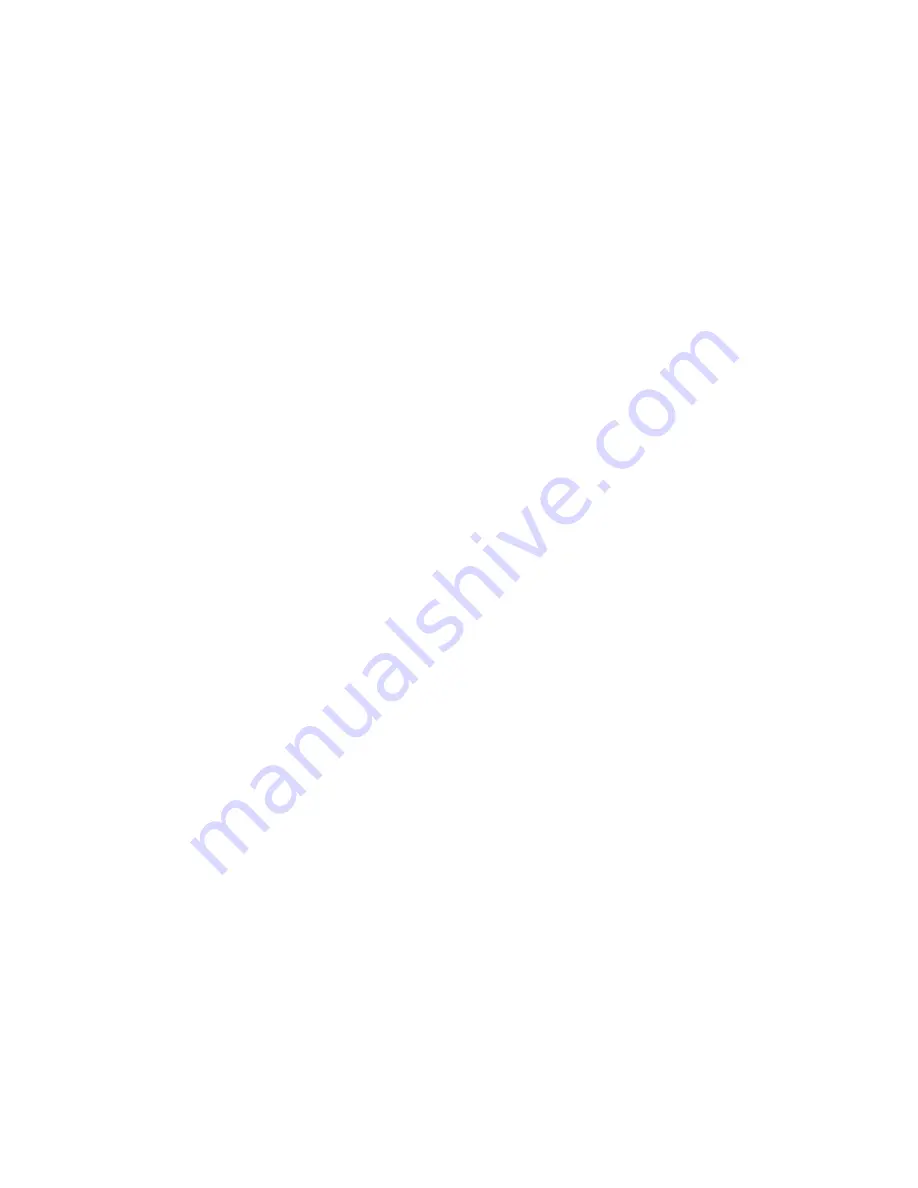
25
8.5.1.7
Hook up weld Head to Controller. All connections are specific.
Emphasize do not force connection, and if difficult, probably
incorrect.
8.5.1.8
Gas In from gas supply, Gas Out to Weld Head.
8.5.1.9
Ensure water lines are correctly mated by color.
8.5.1.10 View fuses and connections.
8.5.1.11 Connect
Pendant.
8.5.1.12 Following connection of Weld Head, Controller, and Power
Source, power up unit.
8.5.1.13 Check for water leaks and adjust for suitable gas flow.
8.5.1.14 For pneumatic push button option install special
regulator/flowmeter and connect pneumatic line in torch cable
to the regulator.
8.5.2 WELD HEAD SET-UP - PIPELINER IIC
8.5.2.1 Explain guide ring function.
8.5.2.2 Demonstrate guide ring installation.
8.5.2.3 Special attention to gap spacing at dovetail joint being equal, and
distance and squareness to joint to be welded.
8.5.2.4 Explain the use of adaptors for smaller pipe OD’s.
8.5.2.5 Initial weld Head set-up Pipeliner IIC
A.
Install filler wire on Head. Discuss importance of
precision/level wound, clean wire.
B.
Explain torch components and wire conducting, break
down to view components and change out procedures.
Demonstrate cleaning.
8.5.2.6 Weld Head Installation.
A.
Install Pipeliner II on properly positioned guide ring
B.
Emphasize guide ring placement and the minimized
steering required when in correct position
C.
Demonstrate torch removal, maintenance and cleaning
while on pipe.
Summary of Contents for 609AF0A0C0
Page 12: ...9...
Page 13: ...10...
Page 27: ...24...
Page 34: ...31...
Page 40: ...37 Undercutting 1 Reduce power 2 Reduce welding speed 3 Shorten arc length...
Page 43: ...40 Remote Pendant...
Page 46: ...43 14 0 ELECTRODE EXTENSION OFTEN NEGLECTED WHEN USING SELF SHIELDED CORED WIRES...
Page 47: ...44...
Page 48: ...45...
Page 49: ...46 15 0 PREVENTING THE EFFECTS OF MOISTURE CONTAMINATION OF FLUX CORE WIRE...
Page 50: ...47...