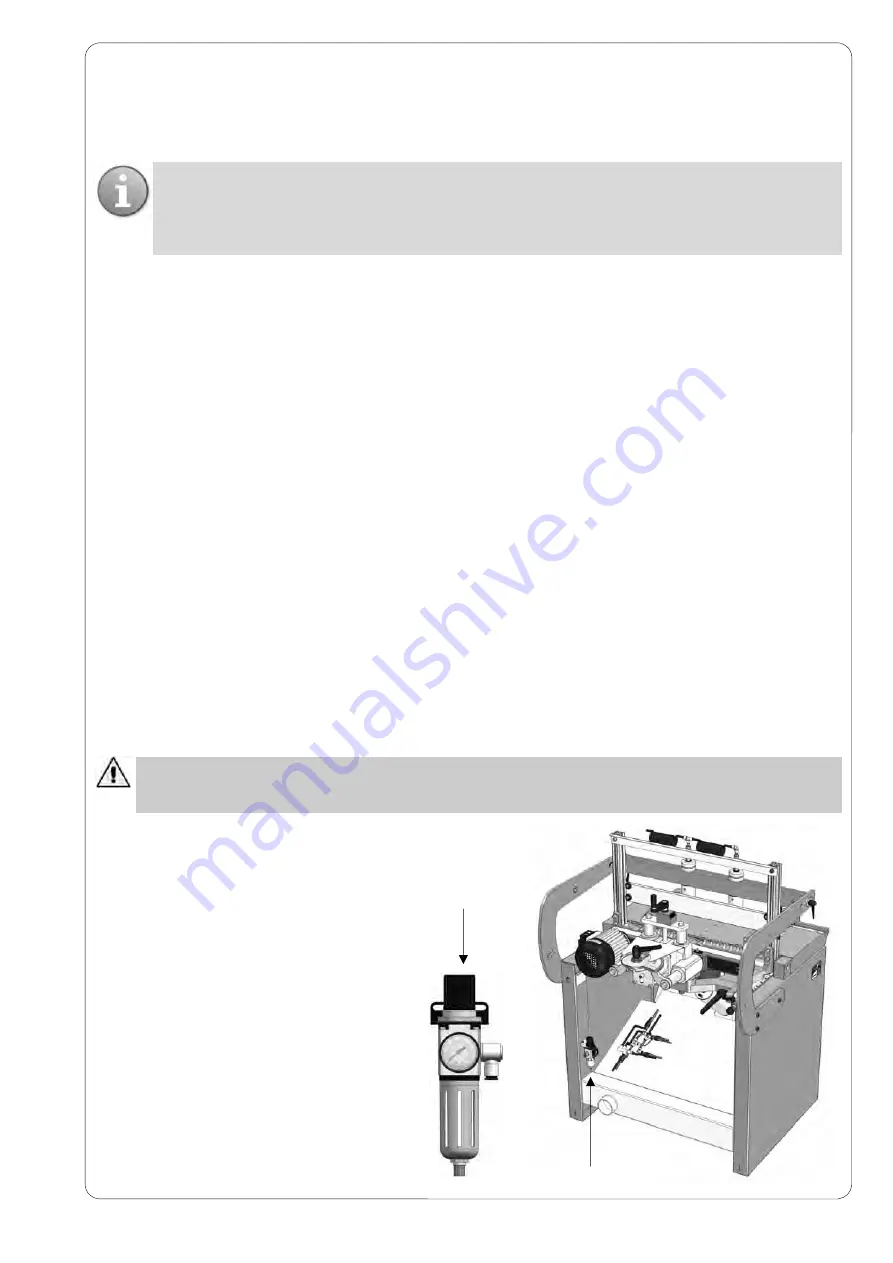
Pag. 12
WOOD SHAVINGS REMOVAL
The wood shavings and waste resulted during the work cycle should be removed in compliance with the stan-
dards in force in the Country of Use of the machine.
Please contact the competent bodies in the Country of Use, in order for them to provide you with the relevant
standards in force.
Warning:
the machine is intended for aspiration, but it is not provided with a vacuum
system; the customer should provide this device, based on the processed material
and frequency with which the machine is used. Please install a suitable system, able
to maintain the dust concentration below the TLV provided in the Country of use.
Attention: we strongly recommend that the connection to the electrical power supply is
done by technical qualified personnel only.
14.2 PNEUMATIC CONNECTION
Connect the Filter regulator unit with the air
line through a rubber or nylon hose with a
minimum inside diameter of 8 mm.
If the pipe length exceeds 5/6 metres it is ad-
visable to increase the inside diameter to 10
mm, you are also recommended to install a
supply shut-off valve on the machine with
manual control complete with air relief.
The Filter purifies the air from dust and hu-
midity protecting the valves or seals in the
pneumatic cylinders.
14.3 MACHINE STARTING
The work station and control panel are on
the machine electric panel. The operator
places the pieces on the work table after
adjusting the stops.
6
14. MACHINE CONNECTION TO EXTERNAL POWER SUPPLY
After machine assembling and installation, connect it with:
Electrical power supply
Pneumatic power supply
Dust suction system
14.1 CONNECTION TO ELECTRICAL POWER SUPPLY
To gain access to the machine electric system, open the main board door by loosening the screws on the front
of it. We recommend not to connect the machine to the electrical power supply until it is not correctly placed in
the right place. Before connecting the machine to the electrical power supply, it is necessary to verify that the
electrical system corresponds to the following necessary power and safety requirements:
Grounded equipotential electrical system
Presence of fuses or protection switches against short circuits on every conducing cable R-S-T, except
the grounded one
The electrical power system must be in conformity with CEI 64.8 (CENELEC HD 384, IEC364-4-41) rules
Voltage and frequency for the motors are specified on the plates placed on them
Connect the power supply cable to R-S-T terminals
Automatic protection devices installed upstream respect to the machine; they have to be coordinated to
guarantee the automatic break according to above mentioned rules.
The electrical connection is done by three-phase plug (or single-phase plug, depending on the panel).
The cable for ground connection is yellow-green.
The tolerance of admissible voltage is +/-10%
When voltage is applied to the electrical power supply, check that the spindles rotation direction is the one writ-
ten in the plate placed on the head (Black=Right; Red=Left).
If the rotation direction does not match the one impressed in the plate, please invert the connection cables to
three phase power supply. For any information please see the electrical diagrams included in this manual.
Summary of Contents for 16271400
Page 2: ...This page intentionally left blank...
Page 4: ...This page intentionally left blank...
Page 7: ......
Page 38: ...1 26273000 Pag 31...
Page 40: ...Pag 33 2 26272100...
Page 42: ...3 26271200 Pag 35...
Page 44: ...Pag 37 4 26271301...
Page 46: ...Pag 39 5 26271300...
Page 48: ...Pag 41 6 26271400...
Page 50: ...7 26272500 Pag 43...
Page 52: ...8 26271600 Pag 45...
Page 54: ...9 262517 Pag 47...
Page 56: ...Pag 49 10 26054810...
Page 58: ...PNEUMATIC SYSTEM Pag 51...