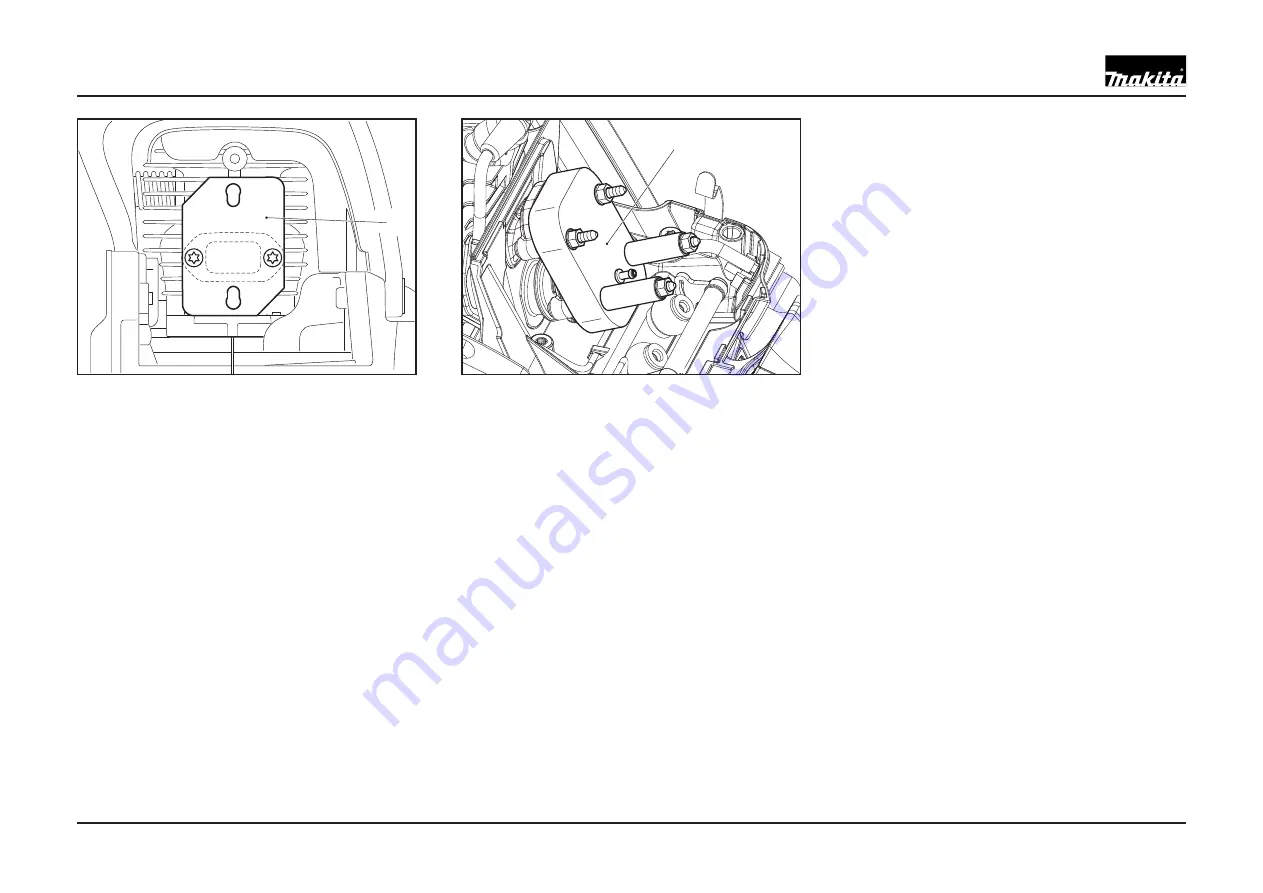
Repair Manual EA6100P / EA6101P
25
11 CYLINDER / PISTON
1
2
Drive, pressure test
If it is not possible to adjust the carburetor
properly, it will be necessary to check the
sealing of the Drive.
To seal the exhaust side, install sealing plate
1
(944.603.180) in the place of the muf
er
(rubber coating towards the cylinder).
To do this it will be necessary to remove the
muf
er, see chap. 04.
To seal the intake side, install sealing plate
2
(944.603.200) in the place of the carburetor
unit.
To do this it will be necessary to remove the
carburetor unit, see chap. 07 and 08.
Connect the over/underpressure pump
to the connection on the sealing plate
2
(944.603.200)
Move the piston to top dead centre.
Pull the pulse line from the cylinder connection
and seal the connection.
Set up a pressure of max. 0.5 bar.
If the pressure drops within 20 seconds, it can
have one of these causes:
• Radial ring leaking
• Cylinder base gasket leaking
• Crankcase gasket leaking
• Crack in crankcase
• Crack in cylinder
• Spark plug leaking
NOTE:
Detergent can be used to localise
leaks. If there is a leak into the oil tank, it
will not be possible to fully identify the leak.
If pressure remains steady in the crankcase
after shutting off the oil line hole, for example
with a rubber stopper (see chap. 05), it is
an indication that there is a defect in the
crankcase gasket to the oil tank.
Drive, vacuum test
Since the radial gasket ring can also fail
at negative pressure, a vacuum must be
established in the crankcase to test the radial
ring.
Seal off the intake and exhaust sides as
described above.
Connect the over/underpressure pump to the
connection on the sealing plate
2
.
Move the piston to top dead centre.
Pull the pulse line from the cylinder connection
and seal the connection.
Set up a negative pressure of max. 0.5 bar.
If the pressure does not rise to more than
0.3 bar within 20 seconds, the radial gasket
is OK. Otherwise the radial gaskets must be
replaced.
Remove the
ywheel and clutch, see
IGNITION SYSTEM
and
CLUTCH / CLUTCH
DRUM
.
On the clutch side, pull the circlip from the
shaft.
Guide the 15 mm radial gasket puller
(944.500.895) over the shaft and turn it
rmly
into the radial gasket. When the spindle is
screwed in, it will press against the shaft and
pull the radial gasket out.
Caution: Under no circumstances hammer
in the puller.