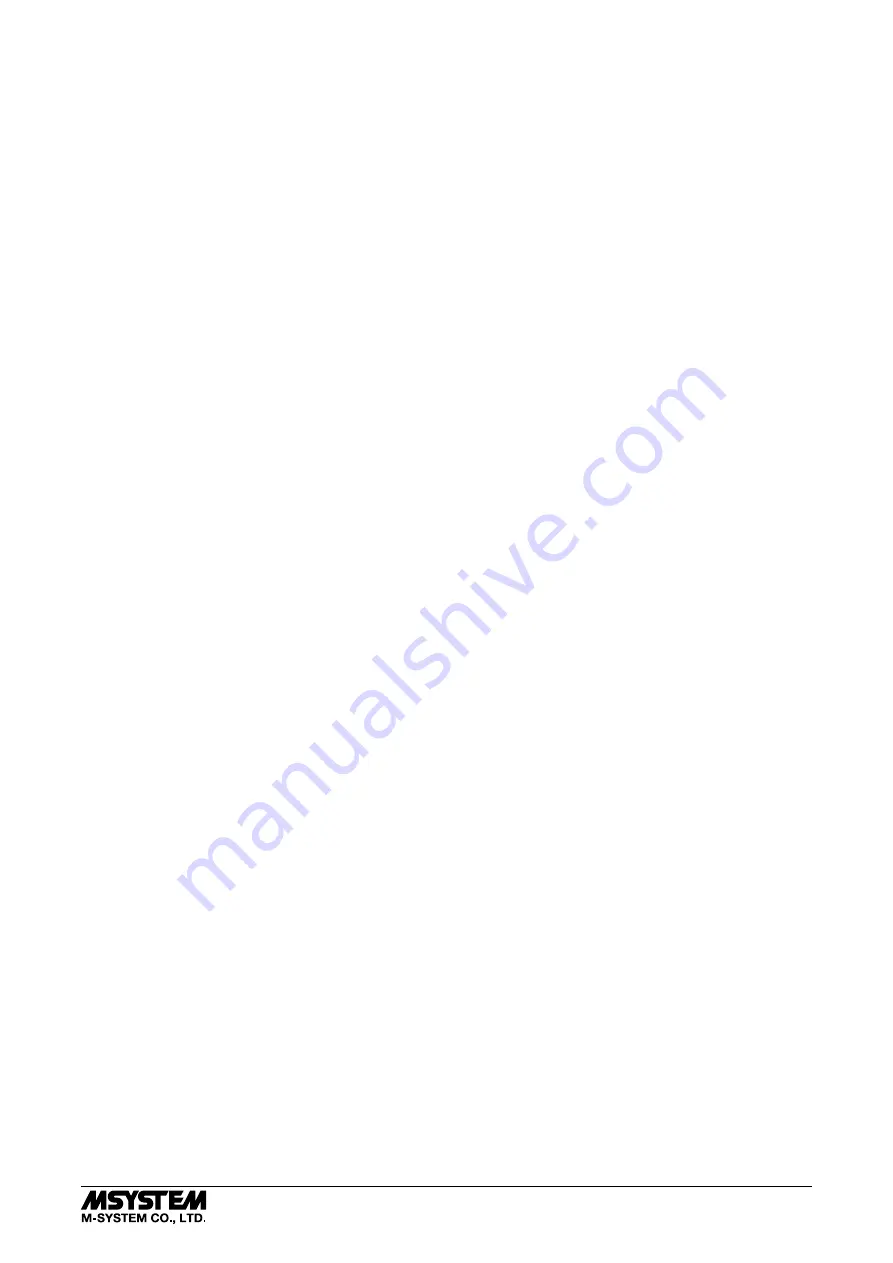
MRP10
5-2-55, Minamitsumori, Nishinari-ku, Osaka 557-0063 JAPAN
Phone: +81(6)6659-8201 Fax: +81(6)6659-8510 E-mail: [email protected]
EM-4889 P. 2 / 13
■
PID CONTROL SIGNAL
• Choose PID parameters carefully so that the MV remains
as stable as possible to prevent hunting. Unstable control
shortens the life of actuator and valve.
■
TRANSPARENT COVER FOR TERMINAL BOX
• When reattaching the transparent cover after wiring,
make sure that the packing and O ring are securely in
place.
■
SCREW TORQUE
• The torque for tightening screws for the transparent cov-
er is between 1.2 – 2 N·m (0.89 – 1.5 ft·lbf). The screws
must be tightened evenly and crosswise in several steps
to prevent uneven clamping.
■
YOKE DESIGN
• When a foreign object is caught in the valve, an excessive
torque may be applied to the yoke. Taking it into account,
design the yoke and joint so as to have sufficient margin
in strength.
• When this unit is used in an application such as temper-
ature control of a steam line, the temperature can rise
higher than the ambient temperature due to heat con-
ducted through or radiated from the piping. Use a longer
yoke for effective heat dissipation and apply insulation
material.
■
HEATER FUNCTION AT LOW TEMPERATURE
• Apply power voltage when the temperature is 0°C or un-
der. Sensor inside the unit is activated at 0°C or under,
and stepping motor starts heater function.
• A heater is incorporated to use under cold areas.
• Thermostat is incorporated to automatically heat when
27°C (±5°C) (80.6°F (±9°F) or lower, and automatically
stop heating when 39°C (±4°C) (102.2°F (±7.2°F)) or high-
er.
• Be sure to apply power voltage even when the MRP is
unused.
Note. Storage temperature (-29 to 70°C (-20.2 to +158°F))
is for before piping. Once the MRP is piped, the tem-
perature must be in the range of operation temperature.
When using the MRP at the first time in -25°C (-13°F),
apply the power voltage and take 30 minutes of hold time
before using the MRP.
■
COVER
• No need to remove the cover. All wiring, adjustments,
indicator LEDs are in the terminal BOX. Remove the
transparent cover to work.
• The quality inside the mechanism is stabilized by not re-
moving the cover.