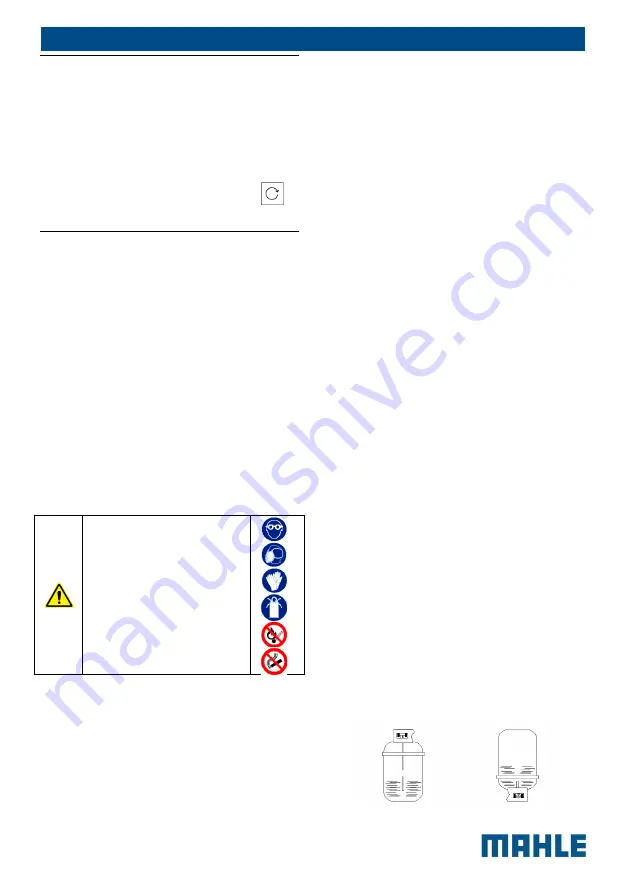
EN | 18 | AIR-NEX 9350/9450 | Commissioning
© MAHLE
8.2
Software update
It is possible to check for software
updates via Wi-Fi and download them
inside the
•
Main Menu
o
Setup
Updates Check
8.3
Initial verification
Execute the following actions in sequence
by following the display guided procedure
and the illustrations on the screen of the
equipment:
•
Gas weight verification
•
Oil weight verification
•
First vessel filling
It is possible to interrupt the initial
verification, the station will propose at
next powering to continue.
The equipment cannot operate until all
the steps of the initial verification have
been completed.
CAREFULLY ABIDE BY
THE FOLLOWING
INSTRUCTIONS TO
AVOID DANGER TO
PERSONS, THE
DISCHARGE OF
REFRIGERANT IN THE
ATMOSPHERE
Let us consider as first filling the one
carried out during the initial check with
internal tank of the equipment free of
refrigerant and containing air.
Set the quantity of refrigerant to fill (at
least 3 kg) and follow the guided
procedure shown on the display.
Check that the equipment hoses are not
connected and positioned in the hose
winder. Start the procedure that initially
implies the creation of vacuum in the
internal tank. This phase will take 15
minutes and will act on the whole
equipment.
Only when the message appears asking
to connect the charge tank, connect the
LP quick coupler (colour blue) of the unit
to an external refrigerant tank using the
supplied adaptor.
When the message occurs open the
coupler by turning the knob clockwise.
Open the valve on the external tank.
Just right before reaching the planned
quantity of refrigerant, the unit will stop
and ask the user to close the external
refrigerant tank. Then, the device will
continue the recovery from the hoses and
ends when these are empty. Hence, it is
necessary to open the LP quick-coupler
and disconnect it from the external tank.
Thanks to the ECO LOCK® function, the
refrigerant - usually kept between the
cylinder fitting and the hose quick-coupler
until the end of the process - will not be
released in the environment.
There may be two types of source tanks:
with plunger and without plunger.
Tanks with plunger shall remain upright
to be able to transfer liquid refrigerant; for
this type of tanks connect to the L (liquid)
coupler.
Tanks without plunger have only one
valve, so they must be turned upside
down to transfer the liquid refrigerant.
Summary of Contents for AIR-NEX 9350
Page 2: ......
Page 4: ...EN 2 AIR NEX 9350 9450 CONTENTS MAHLE 15 Spare parts 34...