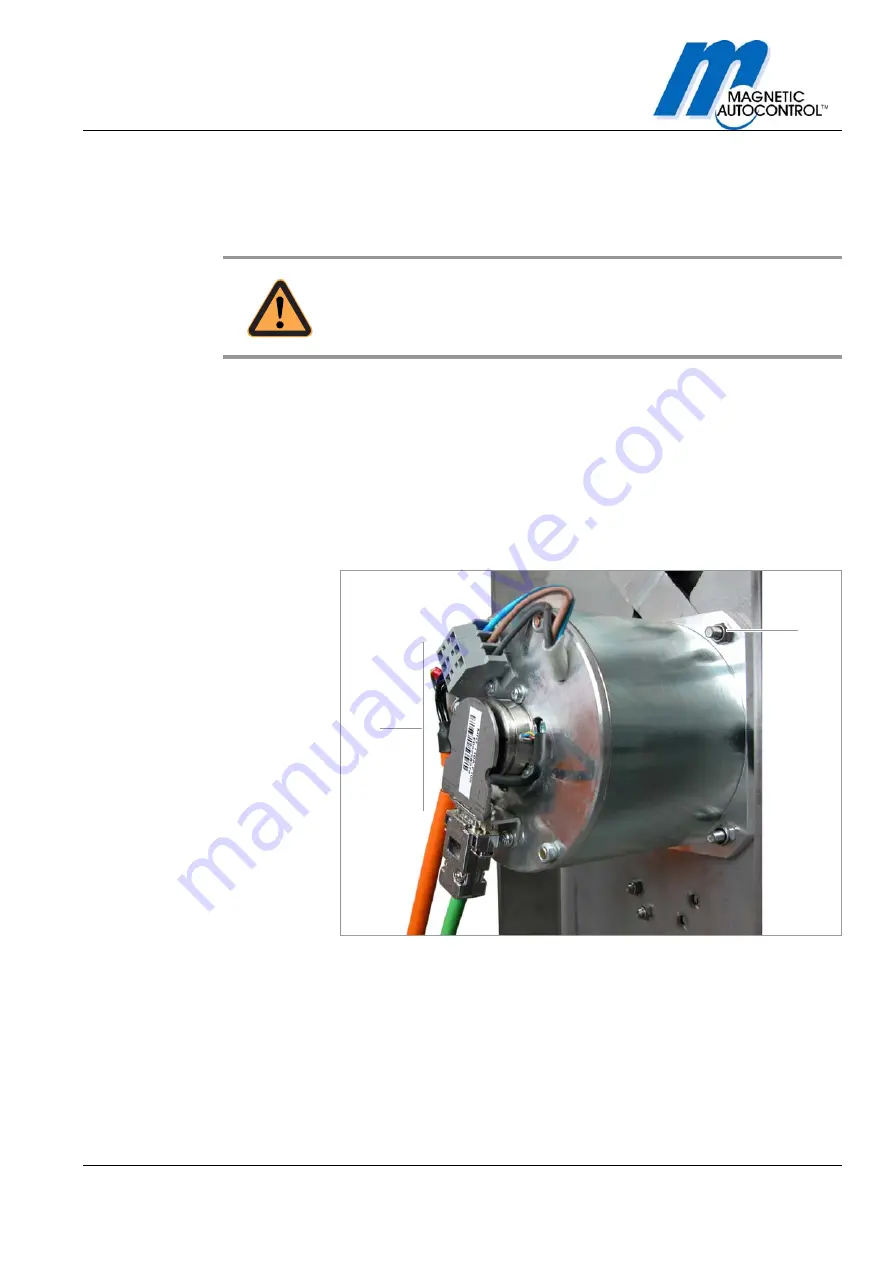
Maintenance
581E,5721/ 07/2006 MPR112_1
page 64/72
Version: 01
10.6. Motor replacement
CAUTION!
Before starting any kind of maintenance work make sure that the
main power supply is switched OFF!
If it is necessary to replace the MHTM (MAGNETIC High Torque
Motor) proceed stepwise as follows:
-
Open the service door at the housing; refer to chapter 4.2
“Access Doors” on page 20. A free access to the driving compo-
nents must be ensured.
-
Hang out the return spring(s). See Fig. 9-1 on page 62.
Fig. 9-2
Motor replacement
-
Loosen the socket head screw of the lever on the motor drive
shaft (see chapter 0 “Dismounting the wing” on page 62).
-
Disconnect the cable connectors at the backside of the motor
.
-
Remove the four motor mounting screws
.
-
Take the motor out of the housing.