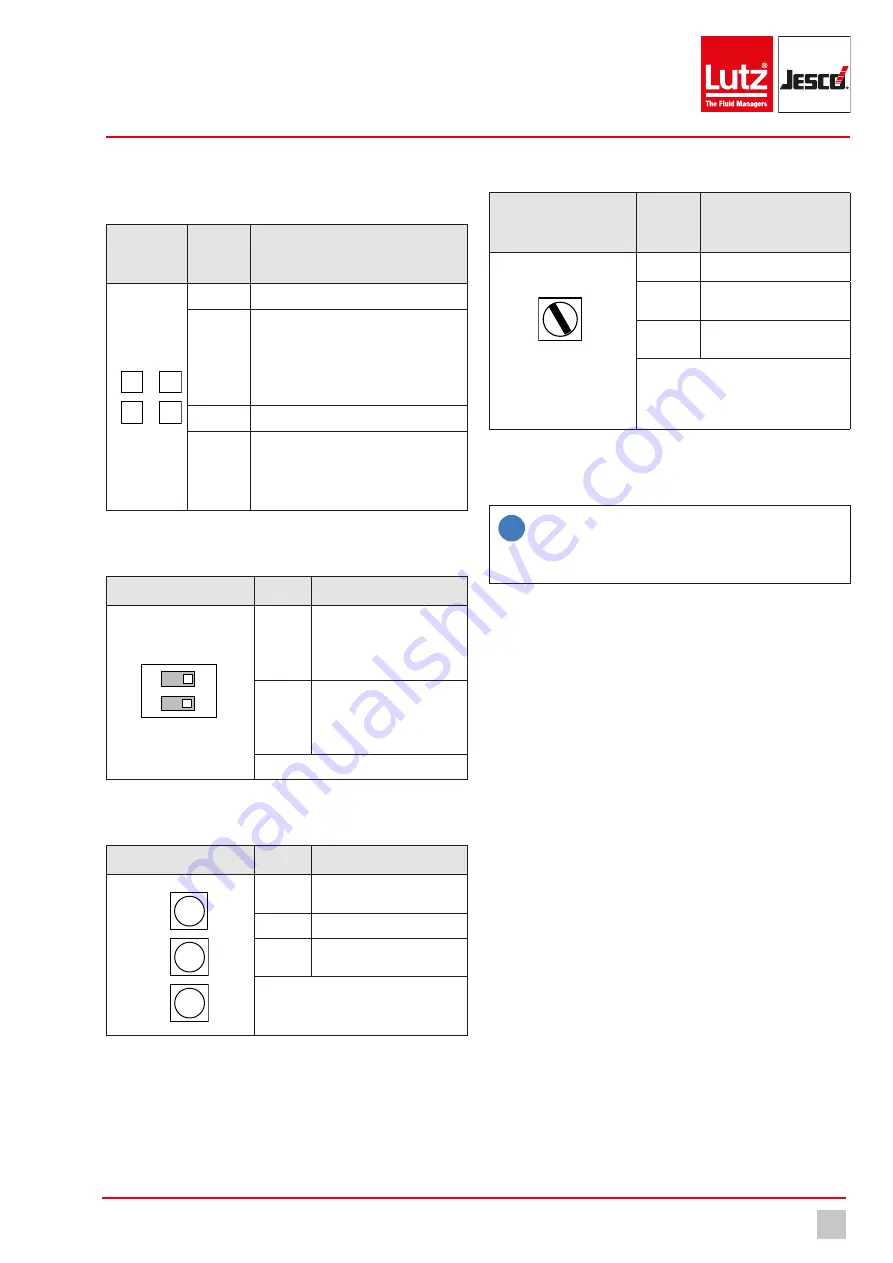
Servomotors
Servomotor 4-20 mA
21
© Lutz-Jesco GmbH 2017
Subject to technical changes.
170518
BA-20710-02-V05
Chlorine control valve
C 7700
Operating instructions
8.3.3 Operator controls of the servomotor
LEDs
LED
arrange-
ment
No.
(colour)
Meaning
R
L
4
3
2
1
1 (blue)
Operation
2 (red)
Fault
n
Voltage supply failure
n
Servomotor in manual operation
n
Current input below 2 mA
(if signal is 4-20 mA)
3 (yellow) Left-hand rotation active (close valve)
4 (green)
Right-hand rotation active (open valve)
Table 21: LED functions
DIP switch
Switch
Position
ON
1
2
1
Rotation direction of the
servomotor
left: 20 mA = valve closed
right: 20 mA = valve open*
2
Operating mode of the servo-
motor
Left: manual operation
Right: automatic operation*
* delivery state
Table 22: DIP switch functions
Keys
Arrangement
Key
Meaning
L
R
SET
L
Manual mode left-hand
rotation = close valve
SET
Program end position
R
Manual mode right-hand
rotation = open valve
The keys have no functions in automatic
mode
Table 23: Key functions
Hysteresis potentiometer
Direction
of
rotation
Position
Clockwise Increase hysteresis
Anti-
clockwise
Reduce hysteresis
R
Manual mode right-hand
rotation = open valve
The hysteresis is adjustable in the
0.1 - 2 mA range. If the setting is too
fine, the motor might run continuously
even with a stable input signal.
Table 24: Key functions
8.3.4 Programming the servomotor
i
The regulation bevel of the motor is 90° for a dosing capacity
of 0-100%. If the regulation bevel is greater, the feedback
potentiometer will shift during operation and the device will
not function reliably.
The servomotor is adjusted to a setting range of 0-100% in its delivery
state. A different setting is only useful in special cases.
Before you change anything on the servomotor, check if the counternut of
the adjusting spindle is tightened securely.
Perform the following working steps:
1.
Switch DIP switch 2 to manual operating mode.
2.
For a minimum and maximum dosing capacity, adjust the trigger
cams to the desired position. The rotary selector switches can be
adjusted by hand without tools.
4
Rotary selector switches adjusted.
3.
After adjusting the rotary selector switches, the motor must move to
both end positions. This allows the slip coupling of the potentiometer
to adjust itself. First, press the R button and keep it pressed until the
motor stops, then press the L button.
4
This adjusts the slip clutch on the potentiometer.
4.
Press and hold down the L key until the rotary selector switch turns
off the motor with the valve closed. Then release the L key.
5.
Press the SET key.
4
The blue LED flashes.
6.
Press the L key 1x within 3 s.
4
The blue LED turns off.
4
The end position 0% is programmed.
7.
Press and hold down the R key until the rotary selector switch turns
off the motor with the valve open. Then release the R key.
8.
Press the SET key.
4
The blue LED flashes.
9.
Press the R key 1x within 3 s.
4
The blue LED turns off.
4
The end position 100% is programmed.
inv.
Manu
Auto
Hyster.