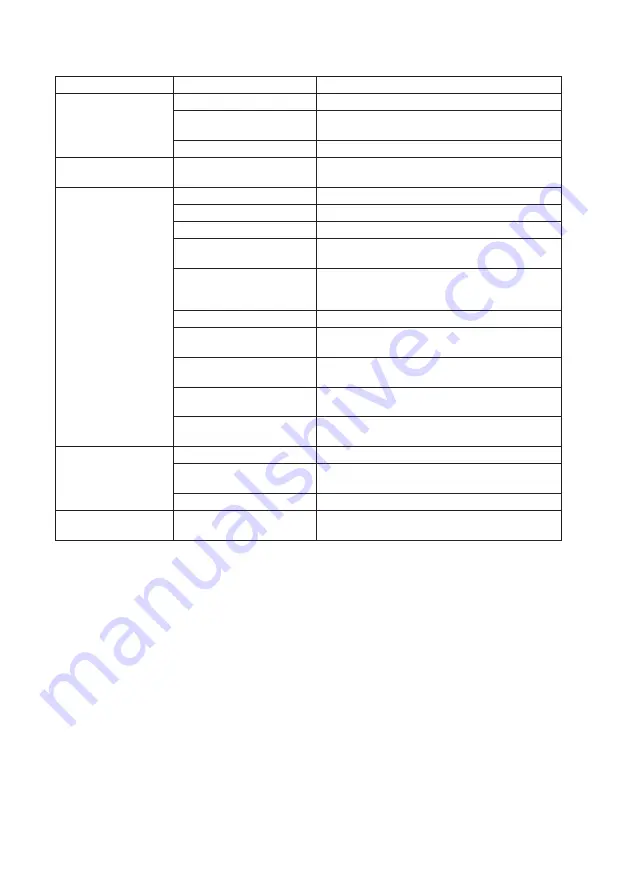
PROBLEMS AND SOLUTIONS
MAINTENANCE
All models are designed and constructed to require a minimum of maintenance.
In any case always bear in mind the following basic recommendations for a good functioning of
the pump:
- On a weekly basis, check that the tubing joints have not loosened, to avoid any leakage.
- On a monthly basis, check the pump body and keep it clean of any impurities.
- On a weekly basis, check and keep clean the line suction filter.
- On a monthly basis, check that the electric power supply cables are in good condition.
-
NOISE LEVEL
Under normal working conditions the noise emission from all models does not exceed the valve
of 70 db at a distance of 1 meter from the electric pump.
DISPOSING OF CONTAMINATED MATERIALS
In the event of maintenance or demolition of the machine, do not disperse contaminated parts
into the environment.
Refer to local regulations for their proper disposal.
ACCIDENTS
The Motor is not
turning.
The motor turns slowly
when starting.
Low or no flow rate
Increased pump noise
Leakage from the
pump body
CAUSES
Lack of electric power
Rotor Jammed
Motor Problems
Low voltage in the electric
power line
Low level in the suction tank
Foot valve blocked
Filter clogged
Excessive suction pressure
High loss of head in the
delivery circuit (working
with the by-pass open)
By-pass valve blocked
Air entering the pump or the
suction tubing
A narrowing in the suction
tubing
Low rotation speed
The suction tubing is resting
on the bottom of the tank
Cavitation occurring
Irregular functioning of the
by-pass
Air present in the diesel fuel
Seal Damaged
REMEDIES
Check the electrical connecting.
Check for possible damage or obstruction of the
rotating components.
Contact the Service Department
Bring the voltage back within the anticipated limits
Refill the tank
Clean and/or replace the valve
Clean the filter
Lower the pump with respect to the level of the
tank or increase the cross-section of the tubing
Use shorter tubing or of greater diameter
Dismantle the valve, clean and/or replace it.
Check the seals of the Connections
Use tubing suitable for working under suction
pressure
Check the voltage at the pump. Adjust the voltage
and/or use cables of greater cross-section
Raise the tubing
Reduce suction pressure
Dispense fuel until the air is purged from the
by-pass system
Verify the suction connection
Check and replace the seal
E11
Summary of Contents for FTWM120-001
Page 19: ......