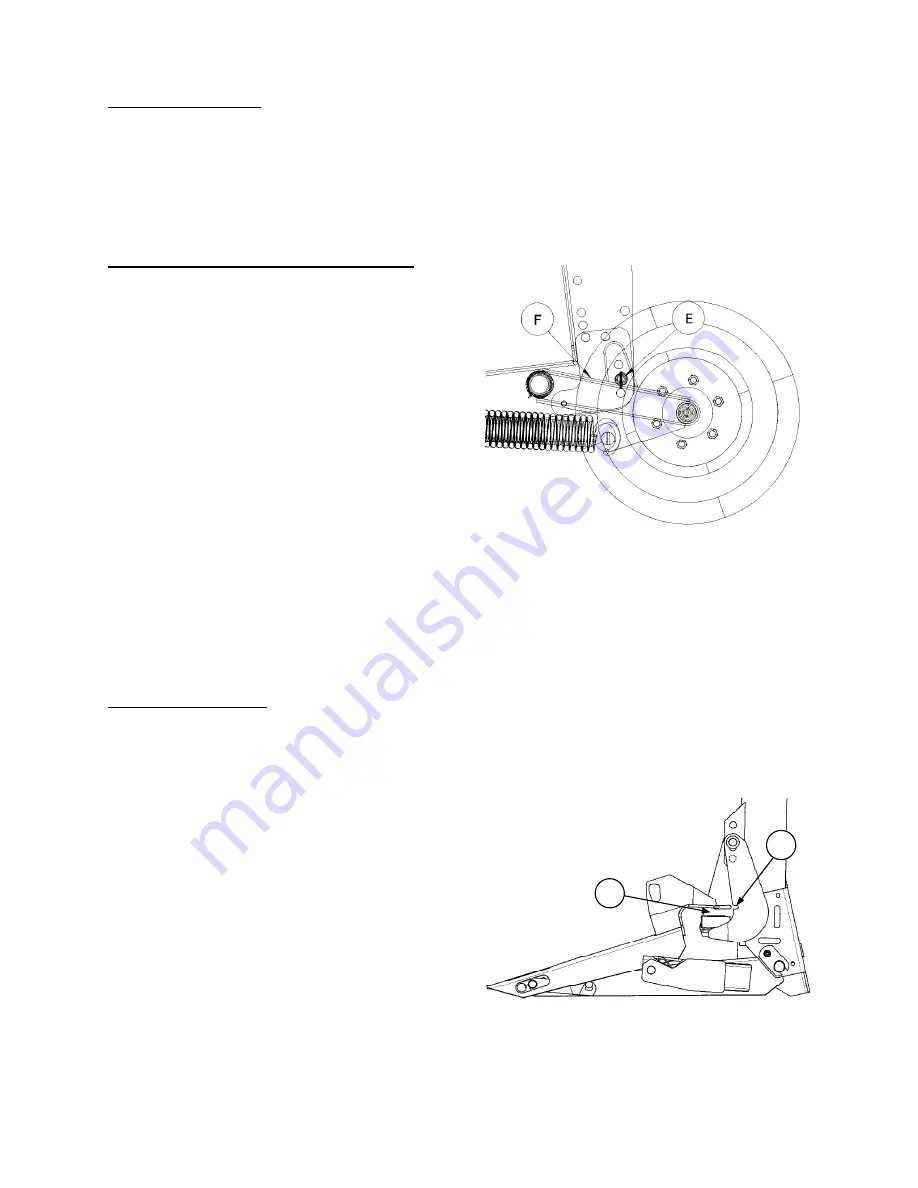
Form # 147083
Issue 01/07
22
1/2” (13 mm) GAP WITH HEADER 6” OFF
GROUND RESULTS IN 2” (50 mm) GAP WHEN
CUTTING ON GROUND FOR FULL FLEX
CAPABILITY
A
B
OPERATION
HEADER FLOTATION
IMPORTANT:
To avoid frequent breakage of sickle components, scooping soil, or soil build-up at cutterbar in
wet conditions, header float should be set as light as possible without causing excessive bouncing.
Under normal conditions, when cutting above the ground, adjust float spring tension so 50 - 70 lbs. force (225 -
315 N) is required to lift divider at either end. Cutting on the ground requires lighter float, approximately 30 lbs.
(135 N) at each divider point.
Setting float on headers with gauge wheels
Headers with gauge wheels use the springs in the
gauge wheel package to assist in header floatation.
As such, the float adjustment for these headers must
be set to take advantage of the extra flotation.
Proceed as follows:
1. Set gauge wheels to medium stubble height
position (E).
2. Set center link to approximately 21-1/2 in. (545
mm) pin to pin.
3. Adjust adapter float spring drawbolts such that
gauge wheel arm (F) contacts pin (E) when the
header is lowered. If header floats away from the
pin, reduce float. If arm (F) contacts pin but float
is heavy, increase float.
For 973 Headers, see "Header Flotation" in Combine
Adapter Operator's Manual for adjustment details.
FLOTATION ADJUSTMENT – 974 FLEX HEADERS
Initial setting of the wing float and adapter spring float is done at machine Set-Up. See “Assembly” section at
back of this book. The following covers field adjustments that may be required from time to time.
Cutting on the Ground
For cutting on the ground, best operation will occur with minimum extra weight on the header. Consider
removing gauge wheels or transport attachment, if equipped. If weight is added or removed from the
header, both wing float and adapter spring float may require readjustment.
Operating tips:
1. Set top link between adapter and header to mid-
range position (19-1/4”) (490 mm).
2. Ensure adapter float lockout is disengaged.
Adjust adapter float springs as described in
Combine Adapter Operator’s Manual so that gap
at (A) between float arm and down stop is 1/2” (13
mm) when cutterbar is 6” (150 mm) above
ground. Notch (B) is provided as an alignment
mark for this setting. This will result in about 2”
(50 mm) gap under normal “ground hugging”
conditions and float optimizer function.
Header
can flex to “full frown” only when gap at (A) is
around 2”
.
USE GAUGE WHEEL SPRINGS
TO ASSIST FLOTATION
Summary of Contents for 973
Page 2: ...Inside Front Cover blank...