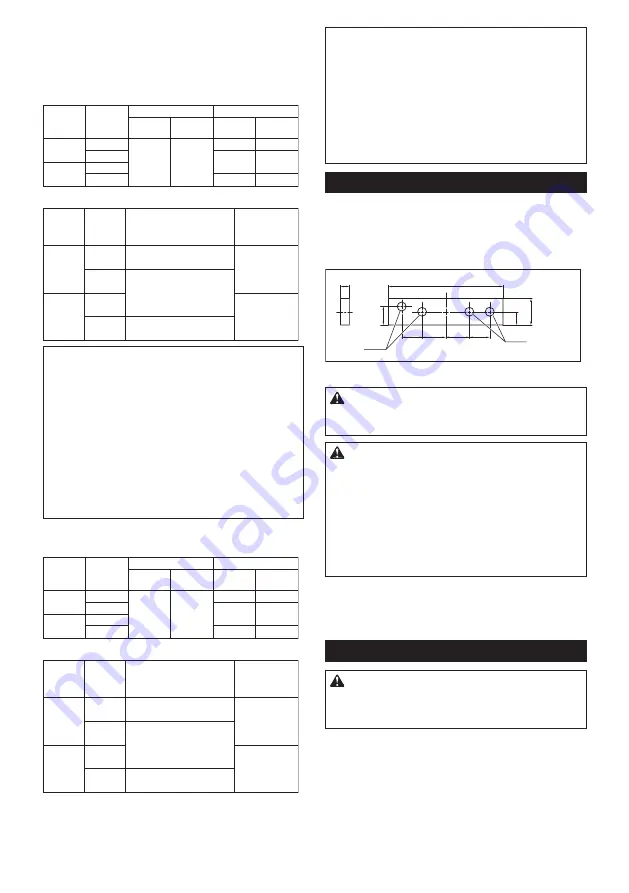
21 ENGLISH
When cutting crown and cove moldings, set the bevel
angle and miter angle as indicated in the table (A) and
position the moldings on the top surface of the saw
base as indicated in the table (B).
In the case of left bevel cut
Molding
position in
Fig. A
Bevel angle
Miter angle
For outside
corner
For inside
corner
52/38° type 45° type
Right 31.6°
45° type
Left 33.9°
Left 30°
52/38° type
Left 31.6° Left 35.3°
Right 35.3°
Right 35.3°
Right 31.6°
(1)
(2)
(3)
(4)
Table (A)
Molding
position in
Fig. A
Molding edge against
guide fence
(1)
Ceiling contact edge should
be against guide fence.
Ceiling contact edge should
be against guide fence.
For
outside
corner
Finished piece
will be on the
Left side of
blade.
Finished piece
will be on the
Right side of
blade.
For inside
corner
Wall contact edge should be
against guide fence.
Finished piece
(2)
(3)
(4)
Table (B)
EXAMPLE
In the case of cutting 52/38° type crown
molding for position (1) in Fig. A:
•
Tilt and secure bevel angle setting to 33.9°
LEFT.
•
Adjust and secure miter angle setting to 31.6°
RIGHT.
•
Lay crown molding with its broad back (hidden)
surface down on the turn base with its CEILING
CONTACT EDGE against the guide fence on
the saw.
•
The finished piece to be used will always be
on the LEFT side of the blade after the cut has
been made.
In the case of right bevel cut
Molding
position in
Fig. A
Bevel angle
Miter angle
For outside
corner
For inside
corner
52/38° type 45° type
Right 31.6°
45° type
Right 33.9° Right 30°
52/38° type
Left 31.6° Left 35.3°
Right 35.3°
Right 35.3°
Right 31.6°
(1)
(2)
(3)
(4)
Table (A)
Molding
position in
Fig. A
Molding edge against
guide fence
(1)
For
outside
corner
For inside
corner
Finished piece
(2)
(3)
(4)
Table (B)
Finished piece
will be on the
Left side of
blade.
Finished piece
will be on the
Right side of
blade.
Wall contact edge should be
against guide fence.
Wall contact edge should be
against guide fence.
Ceiling contact edge should
be against guide fence.
EXAMPLE
In the case of cutting 52/38° type crown
molding for position (1) in Fig. A:
•
Tilt and secure bevel angle setting to 33.9° RIGHT.
•
Adjust and secure miter angle setting to 31.6°
RIGHT.
•
Lay crown molding with its broad back (hidden) sur-
face down on the turn base with its WALL CONTACT
EDGE against the guide fence on the saw.
•
The finished piece to be used will always be on the
RIGHT side of the blade after the cut has been made.
Wood facing
Use of wood facing helps to assure splinter-free cuts
in workpieces. Attach a wood facing to the guide fence
using the holes in the guide fence.
See the figure concerning the dimensions for a sug
-
gested wood facing.
1
1
35mm
(1-3/8")
100mm 70mm
92mm
85mm
(3-3/8")
(2-3/4")
(3-15/16")
(3-5/8")
27mm (1-1/16")
(2"-2-3/8")
50mm-60mm
Over 420mm (16-1/2")
Over 15mm (5/8")
1.
Holes
CAUTION:
•
Use the straight wood of even thickness as the
wood facing.
WARNING:
•
Use screws to attach the wood facing to the
guide fence. The screws should be installed
so that the screw heads are below the sur
-
face of the wood facing so that they will not
interfere with the positioning of the material
being cut.
Misalignment of the material being
cut can case unexpected movement during the
cutting operation which may result in a loss of
control and serious personal injury.
NOTICE:
•
When the wood facing is attached, do not turn the
turn base with the handle lowered. The blade and/
or the wood facing will be damaged.
Cutting repetitive lengths
CAUTION:
For the tool equipped with the hold
-
ers and the holder assemblies as standard acces-
sories, this type of use is not permitted due to the
country regulations.
►
Fig.44:
1.
Set plate
2.
Holder
3.
Screw
When cutting several pieces of stock to the same
length, ranging from 220 mm to 385 mm, use of the set
plate (optional accessory) will facilitate more efficient
operation. Install the set plate on the holder (optional
accessory) as shown in the figure.
Align the cutting line on your workpiece with either the
left or right side of the groove in the kerf board, and
while holding the workpiece from moving, move the
Summary of Contents for DLS713
Page 2: ...1 1 181 mm 181 mm 8 5 x 2 1 4 3 1 2 Fig 5 1 2 3 Fig 6 1 2 3 Fig 1 Fig 2 Fig 3 Fig 4 Fig 7 2...
Page 3: ...1 1 2 1 1 1 2 1 2 3 4 5 1 2 3 2 3 1 Fig 8 Fig 9 Fig 10 Fig 11 Fig 12 Fig 13 Fig 14 Fig 15 3...
Page 9: ...1 2 Fig 56 9...
Page 25: ...25 Ni MH Li ion EN62841 3 9 LpA 88 A LWA 98 A K 3 A EN62841 3 9 ah 2 5 2 K 1 5 2 A...
Page 26: ...26 1 2 100 3 4 5 1 6 100 7 8 9 10 11 12...
Page 27: ...27 13 14 15 16 17 18 19 20 21 22 EN847 1 1 2 3 4 5 6 7 8 9 10 11 12 13 14 15 16 17 18...
Page 29: ...29 2 1 3 1 4 1 5 1 2 3 4 6 1 2 3 7 1 2 3 8 1...
Page 30: ...30 9 1 2 75 100 50 75 25 50 0 25 10 1 11 1 1 2 3 4 Makita 12 1 2 13 1 2 3 4 5...
Page 31: ...31 2 14 1 2 3 15 1 2 3 190 16 1 2 17 1 18 1 2 3 4 5 19 1 2 20 1 2 3...
Page 32: ...32 21 1 2 30 6 35 1 4 Makita 22 1 2 3 23 1 2 24 1 Makita 25 1 2 3 4...
Page 34: ...34 34 1 2 35 1 2 3 4 5 6 7 36 1 2 3 4 120 37 1 2 12 38 1 2 12...
Page 35: ...35 39 1 2 52 97 40 1 2 41 1...
Page 38: ...38 45 1 46 1 47 0 0 0 0 48 1 2 49 1 2 50 1 2 3 0 0 0...