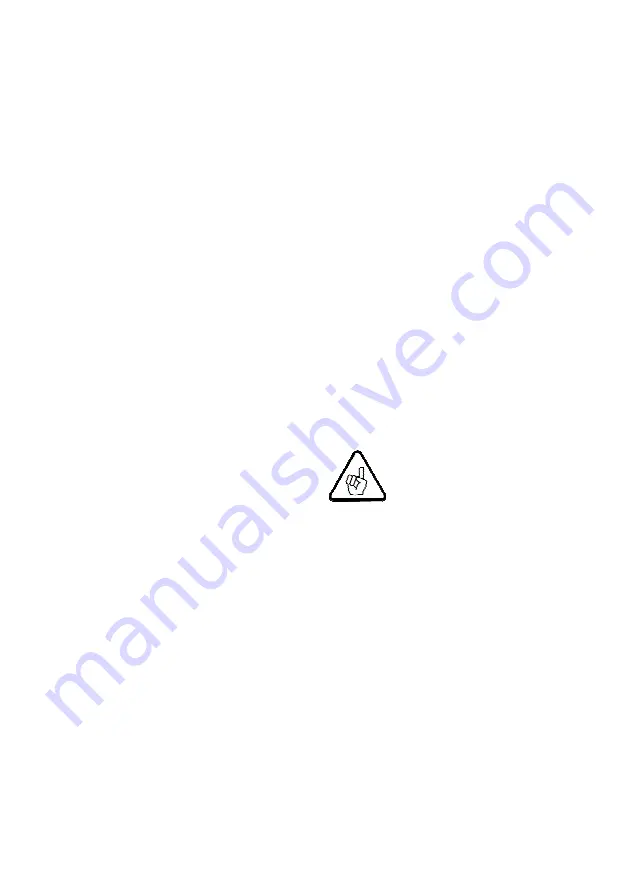
-26-
Reach through the front handle recess 10 (Fig.
10 – page 4) and pull the spring catch 20
forward. Lift the table insert 17, pull it forward
and remove it.
Push the riving knife/splitter with its retaining
bracket downward into the latching position for
concealed cuts.
Release the two hexagon socket head cap
screws 27 (Fig. 11 - page 4) and adjust the
riving knife/splitter 3 according to Fig. 11 with
regard to its distance to the tooth rim and its
height.
Tighten the hexagon socket head cap screws
27.
Reattach the table insert and install the upper
saw guard (see chapter 4.5).
The kerf guide can be engaged in two positions
without requiring tools
:
-
upper position with saw guard - for normal cuts
-
lower position without saw guard - for covered cuts
In order to attain the respective position just pull the
kerf guide upwards and forward or press it down and
to the rear.
4.7 Application as pull-push saw
The special advantage when using the saw as pull-
push saw is the trouble-free and accurate separating
of fixed workpieces up to max. 215 mm (8 7/16 in.)
cutting length, e.g. panels. Apply the workpiece
against the stop plate rail 6 (Fig. 1 - page 3) of the
universal stop 7. Push the handwheel 8 downwards
and pull the saw unit with the handwheel forward.
After completing the cutting procedure the saw unit
runs back to the home position and is stopped there
automatically.
4.8 Application as circular saw bench
Slitting of larger workpieces is carried out with the
circular saw bench function. For this purpose, position
the sawing unit in the foreseen table position. To do
so, push the handwheel 8 (Fig. 3 - page 3)
downwards and pull the saw unit forward until the
circular recess in the pull rod 43 becomes visible.
Lock the saw unit in this position by pushing the slide
bar 42 upwards on the side.
At the same time, use the universal stop 7 (Fig. 2 –
page 3) as parallel stop. In the process, you can
insert the stop plate rail 6 depending on the
workpiece dimensions either with its high workpiece
guiding surface or turned by 90 with its low bearing
surface 6 (Fig. 5 – page 3).
You can return to the push-pull saw function by
pulling slide bar 42 diagonally downwards.
5 Operation
5.1 Initial operation
Personnel entrusted to work with the machine must
be made aware of the operating instructions, calling
particular
attention
to
the
chapter
"Safety
instructions".
5.2 Switching on and off
Switching on:
Press the green switch button 12
(Fig. 3 – page 3).
Switching off:
Press the red switch button 11.
The saw shaft is automatically braked, reducing
the slowing down time to less than 10 s.
5.3 Overload protection
Triggering of the motor protection is
always a sign for motor overload,
whereby the cause must be
determined and eliminated.
The speed is automatically reduced when the motor
is overloaded respectively the motor is automatically
shut down in the case of power failure. You can turn
the motor on again after the power supply has been
resumed.
5.4 Cutting depth adjustment
The cutting depth can be steplessly adjusted by
turning the handwheel 17 (Fig. 8 - page 4) from 0 to
85 mm (0 – 3 3/8 in.). Turning clockwise increases
the cutting depth; turning anticlockwise decreases the
cutting depth.
In order to achieve good cutting quality, the adjusted
cutting depth of the saw blade should be approx. 5
mm (1/4 in.) more than the processed material
thickness.
Depending upon the position of the kerf guide in both
latching positions, the measurement scale 38
mounted on the kerf guide and vertical to the table