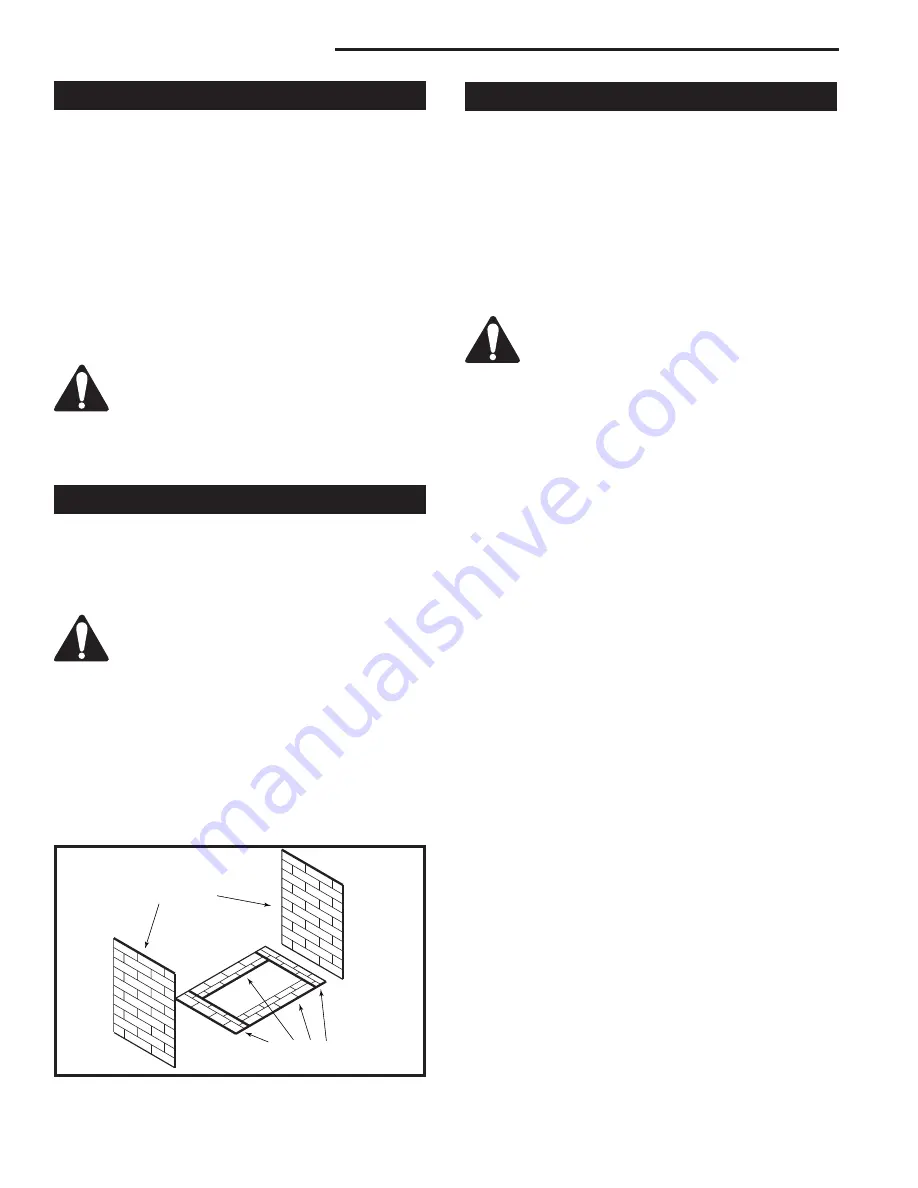
24
360 DVS Series Direct Vent Fireplaces
10006326
Glass Cleaning
It is necessary to periodically clean glass. During start-
up, condensation, which is normal, forms on the inside
of the glass. This condensation causes lint, dust and
other airborne particles to cling to glass surface.
Also initial paint curing may deposit a slight film on the
glass. It is therefore recommended glass be cleaned
two or three times with a non-ammonia based house-
hold cleaner and warm water. The use of fireplace glass
cleaner is recommended within the first few weeks of
operation.
After the initial cleaning process the glass should be
cleaned two or three times during each operating sea-
son depending on the environment in the house.
Clean the glass after the first two weeks of
operation.
Do not clean the glass when hot.
Do not use an abrasive cleaner.
Do not strike or slam the glass.
Ceramic Refractory Installation
The vertical refractory panels are installed in the unit
prior to shipment. For assembly procedures, refer to
Figure 39.
1. Unpack the ceramic refractory panels from the car-
ton.
Handle the refractory material carefully, the
panels are fragile.
2. Place the two end floor refractory panels on the base
of the fireplace.
3. Place both side panels along the side of the base.
NOTE:
360DVS2 is the only 360DV unit that is fitted
with two (2) end vertical panels, as shown in Figure
39. 360DVSL and 360DVSR units are each fitted
with one end vertical panel and two side vertical
panel. The 360DVS3 has only one end vertical
panel.
FP1446
Cer_refract_panels-designer
360DVS
Vertical Panels in
Place When Shipped
Floor Panels Placed
During Installation
Fig. 39
Ceramic panel installation.
FP1446
Log Installation
Refer to Figures 40 and 41 for log location and align-
ment.
Because of the log stack design, these instructions can
be followed from either side of the fireplace. To follow
these instructions, identify the logs by the number cast
into the underside.
For correct operation of the fireplace, the logs must be
correctly placed in the sequence described below:
1. Unpack the logs from the shipping carton. The logs
are fragile; handle them carefully.
Handle and dispose of plastic bags in
which logs were shipped in a safe manner.
As with all plastics, they are not toys and
should be kept away from infants.
2. Remove both sides of the window frame assembly
(where applicable).
3. Place the
log rear (B120
) on the grate. The square
hole located on the underside of the log is to be
placed over the center of the grate. The inner end
of the log ensures that the bottom hole is located on
the pin of the support.
4. Place the
log front left (B121)
on the grate. The
square hole located on the underside of the log is to
place over the corner leg of the grate. The inner end
of the log ensures the bottom holes are located on
the pin of the support.
5. Place the
log front right (B122)
. Once more, the
square hole fits over the corner leg of the grate.
The inner end of this log maintains a recess on the
underside, which locates over the knob on the top of
the
log front left (B121)
to secure the inner end in
place.
6. Place the
log rear left (B123)
. The bottom back of
the log rests on the grate. The notch at the back of
the log locates over the knob on the top of the
log
rear (B120)
. The bottom of the log rests on top of
the
log front left (B121)
.
7. Place the
log bottom left (B124)
. The log maintains
a step on the outer end, which rests against the
prong of the grate. The alternate end rests on the
side floor refractory panel.
8. Place the
log rear right (B125)
. The log maintains a
hole on the underside, which rests over the knob on
the top of the
log rear (B120)
. The bottom of the log
rests against the side floor refractory panel, and the
side rests against the last prong of the grate.
9. Place the
log center (B126)
. The log maintains a
hole on the underside, which rests over the knob on
the top of the
log front right (B122)
. The alternate
end rests against the side floor refractory panel and
positions between the two (2) prongs of the grate.