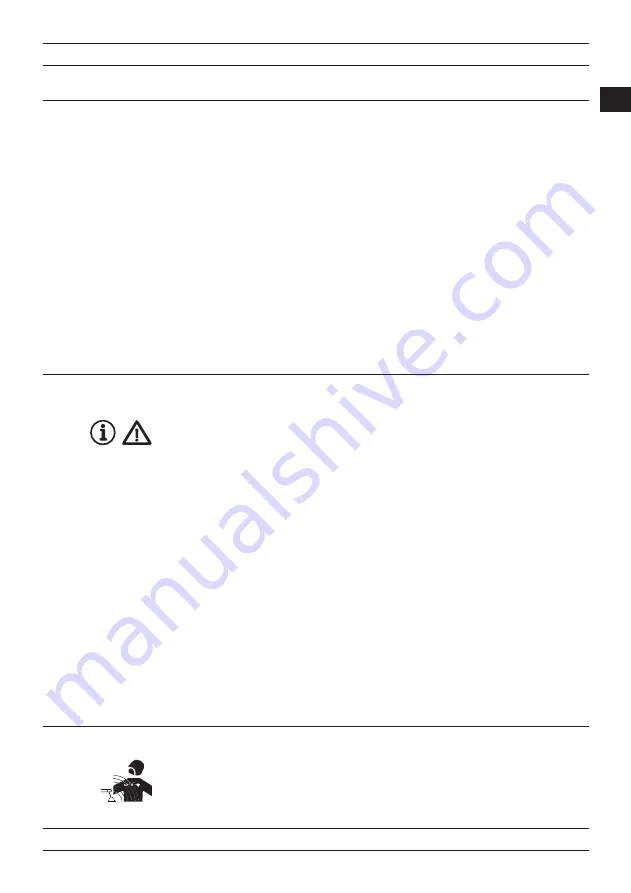
EN
9
COMPACT SMART SERIES
www.magmaweld.com
USER MANUAL
Safety Precautions
• Ensure that your welding and/or cutting machine has been installed and situated in its place
according to the user manual.
According to article 5.2 of IEC 60974-9;
Before installing the welding / cutting equipment, the person in charge of the operation and / or
the user must conduct an inspection of possible electromagnetic interference in the environment.
Aspects indicated below has to be taken into consideration;
a)
Other supply cables, control cables, signal and telephone cables, above and below the welding
/ cutting machine and its equipment,
b)
Radio and television transmitters and receivers,
c)
Computer and other control hardware,
d)
Critical safety equipment, e.g. protection of industrial equipment,
e)
Medical apparatus for people in the vicinity, e.g. pacemakers and hearing aids,
f)
Equipment used for measuring or calibration,
g)
Immunity of other equipment in the environment. The user must ensure that the other
equipment in use in the environment is compatible. This may require additional protection
measures.
h)
Considering the time during which the welding / cutting operations or other activities take
place during the day, the boundaries of the investigation area can be expanded according to the
size of the building, the structure of the building and other activities that are being performed
in the building.
In addition to the evaluation of the field, evaluation of device installations may also be necessary
for solving the interfering effect. In case if deemed necessary, on-site measurements can also be
used to confirm the efficiency of mitigation measures.
(Source: IEC 60974-9).
• The appliance must be connected to the electricity supply in the recommended manner by a
competent person. If interference occurs, additional measures may be applied, such as filtering
the network. The supply of the fixed-mounted arc welding equipment must be made in a metal
tube or with an equivalent shielded cable. The housing of the power supply must be connected
and a good electrical contact between these two structures has to be provided.
• The recommended routine maintenance of the appliance must be carried out. All covers on the
body of the machine must be closed and / or locked when the device is in use. Any changes,
other than the standard settings without the written approval of the manufacturer, cannot be
modified on the appliance. Otherwise, the user is responsible for any consequences that may
possibly occur.
• Welding / cutting cables should be kept as short as possible. They must move along the floor of
the work area, in a side by side manner. Welding / cutting cables should not be wound in any
way.
• A magnetic field is generated on the machine during welding / cutting. This may cause the
machine to pull metal parts on to itself. To avoid this attraction, make sure that the metal
materials are at a safe distance or fixed. The operator must be insulated from all these
interconnected metal materials.
• In cases where the workpiece cannot be connected to the ground due to electrical safety, or
because of its size and position (for example, in building marine vessel bodies or in steel
construction manufacturing), a connection between the workpiece and the grounding may
reduce emissions in some cases, it should be kept in mind that grounding of the workpiece may
cause users to sustain injuries or other electrical equipment in the environment to break down.
In cases where necessary, the workpiece and the grounding connection can be made as a direct
connection, but in some countries where direct connection is not permissible, the connection
can be established using appropriate capacity elements in accordance with local regulations
and ordinances.
• Screening and shielding of other devices and cables in the work area can prevent aliasing
effects. Screening of the entire welding / cutting area can be evaluated for some specific
applications.
Evaluation Of
Electromagnetic
Suitability Of The
Work Area
Electromagnetic
Interferance
Reduction Methods
The electrical current passing through any conductor generates zonal electric and magnetic fields
(EMF).
All operators must follow the following procedures to minimize the risk of exposure to EMF;
• In the name of reducing the magnetic field, the welding / cutting cables must be assembled and
secured as far as possible with the joining materials (tape, cable ties etc.).
• The operator’s body and head should be kept as far away from the welding / cutting machine
and cables as possible,
Electromagnetic Field
(EMF)
Summary of Contents for Compact Smart Series
Page 42: ......
Page 82: ......
Page 120: ......
Page 122: ......
Page 158: ......
Page 160: ......
Page 162: ...162 SMART www magmaweld com RU...
Page 163: ...163 SMART www magmaweld com RU MIG CV MMA VRD AED...
Page 164: ...164 SMART www magmaweld com RU n...
Page 165: ...165 SMART www magmaweld com RU...
Page 166: ...166 SMART www magmaweld com RU 10 2 TS EN 55011 100 IEC61000 3 12...
Page 167: ...167 SMART www magmaweld com RU 5 2 IEC 60974 9 a b c d e f g h 60974 9...
Page 168: ...168 SMART www magmaweld com RU IMF www magmaweld ru wr...
Page 171: ...171 SMART www magmaweld com RU 1 3...
Page 174: ...174 SMART www magmaweld com RU IEC 61000 3 12 2 2 30 40 C 2 1...
Page 175: ...175 SMART www magmaweld com RU 2 3 2 3 1 3 H 2 3 2 2 3 3 3 8 9 5 5 CO2 CO2 CO2 CO2 CO2 CO2 CO2...
Page 179: ...179 SMART www magmaweld com RU 3 2 1 2 1 3 7 8 6 2 4 4 5 5...
Page 180: ...180 SMART www magmaweld com RU 1 MIG MAG Pulse MIG MAG 3 MIG MAG 1 24 15 40...
Page 181: ...181 SMART www magmaweld com RU MMA Lift TIG 1 24 15 40...
Page 184: ...184 SMART www magmaweld com RU 7 8 3 7 1 3 3 1 P3 P1 P2 P3 8 2 4 2 PrG I PoG...
Page 185: ...185 SMART www magmaweld com RU PrG I PoG 4 1 0 2 9 9 0 0 9 9...
Page 188: ...188 SMART www magmaweld com RU 3 6 3 7 4 4 WD 4 4 a b c d e f V V U a b d e f d c c...
Page 189: ...189 SMART www magmaweld com RU 6 5 3 8 8 1 3 3 2 6 4 4 5 a b c...
Page 190: ...190 SMART www magmaweld com RU 8 1 e A B C D E 9 3 1 2...
Page 192: ...192 SMART www magmaweld com RU Magnet MagNET LCD OEE WR magNET...
Page 193: ...193 SMART www magmaweld com RU 10 4 1 3 6...
Page 194: ...194 SMART www magmaweld com RU 4 2...
Page 195: ...195 SMART www magmaweld com RU 0000 NOP...
Page 196: ...196 SMART www magmaweld com RU 4 3 E01 E02 E04 E05 E06 E03...
Page 199: ...199 SMART www magmaweld com RU 5 2 R S T IGBT...
Page 200: ...200 SMART www magmaweld com RU 5 3...
Page 202: ......
Page 212: ...212 KOMPAKT SMART SER S www magmaweld com KULLANIM KILAVUZU TR 1 3 r n Etiketi Teknik Bilgiler...
Page 238: ......
Page 240: ......
Page 245: ......
Page 246: ......