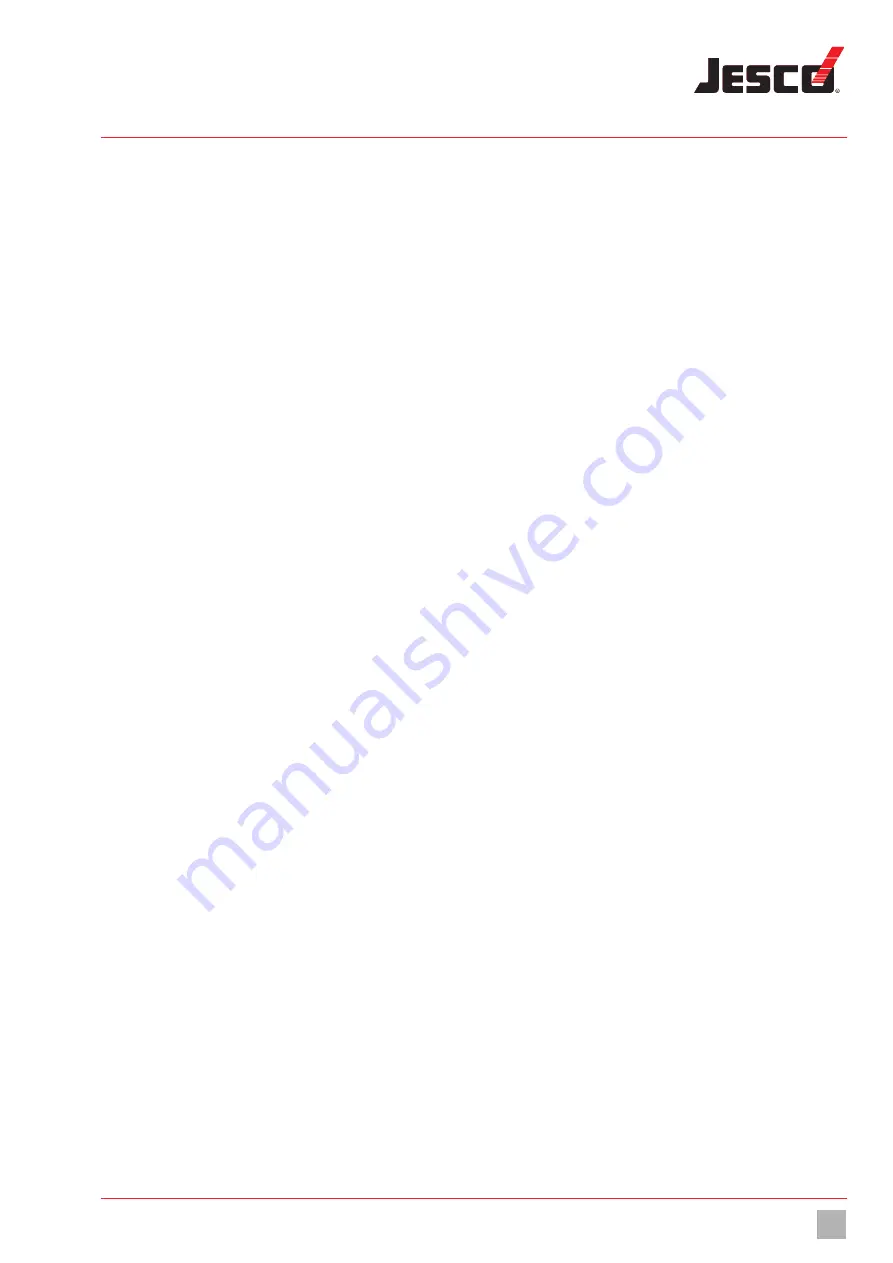
Notes to the Reader
Identification of instructions for action
5
© Lutz-Jesco GmbH 2014
Subject to technical changes.
140327
Solenoid-Diaphragm Dosing Pump
MAGDOS LP
Operating Instructions
BA-10231-02-V03
1.5 Identification of instructions for action
This is how pre-conditions for action are identified:
Pre-condition for action which must be met before taking action.
This is how instructions for action are identified:
Separate step with no follow-up action.
1.
First step in a series of steps.
2.
Second step in a series of steps.
Result of the above action.
Action completed, aim achieved.