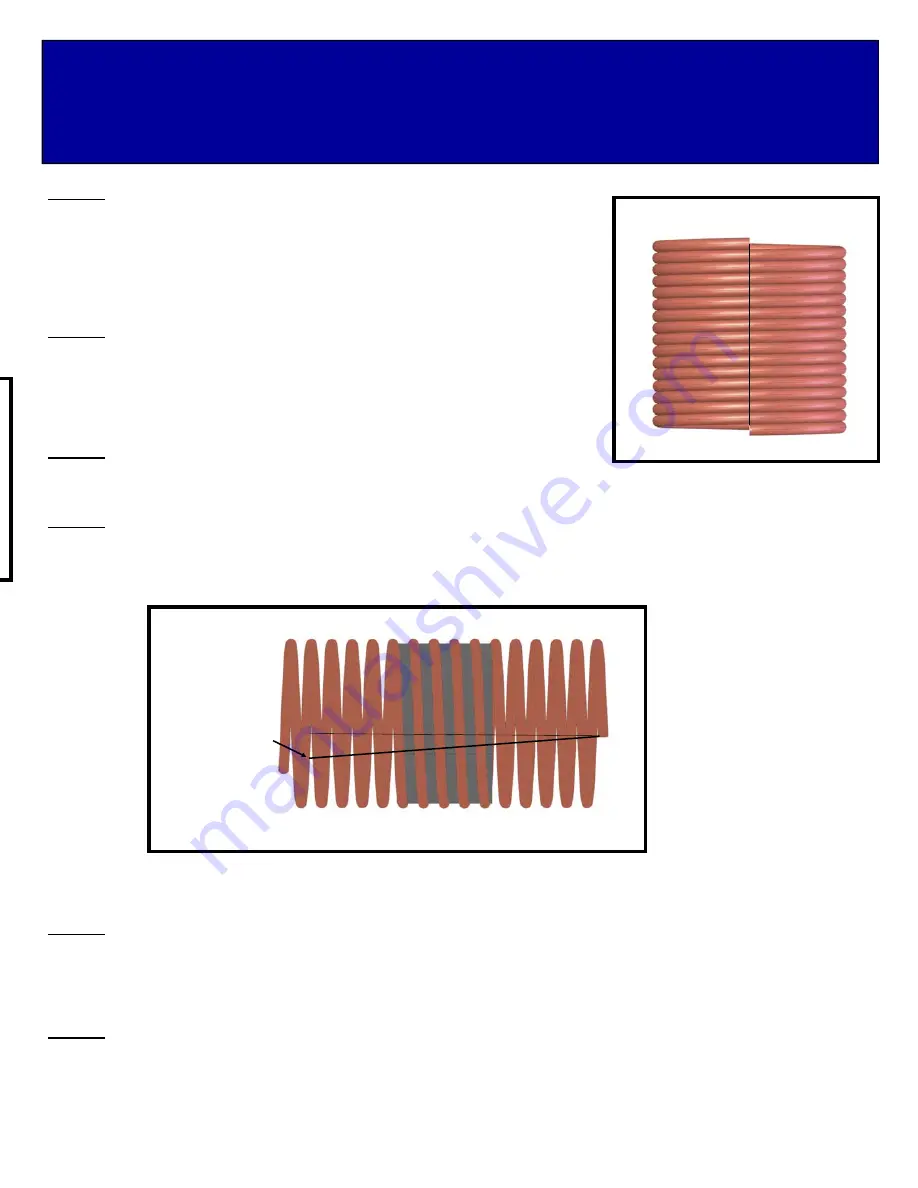
40M COIL ASSEMBLY
INSTRUCTIONS
STEP 1:
The coil comes wound tight with 16 total turns from the factory. The excess
material will be trimmed off after the coil is in its final position. Using a permanent
marker, draw a straight line from one end of the coil to the other. This will help later
to determine if your coil has grown in diameter during assembly. After final position-
ing of the coil no more 3/4 of an inch of line tilt is allowed. A larger coil will cause the
inductance to change which can cause your antenna to be off frequency.
STEP 2:
The COIL is wound tight at the factory to prevent damage during shipping. Use the
COIL SPREADING TOOL provided, and carefully insert it into the first turn of the
COIL. Now gently push or roll the tool through all 16 turns of the COIL. Now the
COIL is nearly in its final shape and is ready to be threaded onto the COIL SUP-
PORT. Note the reference line drawn earlier, it will have a slight tilt after spreading.
STEP 3:
On one end, use pliers to gently straighten the last 1/2” of the COIL and file
off any burrs.
STEP 4:
Begin threading the COIL onto one end of the COIL SUPPORT.
BE CAREFUL
to not deform the COIL during this
process. The COIL should thread smoothly. Continue until about 5-1/2 turns are past the COIL SUPPORT or close to the
center. Exact centering is not important. Again, note your reference line.
NOTE: PENETROX PASTE FOR LUBRICATING SCREW THREADS AND TUBING JOINTS HAS BEEN SUPPLIED. USE A VERY SMALL AMOUNT ON
EACH SCREW THREAD AND UNDER THE COIL POSTS DURING THE NEXT OPERATION.
STEP 5:
Insert the COIL INSULATOR (M2AFG0050) into your COIL SUPPORT (M2ACA1554). Rotate the COIL and the
COIL SUPPORT so the leading end of the COIL goes over and just past the inner hole in the COIL INSULATOR. Now slide
on one COIL POST on to one end of the COIL so it is right over the first hole. Next, carefully slide on the ELEMENT SEC-
TION #6 (M2AEP40MC-6) and align it so both holes in the tube match the two holes in the COIL INSULATOR.
STEP 6:
Insert hardware through the ELEMENT SECTION #6 and the COIL INSULATOR and begin threading it into the
COIL POST. Tighten hardware. Thread the SET SCREW into the top of the COIL POST and with about 1/2” of wire protrud-
ing past the COIL POST, tighten the SET SCREW gently. Use supplied ALLEN WRENCH to tighten the SET SCREW.
1/2” TO 3/4”
TILT