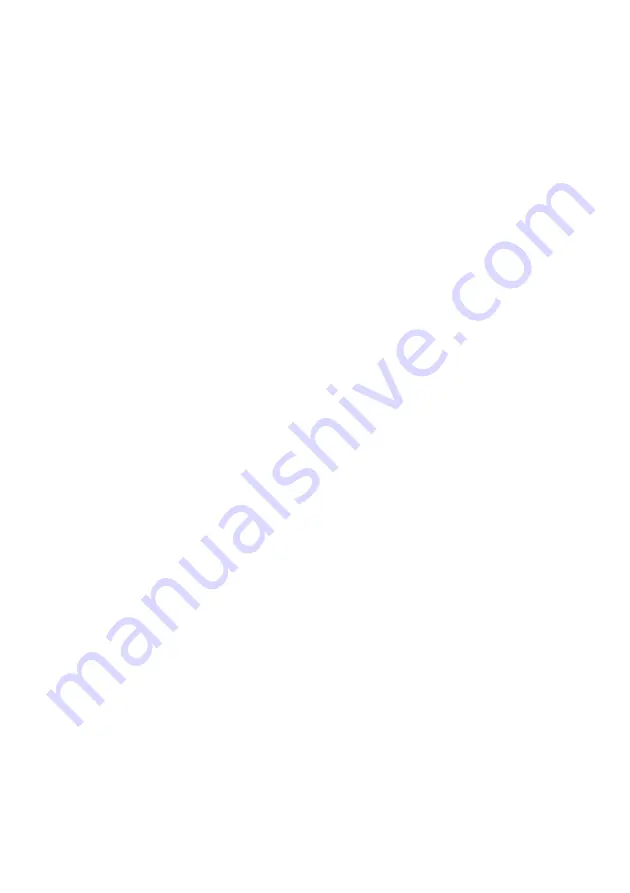
11
4. The end of the wire wound on the spool, flatten or cut off the bent section, then
4. The end of the wire wound on the spool, flatten or cut off the bent section, then
file off, so that was not sharp.
5. To allow the insertion wire feeder release the pressing mechanism,
5. To allow the insertion wire feeder release the pressing mechanism,
by pulling the lever from the knob force control pressure.
6. End of the wire inserted into the guide at the rear of the tray, carry
6. End of the wire inserted into the guide at the rear of the tray, carry
it above the drive rollers and plug to the port leading to the welding torch.
7. Push wire in the grooves of the drive rollers by tightening the clamp.
7. Push wire in the grooves of the drive rollers by tightening the clamp.
8. Remove gas nozzle and contact tip, unscrew.
8. Remove gas nozzle and contact tip, unscrew.
9. Switch on the device.
9. Switch on the device.
10. Handle develop so that it is in a straight line, then press the button on the handle until
10. Handle develop so that it is in a straight line, then press the button on the handle until
the emergence of a wire in the outlet (approx. 20 mm), release the button.
Hold the handle outlet
the emergence of a wire in the outlet (approx. 20 mm), release the button.
Hold the handle outlet
towards the ground, to protect yourself and others from accidental injury to the extending wire.
11. Screw the contact tip, replace the gas nozzle.
11. Screw the contact tip, replace the gas nozzle.
12. Adjust the contact pressure feed roller by rotating the platen knob. Too small force
12. Adjust the contact pressure feed roller by rotating the platen knob. Too small force
pressure, will cause slippage of the drive roller. Too much contact force, increases the resistance of
administration and the deformation of the wire, which in turn may result in cutting or jam.
7.4 Connection of protective gas.
1. The cylinder with a suitable protective gas should be set for example by the wall and prevent it from
1. The cylinder with a suitable protective gas should be set for example by the wall and prevent it from
tipping over, securing it to the support by means of a chain.
2. Remove the protective cap and the second valve unscrew the bottle to remove any impurities.
2. Remove the protective cap and the second valve unscrew the bottle to remove any impurities.
3. Install the regulator so that the gauges were in the upright position.
3. Install the regulator so that the gauges were in the upright position.
4. Combine with semi-cylinder (outlet of the regulator nozzle clip) corresponding hose. Connector for
4. Combine with semi-cylinder (outlet of the regulator nozzle clip) corresponding hose. Connector for
connecting the protective gas is placed at the rear.
5. Unscrew the regulator valve just prior to welding. After completion of welding, spin the cylinder valve should
5. Unscrew the regulator valve just prior to welding. After completion of welding, spin the cylinder valve should
be.
6. Avoid welding in the open air or within - a blast of air can disrupt the flow of the shielding gas and
6. Avoid welding in the open air or within - a blast of air can disrupt the flow of the shielding gas and
liquid metal strip protection.
7.5 MIG-MAG
The user is able to control the wire feed speed and welding current.
Increase welding current increases penetration (penetration depth) and elongation of the arc. When welding
positions and pułapowych wall, you can reduce the welding current, the performance of joint filler to achieve
a smooth face, you can increase the welding current.
7.6 Practical recommendations MIG-MAG welding.
Butt welds in the flat position must be carried out using "push" for thin components and
technology "pull" for items thicker. Butt welds in vertical position for thin elements should be done
from top to bottom. Fillet welds in position nabocznej should be carried out using "push", but with an
additional tilt bracket