Stopper pin is for carrying and
storage purposes only and not for any cutting
operations.
MAINTENANCE
WARNING:
Always be sure that the blade is
sharp and clean for the best and safest perfor-
mance.
Attempting a cut with a dull and /or dirty blade
may cause kickback and result in a serious personal
injury.
CAUTION:
Always be sure that the tool is
switched off and unplugged before attempting to
perform inspection or maintenance.
NOTICE:
Never use gasoline, benzine, thinner,
alcohol or the like. Discoloration, deformation or
cracks may result.
Adjusting the cutting angle
This tool is carefully adjusted and aligned at the factory,
but rough handling may have affected the alignment. If
your tool is not aligned properly, perform the following:
Miter angle
►
Fig.39:
1.
Hex bolt
Loosen the grip which secures the turn base. Turn the
turn base so that the pointer points to 0° on the miter
scale. Tighten the grip and loosen the hex bolts secur-
ing the guide fence using the wrench. If the pointer
does not point to 0° on the miter scale, loosen the screw
which secures the pointer and move and secure the
pointer plate so that the pointer points to 0° on the miter
scale.
Lower the handle fully and lock it in the lowered position
by pushing in the stopper pin. Square the side of the
blade with the face of the guide fence using a triangular
rule, try-square, etc. Then securely tighten the hex bolts
on the guide fence in the order from the right side.
►
Fig.40:
1.
Triangular rule
Bevel angle
0° bevel angle
►
Fig.41:
1.
0° bevel angle adjusting bolt
Lower the handle fully and lock it in the lowered position
by pushing in the stopper pin.
Loosen the knob at the rear of the tool.
Loosen the hex nut and turn the 0° bevel angle adjust
-
ing bolt on the right side of the turn base two or three
revolutions clockwise to tilt the blade to the right.
Carefully square the side of the blade with the top
surface of the turn base using the triangular rule, try-
square, etc. by turning the 0° bevel angle adjusting bolt
counterclockwise. Then tighten the hex nut to secure
the 0° bevel angle adjusting bolt and tighten the knob
securely.
Make sure that the pointer on the arm points to 0° on
the bevel scale. If it does not point to 0° on the bevel
scale, loosen the screw which secures the pointer and
move and secure the pointer plate so that the pointer
points to 0° on the bevel scale.
►
Fig.42:
1.
Triangular rule
2.
Saw blade
3.
Top sur-
face of turn base
►
Fig.43:
1.
Pointer
45° bevel angle
►
Fig.44:
1.
45° bevel angle adjusting bolt
2.
Pointer
Adjust the 45° bevel angle only after performing 0°
bevel angle adjustment.
To adjust left 45° bevel angle, loosen the knob and tilt
the blade to the left fully.
Make sure that the pointer on the arm points to 45° on
the bevel scale on the arm.
If the pointer does not point to 45°, turn the 45° bevel
angle adjusting bolt on the left side of the arm until the
pointer points to 45°.
Replacing carbon brushes
►
Fig.45
Remove and check the carbon brushes regularly.
Replace when they wear down to 3 mm in length. Keep
the carbon brushes clean and free to slip in the holders.
Both carbon brushes should be replaced at the same
time. Use only identical carbon brushes.
Use a screwdriver to remove the brush holder caps.
Take out the worn carbon brushes, insert the new ones
and secure the brush holder caps.
►
Fig.46:
1.
Brush holder cap
2.
Screwdriver
After use
After use, wipe off chips and dust adhering to the tool
with a cloth or the like. Keep the blade guard clean
according to the directions in the previously covered
section titled "Blade guard". Lubricate the sliding por-
tions with machine oil to prevent rust.
To maintain product SAFETY and RELIABILITY,
repairs, any other maintenance or adjustment should
be performed by Makita Authorized or Factory Service
Centers, always using Makita replacement parts.
Summary of Contents for MLS100
Page 2: ...2 Fig 1 1 Fig 2 1 Fig 3 1 2 3 Fig 4 1 Fig 5 1 Fig 6 1 Fig 7 1 Fig 8 ...
Page 3: ...3 1 Fig 9 1 Fig 10 2 1 3 130mm Fig 11 1 2 Fig 12 1 Fig 13 1 Fig 14 1 2 Fig 15 1 2 Fig 16 ...
Page 4: ...4 1 Fig 17 1 2 Fig 18 1 2 3 4 Fig 19 1 2 3 4 5 6 Fig 20 1 Fig 21 Fig 22 1 Fig 23 1 Fig 24 ...
Page 7: ...7 1 Fig 41 1 2 3 Fig 42 1 Fig 43 1 2 Fig 44 Fig 45 1 2 Fig 46 ...