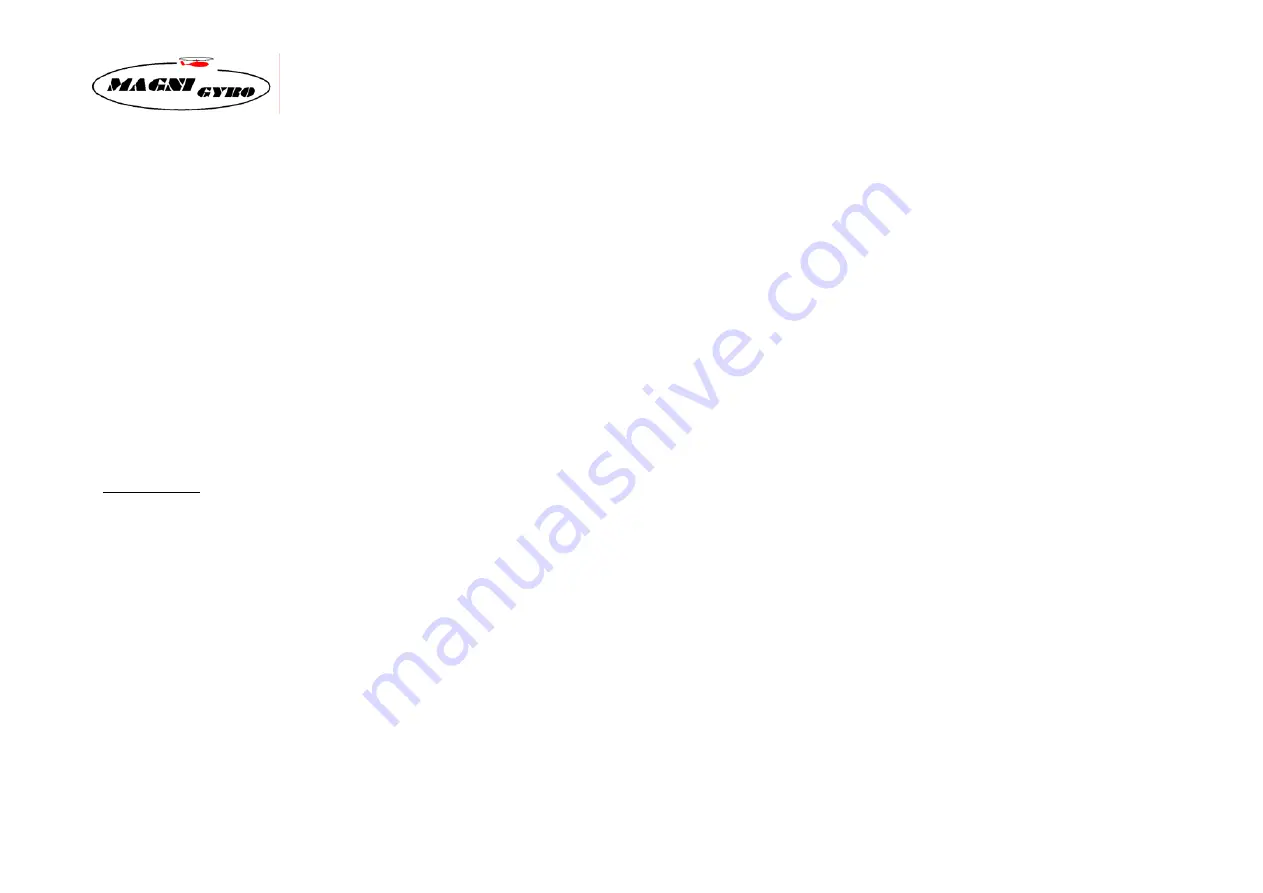
045-00-24_A M24 MAINTENANCE SCHEDULE
Issue A
Page 17
A20 Trim System
Check:
a)
Security of the trim actuator and integrity of the control cable, springs and electric connections.
A21 Fuel System
Check:
a)
That the quantity of fuel is adequate for the flight planned;
b)
The fuel pipes and connectors for serviceability and any sign of leakage;
c)
The fuel filter is clean and that there are no signs of leaks;
d)
The fuel tank surfaces and seams.
Draw a sample of fuel from the drain point and check the sample for any water or other contaminant.
A21 Fuel Level
Check:
a)
The fuel level.
WARNING: This operation must be done using the tank sight gauge on the rear left-hand side of the fuel tank (open cowling flap to view).
A23 Control Rods – Left Hand Side
Check:
a)
Condition and security of the safety points on the control rods, linkages, bearings and fiberlock nuts. There should be
insignificant play in the “Uniball” rod-end bearings and no evidence of corrosion or damage. The control rods should be
straight and undamaged. The control rods should be free to rotate slightly around their axis when gripped and given a light
twist. Any undue force needed or inability to twist the bearing may indicate a problem of the bearing and should be further
investigated;
b)
The rotor brake and cables for freedom of movement and correct function;
c)
The state of the rotor tachometer pick-up and make sure it is secure.
A24 Cockpit and Fuselage – Left Hand Side
Check:
a)
State of external surface of fuselage and remove foreign objects and dirt;
b)
Check doors (if fitted) are secure; hinges are secure and undamaged, locking mechanism working correctly;
c)
Inspect transparencies for fixing, damage and cleanliness.