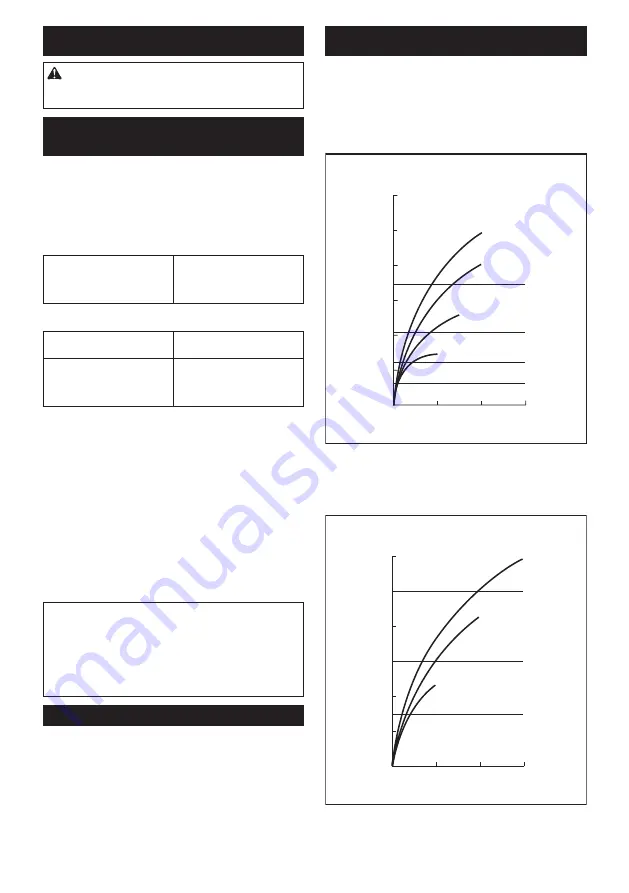
8 ENGLISH
ASSEMBLY
CAUTION:
Always be sure that the tool is
switched off and the battery cartridge is removed
before carrying out any work on the tool.
Installing or removing driver bit/
socket bit
Optional accessory
►
Fig.9
Use only driver bit/socket bit that has inserting portion
shown in the figure. Do not use any other driver bit/
socket bit.
For tool with shallow driver bit hole
A=12mm
B=9mm
Use only these type of driver
bit. Follow the procedure
1. (Note) Bit-piece is not
necessary.
For tool with deep driver bit hole
A=17mm
B=14mm
To install these types of driver
bits, follow the procedure 1.
A=12mm
B=9mm
To install these types of driver
bits, follow the procedure 2.
(Note) Bit-piece is necessary
for installing the bit.
1. To install the driver bit, pull the sleeve in the direc
-
tion of the arrow and insert the driver bit into the
sleeve as far as it will go.
Then release the sleeve to secure the driver bit.
►
Fig.10:
1.
Driver bit
2.
Sleeve
2. To install the driver bit, pull the sleeve in the direc
-
tion of the arrow and insert the bit-piece and driver
bit into the sleeve as far as it will go. The bit-piece
should be inserted into the sleeve with its pointed
end facing in. Then release the sleeve to secure
the driver bit.
►
Fig.11:
1.
Driver bit
2.
Bit-piece
3.
Sleeve
To remove the driver bit, pull the sleeve in the direction
of the arrow and pull the driver bit out.
NOTE:
If the driver bit is not inserted deep enough
into the sleeve, the sleeve will not return to its original
position and the driver bit will not be secured. In this
case, try re-inserting the bit according to the instruc-
tions above.
NOTE:
After inserting the driver bit, make sure that it
is firmly secured. If it comes out, do not use it.
Installing hook
►
Fig.12:
1.
Groove
2.
Hook
3.
Screw
The hook is convenient for temporarily hanging the tool.
This can be installed on either side of the tool. To install
the hook, insert it into a groove in the tool housing on
either side and then secure it with a screw. To remove,
loosen the screw and then take it out.
OPERATION
►
Fig.13
The proper fastening torque may differ depending upon
the kind or size of the screw/bolt, the material of the
workpiece to be fastened, etc. The relation between fas
-
tening torque and fastening time is shown in the figures.
Standard bolt
N•m
(kgf•cm)
2
1
2
1
3
0
100
(1020)
120
(1224)
80
(816)
60
(612)
40
(408)
20
(204)
M12
M14
M10
M12
M14
M10
M8
M8
3
1.
Fastening time (second)
2.
Fastening torque
3.
Proper fastening torque corresponding to each bolt
diameter
High tensile bolt
3
2
1
N•m
(kgf•cm)
2
1
0
80
(816)
60
(612)
40
(408)
20
(204)
3
100
(1020)
120
(1224)
M10
M12
M12
M8
M8
M10
1.
Fastening time (second)
2.
Fastening torque
3.
Proper fastening torque corresponding to each bolt
diameter