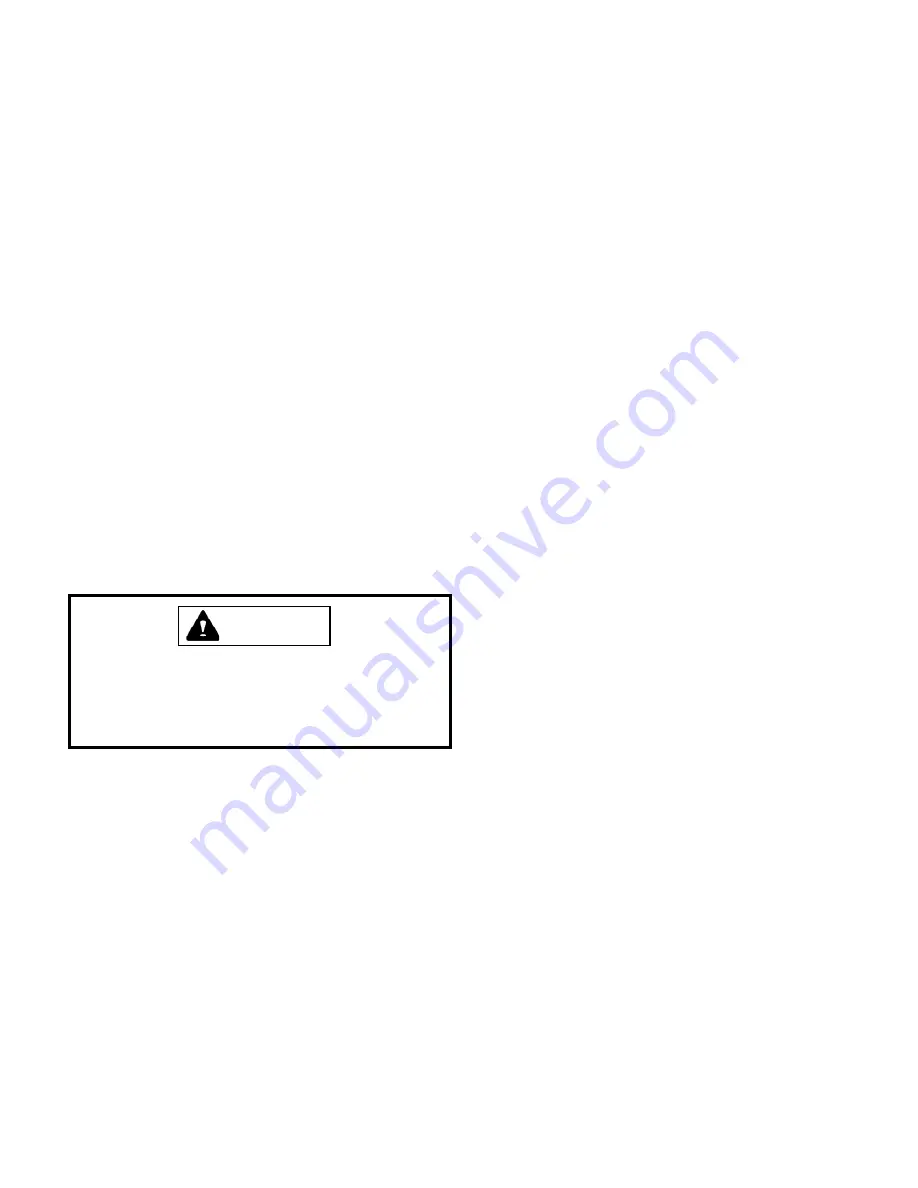
Page 3 of 21
507389-01
Issue 1504
The sleeve is not intended as the sole support for the unit.
An additional support must be provided near the return
opening on the unit for adequate support. The use of
vibration isolation material between the unit and the support
is recommended.
CAUTION
Seal the space between the wall sleeve and the building opening
with non-hardening caulking compound. The seal must be
weathertight to prevent entrance of moisture and water into
the building.
Assure that the unit is completely seated against the gaskets on
the wall sleeve.
• Return air temperature range between 60°F (16°C) and 80°F
(27°C) must be maintained.
• Air filters must be installed in the system and must be
maintained during construction.
• Air filters must be replaced upon construction completion.
• The input rate and temperature rise must be set per the
furnace rating plate.
• One hundred percent (100%) outdoor air must be provided
for combustion air requirements during construction.
• The furnace heat exchanger, components, duct system, air
filters and evaporator coils must be thoroughly cleaned
following final construction clean-up.
• All furnace operating conditions (including ignition, input
rate, temperature rise and venting) must be verified
according to these installation instructions.
Installing With a Wall Sleeve
Refer to the installation instructions packed with the wall sleeve
and Figure 1 for guidance in assembly and mounting using a
wall sleeve.
Make sure the gaskets attached to the sleeve are not damaged.